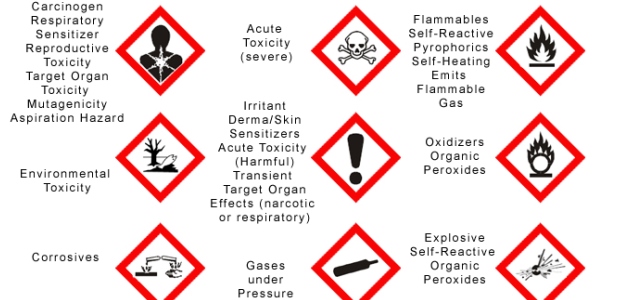
GHS HazCom Training is More Important Than Ever
An effective HazCom training program provides employees with a deeper understanding of the dangers and emergency situations they may face.
- By Melissa McCaffrey
- Jul 01, 2017
In the United States, the final GHS deadline is now long behind us. However, OSHA's alignment of the Hazard Communication Standard (HazCom) to GHS provided a wakeup call to millions of companies across the U.S. that they need to do a better job with their HazCom programs, especially when it comes to training. HazCom violations remain number two on OSHA's top 10 list of violations, with training failures being a big driver of citations.
In this article we'll look at four steps employers can take to ensure employees understand the chemical hazards present in their work environment and to comply with GHS updates to HazCom.
Step One: Build a Training Program Focused on Efficacy
While OSHA doesn't specify how to do training, it does state that the training must be effective. In short, employees must carry their learning into the workplace and be able to put it into use. HazCom training has two key components: one, providing employees with a basic understanding of the HazCom Standard; and two, training employees on the specific hazards of the chemicals to which they are exposed.
Regarding the first item, it’s no coincidence that OSHA's first GHS deadline focused on employee training because workers needed to understand the new SDS and label formats that accompanied GHS adoption. For some companies, meeting this GHS training deadline wasn't a major cause for concern. However, GHS alignment uncovered an unsettling truth: Many employers lacked a basic level understanding of HazCom, making it difficult for them to comprehend and address the changes brought on by GHS. As a result, these employers' workers either had never been adequately trained on HazCom in the first place or had been trained so long ago that what they had learned had been forgotten. Moving forward, it's critical that employers continue to emphasize basic HazCom training, which now includes GHS-aligned information to ensure employees are actually able to use that information in the course of their day-to-day activities.
The second component of an effective HazCom training program goes a step further by focusing more on the individual hazards employees face. Depending on the hazardous chemicals present in the facility, this training can either concentrate on a specific chemical and its hazards or a category of similar hazards for different chemicals; the key here is that it provides employees with a deeper understanding of the dangers and emergency situations they may face.
Keep in mind that employees must also continue to receive training on some pre-GHS HazCom elements if both older MSDS and newer SDS document formats still exist in the chemical inventory. Even though the final GHS changes have gone into effect, many facilities still have MSDSs in their libraries. Reasons for this include the following: a facility not yet having received a new product shipment since a manufacturer's updated SDS was created, a facility using a chemical from a manufacturer that has gone out of business, or a facility using a manufacturer that simply hasn't re-authored an MSDS to the new SDS format—due to their own internal delays or delays farther upstream from their source chemical suppliers. In general, the onus falls on the employer to know whether these pre-GHS formatted documents are still in circulation around its facility and to provide training on these formats for as long as they remain in use.
Step Two: Deliver Training So Employees Can Understand It
When OSHA first published its HazCom Standard in 1983, it championed the concept of the employee's "right-to-know" about the hazards to which they are exposed, which has greatly shaped the safety culture currently in place at many workplaces today. That said, a primary driver for OSHA's adoption of GHS was the desire to improve employee comprehension of critical chemical safety information.
With GHS, OSHA is saying it's not enough for workers to just know about the hazards in their work environment; instead, they also have the "right-to-understand" those hazards and to know what related safety precautions to take. Considering the overall changes brought by GHS alignment, this subtle word adjustment is easily overlooked, but it's a critical clue into OSHA's expectations for employee training.
