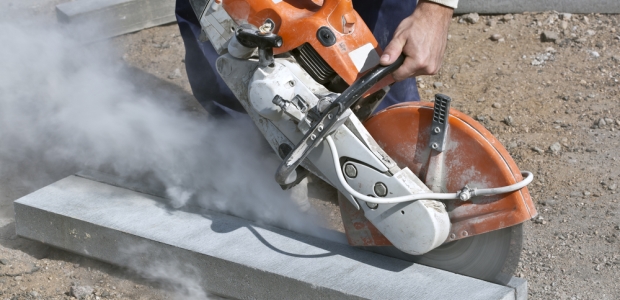
Respirable Crystalline Silica: Regulations and Considerations
OSHA requires that engineering controls be used to achieve necessary exposure reductions unless infeasible; organizations may not simply issue respirators and "be done with" their attempts to lower exposures.
- By Greg Zigulis
- Jul 01, 2018
Many people have heard of changes to the OSHA respirable crystalline silica (RCS) regulations and know that the OSHA "“compliance" dates vary based upon industry. However, not everyone may have had a chance to follow the topic closely. If your company conducts work that may result in employee exposures to RCS that could exceed the OSHA Action Level (25 µg/m3 on an eight-hour time weighted average basis), the following paragraphs present an overview of relevant points and share some program considerations.
Why the Revised Standard?
OSHA believes that employees exposed to respirable silica at the permissible exposure limit (PEL) set in the old standard faced "a significant risk of material impairment to their health." It estimated that there are 2 million construction workers and 300,000 in general industry and maritime workers impacted. The potential health effects that can result from certain levels of exposure might be surprising:
Various industries have argued "against" the appropriateness of the revised standards for feasibility and other reasons, but OSHA's opinions have prevailed in court.
What is Respirable Crystalline Silica and Where Is it Found?
Silica (silicon dioxide/SiO2) can exist in crystalline or non-crystalline form. The standard is intended to provide protection from exposures to the crystalline form, when it exists in or is made into an especially small size, referred to as "respirable." "Respirable" particles are those of a size (approximately less than 10 µm) that when inhaled have the potential to reach the deeper regions of the lung. OSHA-required exposure assessments must be conducted with respirable particle size selective samplers meeting International Organization for Standardization (ISO) 7708:1995.
α-Quartz is the most abundant crystalline form and is found in sand, sandstone, shale and granite. Other forms listed in the standards are cristobalite and tridymite. Within general industry, RCS exposures may be created from abrasive blasting, manufacturing (cement and brick, asphalt/pavement, china and ceramics, dental supplies, steel and foundry industries), hydraulic fracturing processes, and other sources. You can find out if products of potential concern contain or may contain crystalline silica by consulting industry publications, reviewing safety data sheets, communicating with manufacturers and/or conducting laboratory tests.
Regulatory Status
The Federal standard for respirable crystalline silica in construction (29 CFR 1926.1153) is already in effect. Many construction-related organizations have developed information tools either for their membership or the public, many of which can be easily found on the Internet. This includes Associated General Contractors of America (agc.org), the Center for Construction Research and Training (https://www.silica-safe.org/), and others.
The General Industry version of RCS standard, (29 CFR 1910.1053, Respirable Crystalline Silica) seems to have received less attention to date, perhaps since it has an OSHA compliance date (June 23, 2018, with certain exceptions) that is later than that for construction, and due to litigation against OSHA. Some organizations have held off on implementing the new standard, hoping that the standard would be overturned or changed. However, all but one element of a key lawsuit that had been at the U.S. Court of Appeals for the D.C. Circuit has been upheld, with only one item sent back to OSHA for further evaluation. (This one item pertained to the lack of a medical removal provision in the standard.)
The result: While there could be a delay in compliance obligations dates, at least the bulk of the standard will remain in effect, including impactful requirements.
Some Highlights from the GI Standard
The general industry standard includes, among other things:
- Revised exposure limits. The new Action Level (AL) and Permissible Exposure Limit(PEL) for respirable crystalline silica are 25 µg/m3 and 50 µg/m3, respectively. Companies that "used" to be compliant may no longer be.
- More detailed requirements to conduct exposure assessments (initial as well as periodic if dictated by prior monitoring and also triggering events).
- The establishment of "regulated" areas with specifically worded DANGER signs where exposures may exceed the PEL.
