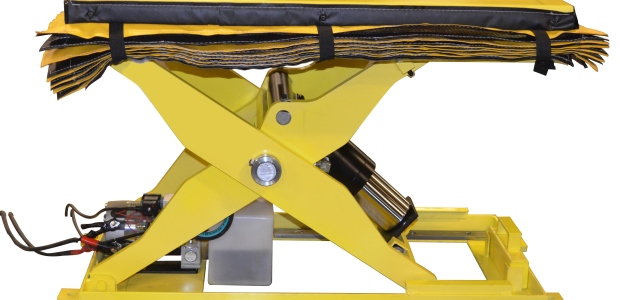
Making the Business Case for Ergonomic Materials Handling Lift Tables
The business benefits of ergonomics extend beyond the management of musculoskeletal disorders.
- By Thomas R. Cutler
- Oct 01, 2018
Ergonomic lift tables and work positioners for pallet handling, assembly work stations, welding booths, and adjustable height worker platforms are transformative in improving safety and productivity.
While there are many ergonomic lift tables and work positioners on the market, selecting the correct ergonomic equipment depends on the application. Vendor expertise adds value to the selection process to be certain ergonomics are properly addressed as well as cycle times and duty cycles that will speed production and productivity.
Boosting facilities' efficiency and productivity, while protecting employees, mandates manufacturers stop forcing the worker to fit the task. According to John Murdoch of Alfacon Solutions, which offers custom-built, engineer-to-order lift tables, "Ergonomics must be included into lift table designs allowing the task to fit the worker. Typical applications include lifting a worker or the item to the appropriate height to comfortably complete a task. Selecting the correct ergonomic product for manufacturing or warehousing workforce is a hallmark of 2018 materials handling."
Employees at risk of injury at a facility can cause additional workers' compensation costs, increased benefits usage, and downtime by cutting corners when ergonomically innovative industry products are readily available.
Plant managers, operations managers, industrial engineers, manufacturing engineers, and health and safety coordinators recognize that ergonomic lift tables improve the bottom line.
Lean Six Sigma and the Ergonomic Conversation
Because more than 70 percent of all manufacturers have a formal or informal lean manufacturing or lean Six Sigma initiative, the implementation of Define-Measure-Analyze-Improve-Implement-Control (DMAIIC) methodology related to ergonomics cannot be overestimated.
And because a lean enterprise views itself as part of an extended value chain, focusing on the elimination of waste between manufacturers, suppliers, and customers while supporting safety is a worthy conversation.
Murdoch also argues that too often, operations and safety professionals have been denied money for ergonomic improvements and grow discouraged. Because ergonomic products are often seen as a cost and antithetical to lean, many have seen their strategic ergonomic plan unsupported by upper management.
"Knowing how to capture the financial benefits of ergonomic initiatives and the ability to perform a cost benefit analysis is essential in today’s business climate to demonstrate how ergonomic solutions affect the bottom line. Few lift table companies assist in developing a comprehensive cost-benefit analysis to justify the ergonomic solution," Murdoch noted.
The business benefits of ergonomics extend beyond the management of musculoskeletal disorders. Through the integration of ergonomics into business processes, improvements in quality, efficiency, employee satisfaction, and profitability are also realized. Using participatory ergonomics and macroergonomics strategies, ergonomics can be integrated into other initiatives such as Six Sigma, total quality management (TQM), sustainability, safety, and support in achieving business objectives.
This article originally appeared in the October 2018 issue of Occupational Health & Safety.
About the Author
Thomas R. Cutler is the President & CEO of Fort Lauderdale, Florida-based, TR Cutler, Inc. (www.trcutlerinc.com). Cutler is the founder of the Manufacturing Media Consortium including more than 6000 journalists, editors, and economists writing about trends in manufacturing, industry, material handling, and process improvement. Cutler authors more than 500 feature articles annually regarding the manufacturing sector and is the most published freelance industrial journalist worldwide. Cutler can be contacted at trcutler@trcutlerinc.com and can be followed on Twitter @ThomasRCutler.