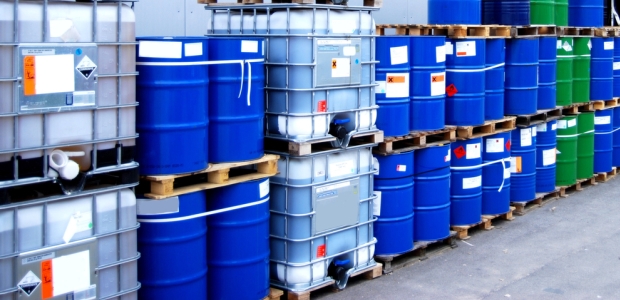
Newest HazCom Chemical Hazard: GHS Classification Shock
Employers should be prepared to address new hazards for chemicals, even for chemicals that have been used in the workplace for years.
- By Glenn D. Trout
- Oct 01, 2013
A key requirement of OSHA's newly revised Hazard Communication Standard (HazCom 2012) is that chemical manufacturers and distributors operating in the United States classify their chemicals using criteria adopted from the United Nations' Globally Harmonized System (GHS). For many manufacturers and distributors, the results of the classification (or reclassification, in the case of chemicals already in the marketplace) can be startling. At MSDSonline, our safety data sheet authors have coined a new term to describe the experience: "Classification Shock."
Classification shock is the realization that a chemical is more hazardous than once thought, either because of the new classifications OSHA has put in place or, in many cases, because the hazards were not evaluated properly the first time.
It's an issue employers should be aware of because they have a responsibility to ensure the requisite controls and personal protective equipment (PPEs) are in place and that employees are properly trained on all of the chemical hazards to which they are exposed. Employers should be prepared to address new hazards for chemicals, even for chemicals that have been used in the workplace for years. As we will see, the classification affects labels, SDSs, training, and more. To better understand the changes GHS brings to hazard identification and the compliance implications for everyone in the chemical life cycle, it's helpful to understand how hazard identification worked pre- versus post-GHS adoption.
Evaluation versus Classification
Under HazCom 1994, which is how OSHA refers to the HazCom Standard pre-GHS alignment, chemical manufacturers and distributors were required to evaluate chemical hazards and provide information about health and physical hazards to downstream users via material safety data sheets (MSDSs) and labels. OSHA provided basic guidance on what constituted a health or physical hazard and what information should be communicated via MSDSs and labels. However, much of what to communicate specifically about those hazards was left to the chemical manufacturer or distributor to determine.
For example, hazard evaluation under HazCom 1994 was a "yes" or "no" process. Either a chemical was hazardous or it was not; and if it was, it received a simple designation (e.g., flammable, carcinogenic, gas under pressure). Furthermore, labels were performance based, meaning OSHA put the onus on the labeler to determine what, and how much, information to include on the label. OSHA would then decide -- after the fact -- whether a label was compliant based on a subjective assessment of how effectively it communicated hazard information to users.
One problem with the old system is that wildly different hazard information filters down to the end users of the chemicals. For instance, an employee whose employer buys acetone from three different suppliers could see three different safety data sheets and three different labels for what is essentially the same product. Likewise, in the case of different chemicals with similar hazards, the information an employee sees often varies dramatically from label to label and MSDS to MSDS. Those days are coming to an end.
Under HazCom 2012, it's no longer enough for a chemical manufacturer or distributor to know that a chemical is hazardous; they also must know how hazardous it is. With GHS, chemicals are classified -- that is, put into broad classes based on the nature of their hazards and then, in most cases, divided into categories based upon the severity of their hazards. What's more, OSHA provides specific guidance on what constitutes a hazard and how a chemical should be classified. Once a chemical is categorized, OSHA provides detailed information and language that the chemical manufacturer or distributor is expected to use on the safety data sheet and label.
After the GHS alignment transition is complete, the end result should be that no matter the product and no matter the manufacturer, employees will see uniform hazard information on labels and safety data sheets for chemicals with similar hazards.
