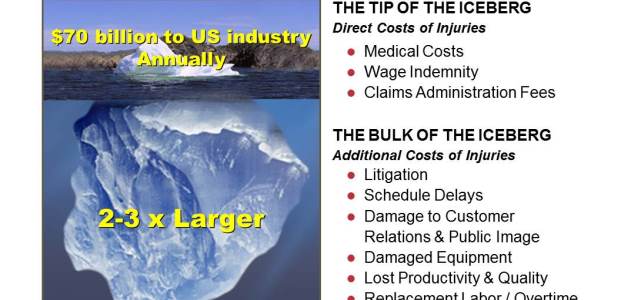
The ROI of Safety
Here's how developing a culture of safety can help the bottom line.
- By Simon Herriott
- Sep 01, 2013
Success in the oil and gas industry is usually quantified in terms of revenue, profit, stock value, and productivity gains, with much less attention paid to the influence of organizational culture on performance, growth, and business sustainability. But increasingly, businesses are re-examining the importance of organizational culture and its impact on performance. An organization's culture encompasses everything it does and everything it produces.
Safety Excellence for Business Excellence
A foundational component of our corporate culture at DuPont is the strong, pervasive safety culture that has taken root over the company's long history. It influences everything we do and every decision we make and has had a significant impact on our longevity and business success. At the heart of our safety culture is an ethical imperative that calls for all companies to do their utmost to keep their employees and partners safe. In a business as perilous as the oil and gas industry, nothing else, including profit margins and competitive advantage, trumps this value for human safety and well-being. But while this belief, thankfully, has an increasingly broad acceptance across industries and around the world, what is often overlooked is its influence on the organization beyond safety performance -- how it affects the bottom line. Based on our internal experience, as well as what we have seen in other organizations, good safety fosters good business in many ways.
Often discussions around the business benefits of safety focus on cost avoidance. Organizations know that every workplace safety incident incurs both direct costs (e.g., the cost of medical treatment) and indirect costs (e.g., loss of morale, damage to equipment, and loss of work time). For some organizations, the cost of these incidents, including the reputational damage they inflict, is motivation enough for improving safety performance. Whatever the reason, as performance improves and a strong safety culture takes root, organizations achieve broader business excellence in addition to safety excellence by creating principles and structures that can be applied to other areas of the organization.
The Road to Zero
In driving our own safety imperative and in helping other companies transform their safety performance, we have learned that ambiguity around the end goal corrodes the belief and commitment of management and employees alike. The goal should always be "zero" -- zero incidents, injuries, or illnesses.
While this target may seem like a difficult, if not impossible, achievement, we and other companies have seen that as performance improves and the intervals between safety incidents increase, celebrations of zero become more frequent and lend credibility and momentum to the drive to succeed. Focusing on zero incidents builds momentum in a way that lesser goals that allow for some injuries do not; lesser goals fail to strike an emotional chord with the workforce and get lost in the myriad of other metrics surrounding the modern organization.
Culture and Safety Performance
The DuPont Bradley Curve describes four stages of safety culture development as depicted above, with progressively more mature and higher performing cultures from left to right. Broadly, these cultural stages reflect a transition from a reactive approach to safety (and to incidents) to a more proactive, preventative approach. At an individual level, we see a transition from an extrinsically motivated approach to safety ("I follow the rules because I have to") to a more intrinsic motivation ("I follow the rules because I choose to"). Safety becomes a personal value and the practice of a safe workplace a source of organizational pride.
The second important step was to try to quantify and validate the relationship between culture and performance. Over several years, hundreds of clients and several hundred thousand employee responses, DuPont has collected perception survey results that help to assess the state of culture in the client organization. These surveys have been conducted in multiple industries and regions and at all levels of the workforce, from management to shop floor. From this data, DuPont has created an index of Relative Culture Strength (RCS) to measure the safety culture of an organization. Using the performance data from the organizations surveyed, we have been able to demonstrate a strong correlation with actual safety performance, supporting the premise that a strong safety culture is a prerequisite for sustained high performance.
