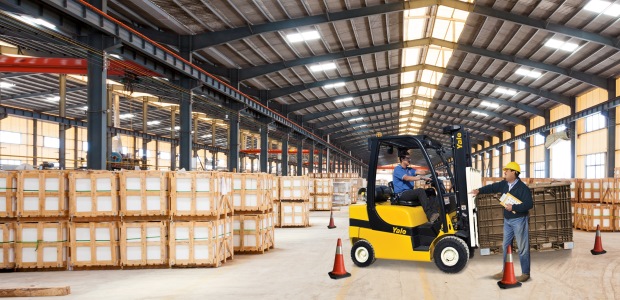
Taking a Second Look at Training
Use these tips to ensure you have an effective materials handling training program.
- By Jay Costello
- Sep 01, 2014
When it comes to materials handling, proper operator training is at the foundation of a safer and more productive operation. According to the National Safety Council, 70 percent of all industrial accidents are operator-induced. OSHA estimates that effective training may reduce the accident rate by 25 to 30 percent and that following training of lift truck operators, there is a 61 percent improvement in operator performance scores.
Key elements of a lift truck operator training program as required by OSHA encompass specific aspects of the lift truck, including warnings, capacity, stability, and controls, as well as workplace topics such as surface conditions, hazardous locations, and load analysis.
Even within the most established materials handling training program, there are areas that tend to be overlooked or topics that companies could revisit to ensure that their training programs are as effective as possible.
Emphasize Both Classroom and Hands-on Training
The "right" mix is highly subjective and really depends on the application, operator, and equipment being used. It should be site-specific, truck-specific, and application-specific. Each facet of training, from formal instructions (lecture, discussion, interactive learning, and reviewing video or written material) to practical training (demonstrations and exercises) and performance evaluation plays a major role in the overall success of the program.
Address Training at All Experience Levels
Like most certifications, the training requirement is a necessary step that must be taken every few years. Refresher training may also be required if an accident or near miss occurs, if employees are assigned new equipment, or if signs of unsafe practices are present.
It's important to connect the dots for veterans and new hires so they can understand the effect improved knowledge and better handling of the truck can have on overall operational efficiency. Aside from emphasizing safety, clearly communicating the contribution they can make is one of the most powerful ways of making training more important and valuable in the minds of all employees.
One approach that has worked well at Yale Materials Handling Corporation, in terms of making the best use of resources and enhancing engagement for both groups, is to have "veteran" operators assume the role of mentor. OSHA does not require that operator instructors be certified; they must have only the "knowledge, training and experience" to train powered industrial truck operators and evaluate their competence. Because every potential operator--including part-time, seasonal, and substitute workers--must be trained at least every three years, using veteran operators to assist with training is a great way of creating a stable group of instructors at the ready.
Customize Your Training
Beyond OHSA requirements, more and more states are considering adopting state-level regulations. Companies should be aware of what their states may require in the future, such as specifications on the type of training that needs to be completed, and integrate those elements into their training programs. Additionally, requirements for operating in Mexico and/or Canada are similar to federal U.S. standards, but companies with North American operations need to be aware of any differences between countries.
It is also important to include multilingual training to enable all operators have the necessary training to operate efficiently and safely. Yale recently released a Spanish version of its Yale Handle with Care program that contains all of the components necessary to conduct the classroom portion of an OSHA-compliant operator training program in Spanish.
Companies should obtain operating manuals from the OEM dealer for each piece of equipment at their facility. It is best to have these manuals located on the truck, and it is a good idea to have multiple copies of each operating manual accessible, in case a copy is lost or damaged.
Think About Attachments
Even if an operator is experienced using a particular truck, adding an attachment changes not only the functionality, but also the operating instructions. All attachments should be included in the operational manual, and these manuals should be revisited if a new attachment is added or if the lift truck is being used in a different manner.
Oftentimes, companies order a standard truck and then later add on an attachment. OEM dealers know that adding an attachment impacts capacity rating, and they will work with you to update the truck’s capacity plate—a critical step in ensuring the truck is used safely.
Cover Non-operator Safety in the Training
Following OSHA guidelines and driver training should provide greater safety for non-operators. Again, because 70 percent of accidents are operator-induced, the responsibility remains with the operator of the lift truck to be cognizant of intersections and other routes or traffic areas where pedestrians are likely to be present.
Pedestrian signs in the workplace should provide warning in areas where lift trucks may present a hazard. The use of warning systems—OSHA required or above and beyond—may, depending on the application, enhance the visibility of lift truck equipment throughout a facility.
Additionally, although they do not need to be certified, it is beneficial to have all people who work in an area where lift trucks are present view the portions of the training that address pedestrian safety. For example, the right and wrong ways to work around a forklift are woven into the Yale Handle with Care DVDs, which encourage safe work practices throughout the facility.
For operators working in public areas such as retail stores, an additional level of precaution is needed because many customers may be unaware of how to safely act around a forklift. To minimize customer interaction, be sure to block off both the aisles where the forklift is located and the adjacent aisles if there is potential for items to fall through to the other sides.
Include a Detailed Plan for Atypical Situations
If a truck component is found to be out of order, whether during pre-check or during a shift, operators should know the protocol for notifying others of the situation. Highly visible "do not operate" tags are recommended to hang on the truck to quickly indicate the truck is out of service. Additionally, if possible, the truck should be moved to a designated area and away from other machines so there is no confusion.
When a lift truck is temporarily unavailable, don't fill in the gaps with just any truck. This can put the operator and others at risk by using a piece of equipment that isn’t designed for that operation.
Operators also should understand which areas of the warehouse have higher potential for risk. For example, people tend to inspect the trucks but not the racks. Engineering departments should have a plan to evaluate these areas on a regular basis because they can pose an unforeseen hazard, and operators should have a way to verify that everything is in working order. Additionally, operators need to know the procedure for reporting unsafe conditions, such as a leaky pipe or broken light bulb.
Make Training Part of Your Company's Culture
Training in and of itself does not change behavior. It's the continual and consistent reinforcement of the training that ensures your employees are acting in a safe and responsible manner.
Tools that encourage uniform behaviors, such as checklists, should be completed by the operators prior to starting their shift—similar to the pre-flight checklists that are a part of a pilot's routine. For multi-shift operations, equipment should be reviewed and checked off by employees prior to starting their shift.
Properly trained lift truck operators can help reduce lift truck downtime and accidents, limit lost-time injuries, improve driver efficiency, and minimize product damage—evidence that a thorough and effective training program contributes to a company's productivity, health, and bottom line.
This article originally appeared in the September 2014 issue of Occupational Health & Safety.