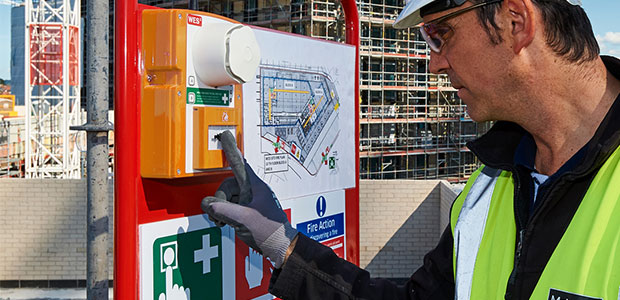
Features to Look for in a Temporary Construction Site Fire Alarm System
It makes good sense to have an adaptable, durable, highly functional alert system in place from the first phase of construction to the last.
- By John Newbury
- Feb 01, 2020
When 6.5 million construction workers report to work on 252,000 jobsites each day in the United States, they do so under the assumption that certain safeguards are in place in order to protect them. Their families are counting on it, too. The expectation is that no matter where a worker is onsite or what job they may be carrying out that day, they’ll be alerted and have the ability to alert others when—not if—an emergency occurs. With the rate of injuries, illnesses, and fatalities higher in the construction industry than most other industries, emergencies are an inevitable part of the regular routine. It makes good sense to have an adaptable, durable, highly functional alert system in place from the first phase of construction to the last.
The statistics for construction fires are harsh; the National Fire Protection Association (NFPA) reports that for each year between 2010 and 2014 there were 3,750 fires in structures under construction; 2,560 fires in structures undergoing major renovation; and 2,130 fires in structures being demolished in the U.S. These fires led to $310 million in direct property damage, claimed 13 lives, and injured 132 people during that time period. Most are attributed to heaters, welding, cutting, grinding, soldering, and/or accumulated construction materials and cardboard.
There’s no doubt that construction is an inherently high-risk industry, but in many cases the impact of emergency incidents can be minimized or, better yet, prevented from happening in the first place. The simple fact is that technology can help, and construction companies who are willing to explore new technologies and implement them into their projects are already seeing the benefits—both in terms of improved safety procedures onsite and the financial return. While there will inevitably be an initial cost of investment in the technology itself, the potential savings in terms of improved efficiencies, reduced lost-time injuries, and elimination of paperwork means a return on the investment is rapidly achieved for companies willing to adapt.
But how? Many challenges exist on an active jobsite that don’t necessarily need to be considered elsewhere. There’s an obvious need for new solutions in this area. Does such technology exist, and if so, what should a safety professional be looking for to ensure the investment pays out in the best way possible? When choosing such a system, there are several factors to keep in mind.
Construction Sector’s Unique Demands
Ideally an alarm system for a construction site would be wireless with a strong, long-range signal to alert everyone onsite, built for the unique demands of the construction sector. Because most alarm systems are battery-powered, the batteries should have several years of operational life under normal conditions before a change is required. The system should have the ability to be activated at any point, and to be loud enough to be heard across every corner of the site, because the traditional reliance on hand bells, whistles, and airhorns is simply not an appropriate measure for today’s large, complex construction sites. It should have the ability to distinguish between smoke and dust in order to eliminate false alarms.
Look for an optional inspection delay to enable site managers to establish whether a false alarm has been raised, and to undertake a staged evacuation process. Units should be able to be added, repositioned, or removed from the network at any point, suited to the constantly changing landscape of a construction site. Also, the system must be rugged enough to withstand the abuse that equipment is typically subjected to on a construction site.
Rapid Deployment
In order to eliminate downtime and frustration, an alarm system should be quick and easy to install. Make sure that assistance from the manufacturer or supplier is readily accessible, whether virtually or in person, and that simple instructions are included with the product. The units should be able to be numbered and attached to drywall, wooden or metal framing, or to posts specifically placed in accordance with your fire plan. Deploy units the moment the building is out of the ground, and add more as each stage progresses.
Mobile Implementation
In the event of an emergency, whether it’s fire, gas leaks, flooding, medical emergency, or another significant event, the system should be able to be triggered from any device onsite, including a smartphone. It should create an invisible, wireless radio mesh network across the site at the touch of a button. In the case of a medical alert, the system should inform relevant personnel of the time and specific location of which device has been activated, so medical support can be immediately and accurately directed to the incident and medical assistance provided. Project management teams should be able to rely on accurate, real-time alerts to make decisions, and when needed, raise a site-wide alarm.
Invest in Compliance
Since some areas require construction sites be monitored during off-hours when sites are unoccupied, it’s important to have smoke and heat sensors that activate automatically so that an emergency response can be actioned in the fastest possible time. Another advantage would be the capability for third-party devices such as code-mandatory standpipe monitors and access control systems to be easily integrated with the network using a simple interface unit. For investigation, insurance, and management of any potential litigation, it would be especially useful if all of the data generated on site could be stored in the device to be used after the event.
These features all combine to give a single, overall protection system that monitors a range of risks across the site, and ensures site managers are able to make high-pressure decisions using accurate, real-time data.
With such a high concentration of manual activity, in a high-pressure environment where the risks and hazards are continuously changing, construction is inherently high-risk. Commercial pressures mean timescales for delivery are getting tighter and tighter, building programs are becoming more and more complex, penalties for late or unsatisfactory delivery can in some cases be crippling, and obligations regarding compliance, insurance and audits are becoming more and more onerous. Managing safety, health and environmental obligations under such challenging conditions is a constant battle for construction management teams. Communication is the key, and being able to alert your team members to disasters as they arise is priceless.
This article originally appeared in the January/February 2020 issue of Occupational Health & Safety.