Along with new classifications, OSHA also has a new definition of hazardous chemical. Under HazCom 1994, a hazardous chemical was one that had a health or physical hazard as broadly outlined in the standard. Under the new GHS-aligned standard, what constitutes a health or physical hazard is very precise. Certainly, many of the new hazard classes are similar to the old ones, but there are some new hazard classes altogether, such as Germ Cell Mutagenicity, Corrosive to Metal, and Reproductive Toxicity. Additionally, three hazards that OSHA used to designate as health or physical hazards no longer can be defined as such because they are not covered under the United Nations’ version of GHS. As a result, to ensure employee protections were not diminished, OSHA changed its HazCom 1994 definition of hazardous chemical to specifically include these three hazards (combustible dust, pyrophoric gas, and simple asphyxiant) alongside the GHS-adopted physical and health hazards.
Same Chemical, New Hazards
All of this classification activity is leading chemical manufacturers and distributors to understand that many of their chemicals are more hazardous than they originally thought. Looking at how GHS was created, it probably shouldn't be that big of a shock.
GHS was developed by the United Nations with the help of many countries and is at its heart a collection of best practices drawing upon four major hazard communication systems: UN Transport Recommendations; U.S. requirements for workplace, consumers, and pesticides; European Union dangerous substance and preparations directives; and Canadian requirements for workplace, consumers, and pesticides.
By adopting GHS, OSHA has taken the best thinking and collective experience of all of those countries that contributed to its creation and has applied it to chemicals in the United States. So it stands to reason that better information leads to a more thorough understanding of a given chemical's hazards. At a minimum, the uniformity of hazard information required on labels and safety data sheets via GHS classification better prevents chemical manufacturers and distributors from obscuring, or otherwise mitigating, the hazards of their chemicals. A likely outcome is that many employers will discover, like the manufacturers and distributors, that some of the chemicals they've been using for years are more dangerous than they ever knew. Armed with this knowledge, employers will have the responsibility to ensure employees understand the new hazards and how to work safely with the chemicals based on the new information.
HazCom Compliance Going Forward
Chemical Manufacturers and Distributors: The deadline for chemical manufacturers and distributors to complete the reclassification process and update safety data sheets and labels is June 1, 2015. By that date, we can expect many more chemical manufacturers and distributors to be experiencing classification shock. Moreover, given the pace of things, companies with a lot of chemicals that wait too long to complete the classification/reclassification process and author/re-author their safety data sheets may be in for a different kind of shock.
Based on the number of safety data sheets that need authoring, the amount of time it takes to author a safety data sheet using the new classification, and the capacity of the marketplace to meet that demand, many companies could be heading for a logjam come the 2015 deadline that pushes them out of compliance. In short, the time to author is now.
Employers: New classifications, new safety data sheets, and new labels have serious compliance implications for employers. First, EH&S professionals should be prepared for the safety data sheet churn. They should expect their entire MSDS library to be updated in just a few short years. That could be a real headache for companies with hundreds or thousands of MSDSs. In preparation, many employers are turning to electronic MSDS management for help, as a good solution can alert employers to new versions of safety data sheets as they become available and flag those documents that have GHS formatting.
As new safety data sheets enter their facilities, employers will need to carefully compare them to older versions to see what has changed. A longstanding requirement for employers is that employees be trained on all of the chemical hazards to which they are exposed. If new hazards surface, that means additional training will be required for all affected employees. New safety data sheets also will have to be updated in the MSDS library.
Next, employers should keep an eye on chemical container labels. Employers have different compliance requirements for different label types (i.e., manufacturer labels on shipped containers versus workplace/secondary container labels). For instance, if an employer becomes aware of new hazards for a chemical already in the workplace, OSHA does not expect employers to update the manufacturer labels. However, OSHA does expect that employees will be made aware of those new hazards.
For workplace labels, OSHA does expect employers to update workplace or secondary container labels as new information becomes available. For instance, suppose an employer rebottles a certain chemical and places its own label on the new containers. If that employer subsequently receives a new safety data sheet that shows a new hazard has been identified for that chemical, the employer would be required to update all of the affected workplace/secondary container labels.
Shock Therapy
The best way for chemical manufacturers, distributors, and even employers to avoid classification shock is to get educated on GHS and HazCom 2012 and stay out in front of HazCom deadlines. The bottom line is that HazCom is a communication standard. The more information all parties have, the more consistent the information is across products and the better decisions everyone in the life cycle of hazardous chemicals will be able to make. Also, there is a lot of help available to those safety professionals who want it, including help classifying chemicals, authoring and managing safety data sheets, and training employees. This is not a road that employers or others must walk alone.
This article originally appeared in the October 2013 issue of Occupational Health & Safety.