New Considerations for Selecting Flame-Resistant Workwear
In a real-world fire emergency, chances are that workers will need to flee to safety, so it is critical that FR workwear continue to provide coverage and allow mobility to protect workers after a flash fire or arc flash.
- By Caroline Holtzman
- May 01, 2019
Millions of people across the globe go to work each day in environments with a heat or fire hazard. For these workers, flame-resistant (FR) or flame-retardant treated (FRT) protective garments are designed to provide a last line of protection against short-duration fires. Many different fibers can be used to make FR or FRT garments, each with their own advantages and disadvantages. With so many options, it can be difficult to select the best product for each specific job function.
There is growing industry awareness about the importance of knowing how a garment will perform not only at the moment of heat or fire exposure, but in those vital seconds just after exposure when an employee needs to escape from the emergency.
Safety Expert Shares Process
A highly regarded industry safety expert who specifies and selects garments for a Fortune 50 oil and gas company recently shared with me the process he uses for FR garment selection. Like most safety professionals, he considers certification to key industry test standards and published performance results as a minimum requirement.
He prefers to witness actual burn testing of the garments and analyzes the results for himself. But he doesn't just stop there because he knows that the test methods simply establish minimums for performance and the live burn tests are conducted on a stationary manikin. As he explained, in the real world, a flash fire or arc flash is a dynamic event that either generates motion in the individual from the pressure wave or blast or from the worker's reaction to protect himself as he flees from the event. That's why he now considers the state of the garment post burn as a mandatory part of the selection process.
Is the garment still intact so it continues to offer protection? Is it flexible enough that, in a moment of crisis, an employee still has mobility to quickly escape heat and flames? If the garment passes this test, he then relies on extended-duration field wear trials to confirm a garment's durability, ease of cleaning, comfort, fit, style, and buy-in from workers who will be wearing the garments on a daily basis.
The Difference is In the Fiber
What properties determine how a fabric will perform after exposure to a thermal event? The answer has to do with the makeup of the fiber and fabric.
Fibers used for FR garments are either inherent or non-inherent. The term inherent is a scientific textiles term spelled out in the definitions sections of FR workwear standards NFPA 2112, NFPA 1975, NFPA 1971, and Canadian standard CAN155.20. These North American industry standards define inherent flame resistance as "flame resistance that is derived from the essential characteristics of the fiber or polymer."1
Inherent fibers are made of substances or materials that are not flammable; do not support combustion in air; and do not provide fuel for a fire, either with or without an ignition source. The thermal protection of inherent fibers is permanently part of the fiber chemistry and goes completely through each fiber strand—end to end, from the outer surface down to the core. The solid layer of fire resistance of inherent materials cannot be stripped off, washed out, or worn away, no matter how the garment is used or laundered. If the fiber is still present, the FR protection is still there.
Inherent fabrics:
- are self-extinguishing in air
- can withstand elevated temperatures for long periods of time without degrading or changing
- will not melt or drip when exposed to high temperatures or fire
Commercially available inherent fibers used for high-temperature garment applications include: meta-aramid, para-aramid, carbon, PBI (polybenzimidazole), and PBO (polybenzoxazole).
Non-inherent fibers, which are flammable in their natural state, include: cotton, nylon, polyester, and fibers made from cellulosic plant materials such as rayon, modal, or lyocell. When exposed to heat or flame, non-inherent fibers become fuel for the fire. To make a non-inherent material flame retardant, a chemical must be added to the mix before the fiber is spun in the production process, or a chemical must be applied to the outer surface after the fibers have been woven or knitted into a fabric.

Considerations Beyond Certification
The personal protective equipment (PPE) marketplace is full of commercially available FR workwear options certified to the two main North American thermal apparel standards: NFPA 2112-2018 and ASTM F1506-2017. Fabrics, sewing thread, labels, and closures must pass multiple and rigorous test standards to achieve certification. But it is important to remember that a lab environment can never perfectly replicate the real world.
