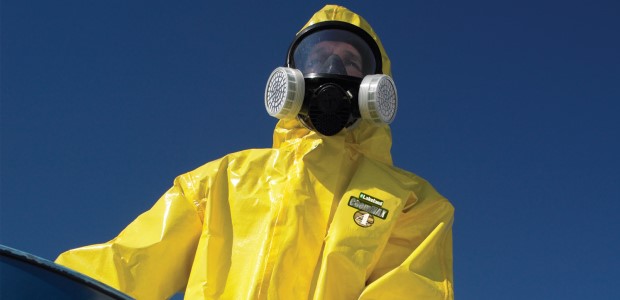
Page 3 of 3
Five Important Features of PPE for Chemical and Biological Hazard Protection
Do you work in an environment that poses significant risk for exposure to chemical and biological hazards? Industries that put workers in situations where they may be exposed to chemical splash, isocyanate paint, bloodborne pathogens, and more should first evaluate conditions of use when selecting appropriate chemical protective clothing.
Too often, decisions are made based on price and aesthetic considerations when selecting protective clothing. Making decisions based on these factors can put workers at increased risk. Another unsafe selection practice includes making purchase decisions based on the brand or fabric that has always been worn and not taking the time to understand important research and test results to determine whether the product is truly the best choice for the application.
While it is important to be cautious of data that is misunderstood or incorrectly applied, buyers should be aware that there are considerable data and chemical resources available in the marketplace. Here are a few garment features that are important to take into consideration when making an informed and appropriate chemical protective clothing purchase decision.
1. Permeation, Degradation, and Resistance to Liquid Penetration
Permeation is the process by which a chemical dissolves or moves through a protective garment. Degradation is the loss of or change in the fabric's chemical resistance or physical properties due to exposure to chemicals, use, or ambient conditions (e.g., sunlight). Penetration is the movement of chemicals through zippers, stitched seams, or imperfections in protective clothing material. All chemicals will eventually permeate protective clothing if the condition permits. Permeation resistance is related to the concentration and temperature of the challenge chemical, environmental temperature, and thickness of the barrier material.
An initial comparison of chemical protective fabrics can be conducted by reviewing published permeation data, but that data doesn't take into account all of the factors necessary when selecting a chemical protective garment. The permeation time quoted only indicates the amount of time at which the speed of the chemical coming through the fabric exceeds the permeation rate set by the test standard. The amount of time required for "initial breakthrough" as well as the amount of "cumulative permeate" are not discernible from published permeation test comparisons and should be taken into consideration when selecting the appropriate chemical protective garment for your task.
"Most people are unaware of the updates coming later this year to NFPA 1991, the Standard on Vapor-Protective Ensembles for Hazardous Materials Emergencies," says Charlie Roberson, SVP for International Sales with Lakeland Industries. "The updated standard will address the cumulative permeation levels of a chemical hazard that occur while the protective clothing is being used, as opposed to just a normalized breakthrough permeation rate."
Higher temperatures in your work environment can also result in faster breakthrough rates and, similarly, lower temperatures can lead to longer breakthrough times for certain chemical and material combinations. How well your PPE works against your known hazards for a work environment in North Dakota during February will likely be different for the same hazards and operation being conducted during August in Arizona. Chemicals also can change state across these types of temperature ranges, something that can’t be taken into account when conducting tests in the controlled environment of a laboratory.
2. Strength and Durability
Many protective garments are put to the test in regard to strength and durability in many job functions. They not only come in contact with hazardous materials, but also with abrasive surfaces, machinery, and rigorous movement by workers. The quality of a garment's manufacturing is just as critical as the quality of the material. Seam construction, tightness, and strength, as well as sizing and a manufacturer's quality guarantee, should be evaluated prior to making a garment selection.
3. Flexibility and Dexterity
Protective garments should be made from materials that are flexible enough for the wearer to move and work in the safest ways possible. A garment that is inflexible or causes dexterity issues may contribute to accidents such as slips, trips, and falls.
4. Breathability and Comfort
A good fit ensures the protective garment provides the wearer with both comfort and adequate protection. Ill-fitting fitting garments run a higher risk of tearing and restrict movement, which can affect the wearer's ability to carry out work safely and efficiently.
Similar to air permeability, there are many misconceptions related to garment breathability. How well a garment breathes is measured by its air permeability. Air permeability is measured by rate of airflow in cubic feet, per square foot of sample area per minute (CFM). Considering that a CFM of zero has no breathability, the differences in many chemical and biological material protective clothing's breathability measurements are typically so small that they are insignificant.
5. Protection Against Bloodborne Pathogens
If you, or the employees you are responsible for, are at risk for coming into contact with blood and biological agents, you need to feel confident that the protective clothing they are wearing can stand up to Bloodborne Pathogens (BBPs). These are the infectious microorganisms in blood that can cause disease in humans.
Unlike in the United States, performance tests in Europe are standardized and the results must be made public. Under EN 14126, the standard for protective clothing performance against infectious agents, we can objectively compare fabrics, allowing us to understand how these materials perform and compare to one another.
These are just a few of the factors to consider when selecting the best chemical protective clothing for chemical and biological hazard protection. It is critical for users to take these five considerations into account, in addition to the comparative performance data available. The selection of chemical-protective clothing should depend upon the type and physical state of the contaminants. Material testing outcomes should be evaluated and performance analyzed before selecting the best chemical protective garment for your unique work environment.
What challenges have you faced when selecting the best chemical protective clothing for your work environment, and how will you incorporate some of these additional factors such as temperature into your PPE selection process?
This article originally appeared in the December 2016 issue of Occupational Health & Safety.
About the Author
Kyle Kerbow is the Director, Product Management with Lakeland Industries.