How to Conduct a Safety Inspection Remotely
Remote inspections can be an alternate and effective way to conduct a safety inspection.
- By Ann Rivers
- May 01, 2019
Workplace inspections are a legal requirement and a necessary component of an effective occupational health and safety program. Routine inspections help to identify existing and potential hazards so that corrections can be made. Corrections include implementing controls, such as elimination, substitution, engineering controls, administrative practices, and/or personal protective equipment. Inspections also allow workers to discuss their concerns about safety.
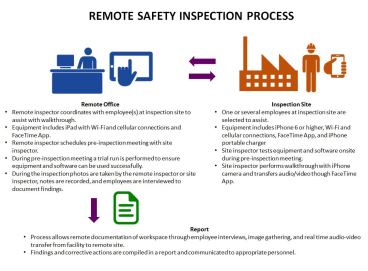
It may not be convenient or possible for a safety inspector to travel to conduct an on-site safety inspection. Time, resources for travel, security, safety, and physical limitations may limit the ability to travel to the inspection site. Remote inspections can be an alternate and effective way to conduct a safety inspection.
This article discusses how to conduct a remote inspection using a tablet (iPad), smart phone (iPhone), and audio-video software (FaceTime App).
Equipment and Software:
- iPhone 6 or higher model with Wi-Fi and cellular connections and FaceTime App
- iPhone portable charger (optional)
- iPad with Wi-Fi and cellular connections and FaceTime App
- iPad stand
Method:
The remote inspector should coordinate with another employee at the inspection site and ensure the employee is available for the duration of the inspection. In many instances, this may mean getting approval from a supervisor or manager; the employee may have other duties that must be delayed or delegated to another employee during the inspection.
Depending on the nature of the inspection, it may be preferable to work with one or several employees at the site. The advantage of using one employee is that less time is spent on training, and the employee may grow more proficient with time. There may be a single reliable or knowledgeable employee at the site that is best suited for the inspection. The advantage of using several employees is that less time away from the employee’s normal work duties is needed, and each employee may be more knowledgeable about his or her own work area.
The remote inspector and site inspector should schedule a pre-inspection meeting. Instruction should be provided to the site inspector regarding how to properly use the software and equipment. A trial run is necessary to ensure the equipment and software works and to ensure the site inspector can successfully use it. The points below can be reviewed during the pre-inspection meeting.
- The remote inspector should position the iPad with a stand to stabilize it for the duration of the inspection. A quality image of the inspector's face should be transferred to employees on site who will be interviewed. The remote inspector should use an iPad rather than an iPhone because the screen is larger and details are better viewed. Although the site inspector may use an iPad, an iPhone is more manageable and more portable.
- The operating system of each device (iPad and iPhone) should be updated to the latest or equivalent operating systems. (Go to "settings," "general," "software update.")
- Each device (iPad, iPhone) should be fully charged prior to the inspection. The iPhone 6 or higher will generally provide two hours of audio-video fully charged with working batteries. It may be optimal to use a portable charger for the iPhone to increase battery time.
- Use the FaceTime App for audio-video communication. To ensure optimal resolution and prevent delay in transfer time, Wi-Fi should be utilized. There may be instances when Wi-Fi is lost but cellular is still available. If Wi-Fi is not available or is partially available, cellular technology is adequate.
- The inspector should turn the camera lens around using the lens on the back of the phone when showing details of the facility (use the flip arrow icon in FaceTime). The camera should be turned to the front lens when the remote inspector is interviewing personnel at the site.
- Photos can be taken directly by the remote inspector through the FaceTime App or by taking screen shots. The site inspector may also take and send photos to the remote inspector.
- Discussing camera movement terms may be helpful (slowly pan or move right, left, up, or down or zoom in or out). Instruct the site inspector to move the camera slow and steady for optimal video.
- Emphasize to the site inspector the importance of watching where he or she is walking or stepping to avoid trips/falls. Site inspectors must keep their eyes on the walk path at all times, not on the iPhone.
Once the remote inspector and site inspector work through the above details during the trial run, they should be ready for the inspection. In some instances, periods with no Wi-Fi or cellular connection or delayed audio or video transfer may present a challenge, but it is generally not a significant barrier to completing an effective inspection.
Conclusion
When time, resources, security, safety, or physical limitations limit the ability for a safety professional to conduct an on-site inspection, a remote inspection can be an effective alternative. The technology and method described in this article allow remote documentation of the workspace through employee interviews, image gathering, and real-time audio-video information transfer from the facility site to the remote location. The findings and corrective actions can be compiled in a report and communicated to appropriate staff.
This article originally appeared in the May 2019 issue of Occupational Health & Safety.