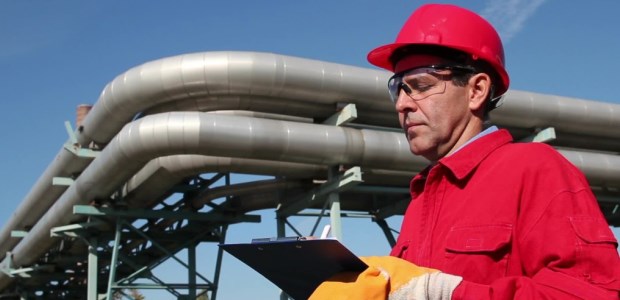
Transitioning From Old Traditions to a BBS Process
When so much emphasis is placed on a lagging indicator number, we begin to manage the number rather than what's driving it.
- By Scott Falkowitz
- Oct 01, 2014
For years, we built our safety programs on the processes and systems we all thought were most important. These were the processes and systems we were taught, mentored on, and what executives expected. They were learned through the safety training classes we attended and from peers from world-class organizations. What we essentially did was focus most, if not all, of our attention on a traditional-style management system based on safety meetings, training, measuring incident rates, applying disciplinary measures, and conducting site/facility inspections centered largely around conditions. These components are important and still have a place in today's safety management systems, but about 20-25 years ago, a new paradigm of safety management emerged.
Safety leaders were starting to realize that even though the traditional components of a safety program were important, not enough focus was being placed on the employees' behaviors. Injuries and losses were still occurring, discipline wasn't the sole answer, and the culture wasn't improving. A new approach was necessary, regardless of the industry: construction, manufacturing, engineering, or any other industry. It was time to place more emphasis on the people of the organization and investigate the concept of Behavior-Based Safety (BBS).
BBS at the Core
The broadly defined process of BBS is about management’s being supportive and caring for the employees. It’s about engaging with them in every aspect of the program, including concept, design, execution, and review. It takes a step back from threats of discipline, blame, and the promotion of fear and promotes coaching, feedback, and responsibility.
Successful implementations will yield an improvement in morale, a reduction in the severity and frequency of incidents, and an improvement in production, including reduced costs and better quality. (Komaki, J., Barwick, K. D., & Scott, L. R. 1978) This approach eliminates the perception of "us versus them" and bolsters a certain believability factor and trust that's established between the employer and the employee.
Traditional Safety Pitfalls and the BBS Solution
Let's uncover some of the pitfalls of the traditional occupational safety approach and identify things that can be done on the behavior-based safety side to improve our processes.
Safety meetings are an important part of any comprehensive safety program. Traditionally, everyone was brought together on a monthly basis for an hour, picked a topic, and discussed incident rates with some graphs that most of us couldn’t understand. How many times have you sat in a safety meeting and failed to make good use of the time by discussing a topic that had no value-added benefit? When this happens, the pitfall is that, though a meeting occurred, the meeting was not properly planned and likely lacked intent other than to document attendance. A BBS solution to this would ensure that safety meetings are focused specifically on the relevant tasks/risks at the time and that the employees are fully engaged in the conversation.
A discussion should be had with middle managers to determine the tasks that apply and, if necessary, shorter meetings should be held with the groups to which the tasks apply. In the meeting, avoid "preaching" from the podium. Instead, engage the audience in a two-way discussion to make the attendees feel appreciated, a part of the discussion, and that they are being heard and understood. The leader of the meeting should be a facilitator of great discussion. He or she should always follow through with suggestions and follow-up to close out open issues.
Traditionally, safety has been measured by OSHA recordability and the total recordable incident rate (TRIR). Many companies, even today, still base safety performance solely off of this and other lagging indicators. Some organizations measure the safety of their locations by using a process of reporting near misses. A successful near-miss process is often defined by achieving a certain amount of near misses per timeframe or hours worked. In reality, no real emphasis is placed on the quality of the near-miss reports or on corrective action follow-up.
