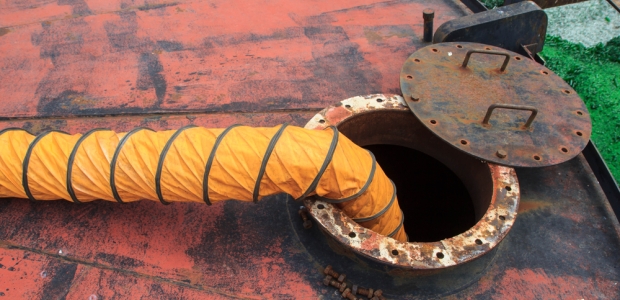
The Complexities of Confined Space Safety
Once a space is designated a permit-required confined space, it engages an extra level of planning and preparation to mitigate the potential hazards.
- By Baxter Byrd
- Jul 15, 2019
Confined spaces by any relative measure are complicated affairs. Few endeavors involving fall protection pose such dangers not only for the participant, but also those tasked with monitoring the situation or performing rescues. Given the potential amount of personnel, equipment, and additional expertise a confined space operation may require, getting off on the right foot goes a long way to ensuring a safe environment for your workers.
To Permit or Not to Permit?
OSHA defines a confined space as an area that:
1. Is large enough for an employee to enter fully and perform assigned work;
2. Is not designed for continuous occupancy by the employee; and
3. Has a limited or restricted means of entry or exit.
A confined space that fits this description is considered a non-permit-required work area. And although workers must take extra care when working in these spaces, the space itself poses no direct health risk to workers. When the conditions within the confined space do pose a direct health risk, OSHA considers these areas to be permit-required confined spaces.
Like a non-permit-required confined space, there are certain identifiable traits of a permit-required confined space. OSHA identifies those as:
1. Contains or has the potential to contain a hazardous atmosphere;
2. Contains a material with the potential to engulf someone who enters the space;
3. Has an internal configuration that might cause an entrant to be trapped or asphyxiated by inwardly converging walls or by a floor that slopes downward and tapers to a smaller cross-section; and/or
4. Contains any other recognized serious safety or health hazards.
Once a space is designated a permit-required confined space, it engages an extra level of planning and preparation to mitigate the potential hazards.
The entry permit contains a comprehensive accounting of personnel, intended purpose of entry, means and methods of hazard abatement, rescue procedures and contacts, and a host of other important information, including a specific duration of work. A confined space operation is not an open-ended affair, and an entry permit is valid for a specific amount of time only. If additional time is needed, the permit must be updated or a new permit must be issued. In addition, any time the confined space environment changes to something other than what is addressed on the permit, the permit must also be updated or a new permit issued.
Given the high degree of variability of conditions in a confined space, it is quite possible for the parameters of a permit to change mid-work. Fluctuations in atmospheric oxygen are one such example where a permit may need to be updated.
The average atmospheric oxygen level is around 20.9 percent. If an inert gas, such as nitrogen, were introduced into a confined space and the oxygen level dropped below about 16 percent, workers would suffer hypoxia, which can cause accelerated heartbeat, nausea, poor judgment, and fatigue. Once the oxygen level dropped below 10 percent, workers would fall unconscious. If the oxygen level rose above 23.5 percent (perhaps due to a faulty shut-off valve somewhere), the space would be considered oxygen rich, a condition that creates the potential for combustion. In a nutshell, altering a single factor (oxygen level) can shift the risk from one problem of unconsciousness and loss of motor skills to one of combustion. Because the remediation procedures for an oxygen-rich versus oxygen-depleted space are different, the permit must be updated to reflect the changed environment.
Non-Entry vs. Entry Rescue
Parallel to pre-planning a confined space operation is planning for a potential rescue situation in which the worker becomes incapacitated or otherwise unresponsive. Just as confined space work is generally separated into two types—permit-required and non-permit required—rescue operations also generally fall into one of two categories—entry and non-entry.
A non-entry rescue is one in which the rescue of the worker is facilitated by rescue personnel located completely outside of the confined space. They rely on overhead anchors, tripods, side-mounted davit arms, winches, remote connection poles, or a host of other devices to extract the worker. Non-entry rescues are by nature limited in their scope because relatively small condition changes can mean a non-entry is infeasible. For example, a worker moving around a 90-degree corner in an HVAC shaft seems nearly inconsequential until the worst happens. That simple 90-degree turn means a direct-connect option is no longer available, and what may have been a relatively straightforward rescue before the turn suddenly becomes exponentially more dangerous, not only for the victim, but for the rescuer, as well. The non-entry rescue has now become an entry rescue.
Entry rescues are rescues in which additional personnel must enter the confined space to effect the rescue of a fallen worker. They can be incredibly dangerous operations. In fact, OSHA reports that "where multiple deaths occurred, the majority of the victims in each event died trying to rescue the original entrant from a confined space." This means that rescuers, not the victims themselves, comprise the majority of deaths in instances of multiple victims. Granted, in many of these cases, the rescuers were "untrained or poorly trained." They were not fully trained experts, merely other workers who tried to extract the victim from the confined space and were overcome by fumes or other factors. The point here is that lack of a properly developed rescue plan, one that considers all possibilities, can be a very deadly thing.
The number of potential situations to consider precludes mentioning their solutions individually, but suffice it to say that confined space operations can be some of the most complex problems to solve due to the nature of threats posed to the worker and the fluidity of those threats over time. From access to engulfment, ventilation to fire abatement, pre-entry testing to constant monitoring, the name of the game in confined work is careful pre-assessment of not only known hazards and procedures, but also consideration of those not only present, but possible.
This article originally appeared in the July/August 2019 issue of Occupational Health & Safety.