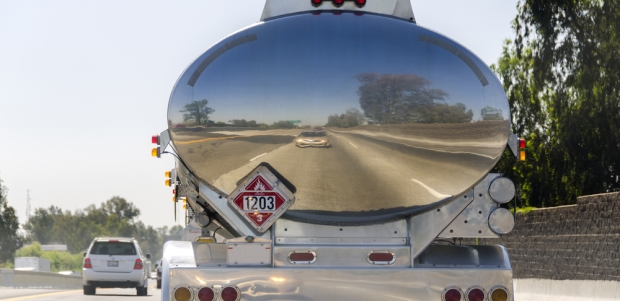
Key Requirements for Employees Transporting Hazmats
Like OSHA and EPA chemical safety trainings, DOT training helps hazmat employees to recognize and identify hazardous materials and learn how their functions ensure that those materials can be transported safely.
- By Karen D. Hamel
- Jun 01, 2017
Between OSHA and EPA's training requirements, employees who handle hazardous materials in their workplace should be very familiar with the hazards presented by any of the chemicals they work with daily. But when hazardous materials leave the facility in the form of a finished product, OSHA and EPA training is not enough.
The Pipeline and Hazardous Materials Safety Administration (PHMSA), which is part of the U.S. Department of Transportation (DOT), requires every person who is involved in the transportation of hazardous materials in commerce to receive specific training to understand how their actions affect transportation safety. Any facility that offers a hazardous material for transportation is a "hazmat employer" and must properly train its "hazmat employees."
Hazmat Employees
Hazmat employee training isn't just for commercial drivers or facility representatives who sign manifests. While DOT's definition of "hazmat employee" certainly does include those individuals, many more require hazmat employee training, including employees who:
- load, unload, or handle hazardous materials;
- test, recondition, repair, modify, mark, or otherwise represent containers or packages that qualify for transporting hazardous materials;
- prepare or offer hazardous materials for transportation;
- design, manufacture, or test packaging used to transport hazardous materials; or
- are otherwise responsible for the safety of transporting hazardous materials.
Unlike some regulations that exempt small employers, the training requirements for hazmat employees apply to every facility that is involved with the shipment of hazardous materials, even if they are self-employed. (49 CFR 171.8)
Like OSHA and EPA chemical safety trainings, DOT training helps hazmat employees to recognize and identify hazardous materials and learn how their functions ensure that those materials can be transported safely. Training includes several different aspects and must be completed within 90 days of employment or on the first day of a change in job function.
Employees must be tested at the completion of training and be able to demonstrate their knowledge. Until an employee can be trained, they must work under direct supervision of a person who has been trained.
General Awareness Training
All hazmat employees must receive general awareness training. This training is similar to OSHA's hazard communication training and in many cases can be combined with hazard communication training, as long as the required DOT elements are covered. General awareness training is designed to help employees recognize, identify, and classify hazardous materials. It also teaches employees the general requirements of DOT's hazardous materials regulations. This includes skills such as using the hazardous materials table, how to mark and label packages, and how to prepare shipping papers. (49 CFR 172.704)
Function-Specific Training
Because hazmat employees perform a diverse set of tasks before and during transportation, function-specific training is also required. This training provides targeted education on the specific function(s) that a hazmat employee will perform. For example, if a hazmat employee is filling packages, function-specific training may include how to close the package properly so that it will not leak or fail during shipment. Function-specific training for anyone signing manifests would include choosing a proper shipping name and other procedures specific to that task.
For some employees, function-specific training may include tasks required by International Maritime Dangerous Goods (IMDG) Codes, International Civil Aviation Organization (ICAO) Technical Instructions, or other procedures to fill the requirements specific to the mode of transportation or ultimate destination.
Safety Training
Like general awareness training, safety training that meets OSHA and EPA regulations may be used to satisfy the safety training requirements for a hazmat employee if the DOT requirements are also met. Training must specifically cover situations that a hazmat employee may encounter while handling a hazardous material.
Some of the topics that may be applicable are safe handling, bulk delivery, and closing containers when they are not in use. Hazmat employees also should be aware of emergency action plans, spill response procedures, fire prevention plans, and any other procedures that are in place to help prevent injury while preparing or transporting a hazardous material.
Security Awareness Training
Preparing hazardous materials for shipment and transporting them can present security risks. Hazardous materials can also present health, safety, and property risks when they are transported.
All hazmat employees must be aware of the security plan and be able to identify these types of risks before or during transportation. They also need to be trained to respond to possible security threats, which could include threats to a company or unexpected circumstances during transportation.
Hazmat employees who are responsible for implementing a security plan and those who perform regulated functions within the security plan must receive in-depth security training. The content will be specific to the facility and will address specific risk and threats that may be encountered.
Training must include a detailed understanding of the security plan, including objectives, organizational security structure, procedures, employee responsibilities, and actions to be taken in the event of a security breach.
Retraining and Recordkeeping
Every three years, hazmat employees must be retrained. The training should not be a brief refresher or solely an update; it must be compliant with current rules and include all of the same elements that were included in the original training. [49 CFR 172.704(c)(2)] Additionally, if a hazmat employee’s job duties change, he or she must receive function-specific training and any other required training prior to performing those new duties without supervision.
DOT takes this retraining very seriously. Like training for a new hazmat employee, recurrent trainings must include testing following the completion of the training. And employees who are not retrained within three years may not perform hazmat employee functions until they are retrained.
When DOT adds or revises rules that affect a hazmat employee's functions, they must receive retraining "prior to performance of a function affected by the new or revised rule." This training may not be delayed until the employee’s three-year training cycle is due.
Employers are responsible for keeping training records for each hazmat employee. Complete records include the employee's name, the date of the most recent training or retraining, a description or copy of the training materials used, and the name and address of the person providing the training. Each hazmat employee must have a document certifying that he or she has been trained and tested as required. Training records must be kept for the entire duration of the three-year training cycle and for 90 days after an employee leaves.
Just as OSHA and EPA regulations protect employees from the dangers of hazardous chemicals in the workplace, DOT's hazmat employee rules protect transporters and communities when hazardous materials are on the road, in the water, or in the sky. Identifying hazmat employees and providing them with the proper training helps to ensure that hazardous materials are kept safe at each step in the process.
This article originally appeared in the June 2017 issue of Occupational Health & Safety.