The pitfall with focusing on lagging indicators is that when so much emphasis is placed on the number (e.g., whether or not we achieved an incident rate of 0.5 or collected three near misses for every 10,000 hours worked), we begin to manage the number rather than what's driving it. To transition from traditional and use a more BBS-based approach, organizations should measure safety performance based on leading indicators. The following are examples of value-added points of measurement:
1. What is the percentage of observations (observation strength) conducted on tasks that have resulted in past incidents or were problematic points of observation?
2. What percentage of your observation commentary (observation details/feedback/corrective actions) are properly documented?
3. What is your percentage of open issues that have been field verified as having been effectively resolved?
4. What percentage of tasks are field verified to have been pre-task planned (JSA, JHA)?
5. What is the percentage of employees who have been visited by a member of top management and had something safety-related, rather than production-related, discussed with them directly?
6. After review, what percentage of near misses are actually near misses and not reports of unsafe acts or conditions?
7. Of all the observations collected, what percentage are behaviors vs. conditions?
Each of the above examples opens the door for very important follow-up coaching on not only what to observe, but also observation quality, effective resolution, management interaction, and the building of the observation and feedback skill set.
Conducting Behavioral Observations
The word "inspection" has long been a staple of traditional safety programs. It's a process by which an employee goes out into the field with a checklist and focuses on conditions-based items that require some level of correction. Examples might include a damaged extension cord, substandard housekeeping, or a missing pair of safety glasses. Once the inspection has been completed, usually it is filed someplace with the hope that someone else might correct the issues that remain.
The pitfalls to this are many. They include unresolved issues, behaviors that are believed to be the primary cause of incidents having not been resolved--or even identified--and a large amount of paper with little to no value.
In a BBS system, the term "behavioral observation" is more prevalent than "inspection" because of its employee-centric nature. The first step is to develop a comprehensive strategy focusing on who conducts the observations, time of completion, observation frequency, and focus. The strategy is usually formed, in part, by focusing on where sustained losses have occurred in the past and where recent observations have shown that problems exist. A checklist can be developed that is either universal or task specific.
The second step is to train observers on how to conduct observations. Making sure that the observers introduce themselves to the observees, identify what they're observing, and why they're there are keys to an effective observation process. The goal is to observe the employee in their normal work environment, performing routine tasks without pressure, change of common tactic, or fear of reprisal or persecution.
The third step is to offer feedback after the observation has been completed. The feedback should include positive reinforcement for the things that were done safely and above average and corrective coaching for areas where the need for improvement was identified. It's very important to reassure the employee that this is a two-way discussion and it's meant to be a positive coaching process. If the goal is to build the employee's trust, the focus must be placed on coaching, not discipline.
The fourth step is to track and communicate the findings. The BBS process generates valuable data to aid in preventing future recurrence by focusing on resolution and prevention, but it needs to be communicated so that people become aware of the concerns. In a BBS process, names are of little to no importance and many processes are kept completely anonymous to help build trust and actually focus on the behavior rather than creating a punitive situation. As you collect more observations, you can focus on developing metrics to track and trend performance.
Conclusion
Implementing a BBS process within your organization is a substantial undertaking and is not something that can be done overnight. For some, it takes years. This article merely scratches the surface of the challenges you might currently be facing in implementing a BBS system.
Evaluate where your company stands in terms of what's being measured, the level of trust your employees have with management, what's being evaluated from an observation perspective, whether or not coaching and feedback is occurring, and whether there is ownership at all levels. Then sit down with your leadership team at the highest levels and have a candid discussion about your findings, as well as the benefits of this process, which include not only improving site safety, but also leadership styles. Propose BBS as an initiative but make sure it's laid out in a clear and concise plan with milestone goals and specific expectations.
A haphazard implementation of BBS will yield frustration, a lack of participation, and disengagement. Remember that this is an employee-centric process, so involving them and making them aware early on will be the catalyst, in concert with your leadership's support. As your behavioral process grows and the data improve, you'll identify better ways to support continuous improvement by focusing on clearer planning, more effective execution, and long-term sustainability. By transitioning from the old traditions to the new, you not only can get employees engaged through BBS, but also you can help to predict, prevent, and eliminate death on the job.
This article originally appeared in the October 2014 issue of Occupational Health & Safety.