The pre-GHS employee right-to-know concept often translated most literally into giving workers access to MSDSs and labels and making sure they were aware of the hazards that existed for the chemicals in their work environment. However, this approach didn't always translate to employees actually understanding the safety and health information being conveyed on the documents and labels.
GHS adoption helped solve this issue by bringing harmonization and consistency to the structure of safety data sheets and labels. Use of standardized hazard communication elements such as pictograms, which convey hazards via symbols, makes it possible for workers to more easily understand the hazards associated with the chemicals in their work environment. This simplified approach to communicating hazard information also makes it possible to better protect workers of all backgrounds. For instance, pictograms make it easier for illiterate and non-English speaking employees to understand the nature of a product's hazardous properties. GHS adoption helps ensure workers better understand the dangers being communicated to them.
Finally, the right-to-understand concept complements OSHA's rule on employee HazCom training—that it must be presented in a manner that all employees can comprehend and retain. When applied to HazCom training, this means that employees who interact with hazardous chemicals must receive training on those dangers in a language they can understand, even if the documents, SDSs, and labels themselves are only required in English.
Step Three: Provide Easy Access to SDSs
A key aspect of HazCom training is making sure employees know how to get direct access to SDSs and other hazardous chemical information. If an employer is using an electronic solution to provide employees with access to its inventory of SDSs, it's incumbent upon the employer to ensure employees are made aware of the system and how to use it to retrieve SDSs and that they care given access to the system with no barriers. Without that access, in the event of an emergency, even an employee who has received the most robust training on labels and SDSs will be at risk should a chemical incident occur that requires quick action.
For just that reason, many employers are taking advantage of technological advancements and using mobile solutions to put SDSs and other chemical information in the hands of every employee. The best EHS software solutions today leverage the cloud to make critical chemical safety information available anywhere, any time—and even offline via mobile apps.
Early adopters of mobile-enabled chemical management products and apps have found that they are great ways to extend the efficacy of training beyond the classroom, especially given all of the information available on an SDS for handling, storing, and dealing with chemicals during an emergency. Similarly, putting a good incident and hazard reporting mobile app in the pockets of workers provides safety managers with real-time information about work site risks that can lead to faster hazard abatement and better training around the actual dangers in the work environment.
Step Four: Keep It Consistent
While OSHA doesn't require employee training be performed in specific intervals of time, regular training—at least annually—is a best practice that will help ensure your employees better retain HazCom information. Other instances when training must occur include any time a new employee is hired, including temporary workers and visiting contract workers (to adequately understand the hazards associated with the chemicals with which he/she will interact) and when a new chemical has been introduced to the facility or when the employer becomes aware of newly identified hazards of an existing hazardous chemical. This helps ensure that employees who might come into contact with that substance understand its potential hazards.
Moving forward, it's important to view HazCom and GHS training as an ongoing obligation. Look into EHS software options for help managing, deploying, and tracking OSHA-required training. A good product eases the demands for administering numerous safety courses to individual employees or having to pause operations to host live trainings involving groups of employees. It makes it possible to deploy courses to whomever and at whatever frequency makes the most sense to your business. These solutions not only help you track your training needs and streamline communication to employees about completion deadlines, but also should provide a wide variety of on-demand safety training options that offer various courses, with many in multiple languages, to help you meet your unique compliance requirements.
No matter your approach to training, it's critical that you stay up to date. OSHA already has indicated its intent to review and most likely align with newer revisions of GHS as they are introduced by the United Nations. Most recently, OSHA expressed its intent to align with GHS Revision 7. As regulatory requirements continue to change, it remains the employer's responsibility to modify training programs to evolve with them. Companies should look at GHS as an opportunity to update and solidify their own training obligations and to ensure consistent HazCom information is being provided to them from manufacturers.
Companies following the four steps outlined above will be better positioned to address any changes to regulations, workplace conditions, or personnel. It's a relatively easy way for employers to mitigate risk and safeguard employees.
This article originally appeared in the July 2017 issue of Occupational Health & Safety.