One shortcoming of the certification process is consideration for how FR clothing might perform in motion (the wearer moving to safety) after exposure to heat, flame, or fire. Manufacturers of FR workwear hope that their products are never needed for a fire emergency; however, if they are needed, they must provide continuous protection until the wearer can escape from the hazard. This means an FR garment needs to stay intact and flexible so an accident victim can maintain mobility and protection.
A very effective method of flame retardancy used with treated cotton, cotton blends, or other plant-based fabrics converts the organic material in the fabric to a carbon char. This chemical process absorbs heat; releases carbon dioxide and water; makes the cotton unavailable as a fuel; and the char blocks heat from the body, all of which provide protection in a thermal emergency. One downside to this process is that this chemical reaction is exothermic or produces heat, which can add to the burn injury. Another problem is that the formed carbon char is brittle and does not have the strength or integrity of the original fabric. Even slight motion after exposure can cause the fabric to flake and disintegrate. Inherent fibers can withstand higher temperatures and greater levels of heat energy before physical changes take place, allowing the fabric to stay stronger and flexible for longer.
This structural integrity after heat or flame exposure is not reflected in a certification test report and can be seen only by witnessing an actual exposure. Tests have been conducted to gauge the level of fabric integrity and flexibility remaining in fabrics after testing using the industry standard thermal manikin test ASTM F1930.
As shown in these photos, the test manikin was dressed in a 7 oz/yd2 non-inherent FRT 88/12 cotton/nylon blend shirt paired with 6 oz/yd2 inherent pants. Both garments were received new and then washed and dried in one home laundering cycle using AATCC 135 industry recommended wash and dry procedures.
The clothing was exposed to test standard 2 calories/cm2 of heat energy for three seconds. Both the shirt and pants that were tested are commercially available certified garments. Test data shows that both garments would be well below the maximum total predicted burn injury (TPBI) percent required for a certified garment.
After exposure, the garments were very carefully removed from the test manikin to minimize damage to the fabrics. What the test report does not show, but what is clearly evident in these photos, is that the non-inherent shirt became brittle and broke into fragments. In sharp contrast, other than a color change due to the fabric dyes being exposed to high temperatures, the inherent pants were still flexible enough to crumple into a ball multiple times and stayed fully intact with no breaks, holes, or tears.
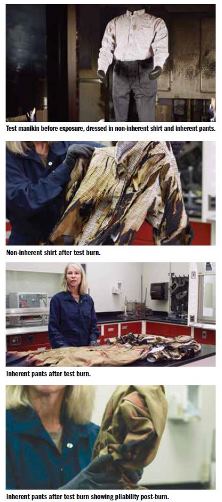
Real-World Implications
In a real-world fire emergency, chances are that workers will need to flee to safety. A recently published study from the American Gas Association shows that workers may need up to six seconds to safely escape from a flash fire.2 Therefore, it is critical that FR workwear continue to provide coverage and allow mobility to protect workers after a flash fire or arc flash.
Inherency Means Peace of Mind
The bottom line when it comes to selecting FR workwear is that inherent FR products help give you peace of mind. That's because you can be confident that if a garment is intact (no holes or worn-through areas), the FR properties of inherent materials are intact.
On the other hand, FRT fabrics can have their FR properties diminished or severely compromised depending on how they are laundered; how many times they are laundered; or with exposure to certain chemicals in the laundering process or work environment. In fact, garment labels are commonly found in non-inherent workwear carrying multiple warnings: not to use bleach or hydrogen peroxide; that improper laundering can adversely affect the flame resistance of the fabric; or garments can lose flame-resistant properties if not laundered and maintained according to manufacturer instructions.
Unfortunately, there is no quick, easy test to confirm that the FR protection is still present in a non-inherent garment without destroying it. Further complicating the situation is the fact that the wear and tear a garment experiences in the field and through washing is highly variable, making it difficult to know when to retire it.
The key thing to remember is that with inherent materials, if the fabric is there, the built-in flame resistance is there. It's that simple.
This article originally appeared in the May 2019 issue of Occupational Health & Safety.