- Requirements that employers use engineering and work practice controls to reduce exposures to below the PEL, and until they do, to provide respiratory protection.
- Requirements for the development of a written exposure control plan with specified content, when exposures may exceed the AL.
- Requirements for respiratory protection (but not as the primary or sole method of reducing exposures).
- Where RCS exposure is an issue, prohibitions on dry sweeping/brushing unless wet sweeping or HEPA vacuums are not feasible, and on the use of compressed air to clean clothing or surfaces unless used in conjunction with a ventilation system that captures the dust.
- Medical surveillance provisions. The standard requires the offering of medical monitoring; the monitoring content goes beyond what is required for respirator clearances.
- Specific communication on silica hazards.
- Recordkeeping (exposure assessments and lists of persons exposed, data sheets, etc.).
Some Points to Highlight
There are many requirements in the standard; one must read it to ensure compliance. However, a few key points include:
Exposure assessments: The value of your exposure assessments could get lost in the shuffle, especially if employees work interchangeably throughout a facility, pull from utility teams, or have tasks that create exposure for only a small fraction of the work day. A cross-reference chart showing job categories, task(s) conducted during sampling, and related air sampling can be of value for longer-term tracking and compliance assurance.
Air sampling devices need to be selected carefully based upon likely exposure levels, nature of work and body postures, and laboratory detection limits. While there are many "tools" that can be used and each can have its purpose, I've found that SKC PPI (Parallel Particle Impactor) sampling devices can be a great addition to traditional cyclone sampling. This is due to the ability to use higher flow rates as well as sampler orientation considerations.
Regulated area signage: Some changes may be necessary in your facility that "may" not be easily understood or accepted by workers. Exposure potential may dictate that "Regulated Areas" be established. If so, corresponding signs must state:
Will your workers perceive that the company is trying to protect them, or instead wonder why they weren't told of this hazard beforehand? This sort of issue "begs" for a well-thought-out and implemented roll-out plan and communication strategy.
Coordinated efforts and culture: Are employees "used" to working in ways that will now be prohibited? Changing old habits will require more than management edict. Have engineering, maintenance, and operations workers been involved to think about and work through the consequences of required changes and to identify alternate methods? Where might vacuum systems be feasible and effective, and where must they be located? What methods will be used for emptying containers and changing filters while still protecting workers? Is there the potential to develop static electricity? How will the company change its practice of using brooms and compressed air, if new methods are physically more difficult and time consuming?
Exposure Control Plan (ECP): The ECP that companies must develop should be a coordinated plan and not simply list canned requirements. The standard details required content. Organizations should expect development of this plan to be more than trivial because it must describe tasks that involve exposure to RCS, as well as outline work practices, engineering controls, and other things that will take coordination among departments. You'll need to consider things such as:
- What requirements will your company apply to persons going "into" and "out of" regulated areas, such as for supervisors and forklift operators? What about short-duration entry? (You and I probably know the desired answer, but does your team see it the same way?)
- What is your company's protection philosophy and goal? Is it to (only) protect employees to the AL/PEL on an eight-hour time weighted average, or is it to consistently aim to reduce significant exposure potential wherever possible?
- Will changes to the respiratory protection program or practices be needed?
- Will there be changes necessary to existing local exhaust ventilation systems and associated maintenance and testing?
- Are local medical providers knowledgeable of the standard and "ready to go"?
Engineering controls and feasibility: OSHA requires that engineering controls be used to achieve necessary exposure reductions unless infeasible; organizations may not simply issue respirators and "be done with" their attempts to lower exposures. Investigate engineering control options in earnest. Controls that work in one industry may not work in another. Some companies may have implementation issues that are difficult to overcome or have situations where the costs incurred to reduce exposure levels result in diminishing returns. Organizations should carefully manage and document their improvement efforts and feasibility criteria (costs, availability of controls, improvements, acceptance, others).
Conclusion
The respirable crystalline silica standards have changed significantly. Time is of the essence for companies that have work that results in employee RCS exposures that trigger the standard. Preparation should include obtaining and reading applicable regulations, as well as OSHA Directives and other available information. Action plans should be time-based and address both regulatory requirements and organizational change issues. Some companies may have significant management decisions to make as they move toward improving regulatory compliance and reducing exposure. Good luck!
This article originally appeared in the July 2018 issue of Occupational Health & Safety.