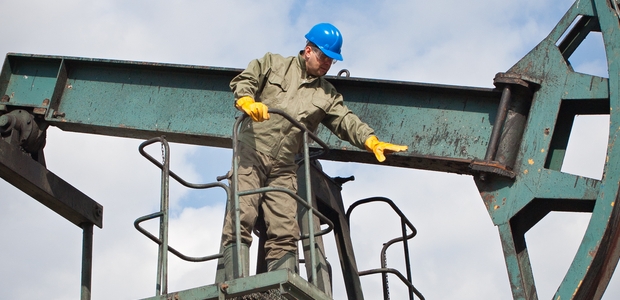
Covering All the Bases
Protective apparel is evolving to increase worker safety and satisfaction alike.
Not long ago, workers in the oil and gas, steel, and electrical industries had few, if any, preferred options with flame-resistant (FR) protective apparel. At the time, few companies understood or even recognized arc flashes, combustible dust, or flash fires as workplace hazards. Before protective apparel programs and education around safety practices, most workers exposed to these hazards just accepted their job was dangerous--liable to injury or even death.
Today, thanks to the actions of several organizations--including the National Fire Protection Association, OSHA, and ASTM International--workers exposed to flammable hazards can select from a variety of protective apparel to help reduce the likelihood and severity of injury during an accident. In fact, in recent years, many individuals have credited FR shirts, pants, and other garments with saving their lives.
As an ever-growing number of business leaders recognize the impact protective apparel has on employee safety and the bottom line, they are directing their risk prevention experts to implement protective apparel programs. Employees of these companies are finding that today's fire-resistant garments are a significant improvement in both protection and comfort. Many of today's cutting-edge fabrics have an improved look, feel, and breathability over the flammable garments the employees previously wore. To illustrate, below are three ways that protective apparel has evolved to provide organizations and employees with improved protection, comfort, and peace of mind.
Heat Stress Protection
OSHA estimates that 5 million to 10 million workers are exposed to heat-related illnesses each year. Any individual who works in an industry where time is spent in hot and/or humid conditions may be at risk for heat stress, a condition in which the body is unable to cool itself by any available method, most commonly evaporation (sweating). Many industries fall into this category, including oil and gas (both upstream and downstream), construction, manufacturing, power (generation, transmission, and distribution), mining, molten metals, and others. Although FR garments rarely cause actual heat stress, the type of fabric an individual wears can greatly improve the comfort of a wearer throughout the day.
Unlike the flame-resistant garments that first came to market--they were described as heavy, hot, and rigid--today's FR clothing is lightweight, soft, and breathable. Advancements in apparel technology have enabled textile manufacturers to create FR garments that wick moisture away from the body, allow for substantially more air flow, and transfer heat off the body. Designed to feel less like industrial work wear and more like the latest retail-inspired performance fabrics, today's flame-resistant options are an improvement in comfort over what the employee used to wear.
Enhanced Visibility FR
Today, FR apparel is evolving even further to include apparel that protects not only from fire, but also from low-visibility situations. Workers in almost every industry who wear FR garments are adapting enhanced and high-visibility options, especially where limited visibility creates a hazard. These low-visibility situations include working at night, in foul weather, in dusty conditions, and where moving vehicles and equipment are common. Garment options include ANSI 107-compliant FR reflective vests, neon fabrics, and a nearly limitless number of colors, sizes, and placement options for the reflective trim that can be applied to garments for either day or night protection.
Standards requiring flame-resistant apparel for work, such as NFPA 70E, the Standard for Electrical Safety in the Workplace, drove mostly indoor workers into FR clothing and do not address high or enhanced visibility options. However, OSHA's 2010 clarification memo forced the upstream segment of the oil and gas industry to match their downstream counterpart with a fire-resistant garment requirement. Operating day and night, in good weather and bad, it was important that the industry have enhanced and high-visibility FR garment options, which both FR fabric and garment manufactures delivered.
Unlike NFPA 70E and electric arc hazards, the industries that have a flash fire hazard use NFPA 2112, Standard on Flame-Resistant Garments for Protection of Industrial Personnel Against Flash Fire, and NFPA 2113, Standard on Selection, Care, Use, and Maintenance of Flame-Resistant Garments for Protection of Industrial Personnel Against Flash Fire, as their guide. NFPA 2113 requires that garments conform to ANSI 107 requirements. Under industry standards, organizations that utilize reflective striping for outdoor workers must ensure that the striping is also flame-resistant.
Industrial Laundering
When protective apparel first became available, it was mostly up to the employees to care for and launder their garments. Eventually, with the creation of industry standards, organizations realized they needed to wash FR clothing properly in order to maintain the FR integrity of the garments; this holds true today with treated fabrics and even with the advent of inherent FR fabrics. ASTM F2757-09, Standard Guide for Home Laundering Care and Maintenance of Flame, Thermal and Arc Resistant Clothing, outlines the proper laundering methods, including that FR garments should be turned inside out for laundering and should not be laundered with fabric softeners or chlorine bleach.
However, even if FR wearers diligently follow the steps above and wash FR garments according to the instructions in ASTM F2757-09, some contaminants simply cannot be removed through home laundering. Most FR wearers don't have at-home water temperatures high enough or detergents strong enough to remove the petroleum-based substances that can sometimes stay on and compromise FR clothing.
For this reason, the industrial laundering industry began offering updated processes that are unique and critical for FR garments. Featuring the proper water temperatures, water softness, and detergents, industrial laundering allows organizations to increase employee safety and compliance by providing a much greater likelihood of garment FR integrity. Under industrial laundering systems, weekly route services are used to collect garments and the clothing is inspected by hand, properly laundered, replaced if necessary, and returned. Garments deemed damaged or defective according to ASTM F2757-09 are either repaired with special FR threading or replaced.
An Eye Toward the Future
Although the protective apparel industry has come a long way in 20 years, the industry shows no signs of slowing down. Textile manufacturers, engineers, and safety professionals continue to invest time and resources in new technologies to make FR clothing safer and more comfortable for end users.
In addition, as protective apparel becomes more prevalent, it will become increasingly critical for organizations to look for products that have been properly tested and backed by a reputable manufacturer. Because it's important to ensure the FR integrity of the garment throughout its wearable life cycle, organizations should exercise caution while ordering online from unknown sources. The most reputable FR fabrics are typically certified to the requirements of NFPA 2112.
Ultimately, by taking the time to understand industry standards and best practices in protective apparel, safety, and risk prevention, professionals can significantly reduce the likelihood of injury among employees, as well as compliance costs.
This article originally appeared in the December 2013 issue of Occupational Health & Safety.