Arriving at an Interdependent safety culture goes far beyond reducing the number of injuries in the field; it requires organizations to examine their safety model from three perspectives:
1. Leadership. What does management do to lead employees to safety excellence?
2. Structure. What are the organizational structures that enable the pursuit of safety excellence?
3. Processes and actions. What actions does the organization take on a regular basis to increase safety performance?
Felt Leadership
The greatest challenge to creating a safety culture is instilling felt leadership, which means that company leaders, including executive leadership, demonstrate they are incontrovertibly committed to safety. They do not waver, no matter the business conditions, and they are clear that whenever a decision involves a choice -- between safety and productivity, for example -- safety comes first.
The primary requirements of felt leadership are visible engagement and two-way dialogue. This demands, for example, that company leaders, including the highest-level executives, regularly interact with employees by performing safety observations, having conversations with employees about safety, leading safety meetings, and taking active roles in other safety-promoting activities. At DuPont, for example, the chief executive officer is also the chief safety officer and continually reaffirms, inside and outside the company, that safety is a core value and the goal is zero. The goal, per the DuPont Bradley Curve, is to foster a level of intrinsic motivation and operational discipline where people choose to follow the rules and where leaders enforce the rules fairly and consistently.
Elements required to support leadership include:
- Clear and meaningful policies and principles that confirm the priority of safety and provide a clear basis for decisions;
- Safety goals and objectives that are a prominent part of standard operating procedures; and,
- High performance standards that apply to all safety matters and are obvious and known to all employees.
Integrated Safety Structure
A strong safety culture engages all employees. This requires the company's safety organization to deploy people strategically throughout the organization. Traditionally, many companies have employed safety professionals or established entire departments to which safety was effectively outsourced. More "safety" than engaged participant and often out of touch with the real challenges of safe production, these safety professionals end up with an unenviable and unviable task. One of the earliest principles established by DuPont's founding fathers was that line managers should be responsible for the safety of the units they were operating. The supporting safety professional then becomes expert, mentor, and guide to the line organization.
An effective safety organization also produces data -- lots of it -- measuring both past performance and leading indicators (future). It develops strategies, is open to new ideas, and takes corrective and proactive actions. To do this, both line managers and safety professionals need to set up integrated managing structures to ensure the data are interpreted and used to drive change and that actions are agreed upon, assigned, and completed. The most effective organizations form committees or teams that are dynamic and productive groups working effectively to improve performance.
Processes and Actions
Even with strong leadership and an enabling structure in place, organizations must act to be effective. Organizations with a strong safety culture share certain action-oriented practices that include:
- Ongoing development programs that transfer knowledge and skills that help employees recognize unsafe situations, correct them, and work safely;
- Comprehensive audit programs with second- and third-party participants to proactively identify gaps in their processes to help ensure the safety culture remains strong and is embraced by the organization;
- Effective communication programs that keep safety top of mind throughout the organization; and,
- Both reactive and proactive processes to analyze and prevent safety incidents. For example, incident investigations help organizations learn from what has happened, while regular safety observations help prevent what might happen. In both cases, the key is to socialize the findings and show strong discipline in implementing recommendations.
Measuring the ROI
The return on investment that results from developing a strong safety culture includes returns that are relatively quantifiable (direct costs saved) and those that are less easily quantified (indirect costs avoided from loss of production, quality losses, equipment damage, etc.). The size of direct costs depends in part on the regulatory framework in which the organization operates, but indirect costs apply everywhere. Direct costs alone are often enough to justify investments in safety improvements. The iceberg illustration showing direct and indirect injury costs applies to all organizations, although proportions may change.
However, focusing exclusively on the benefits of avoiding incidents does a disservice to well-run safety organizations. Engaged leadership, the ability to diagnose issues and act preventatively to correct them, and the supportive and collaborative nature of an interdependent safety organization spill over into broader organizational effectiveness. Dividends include stronger operational discipline, greater productivity, an improved risk profile, and higher employee morale.
Momentum Is Key
Sustaining a safety culture transformation requires a plan that keeps safety alive and fresh across the organization, and it often takes time. Otherwise, the accomplishments may be temporary.
A successful safety plan should take into account employee turnover and leadership changes, maintain operating discipline, provide for continued audits, monitor data, report progress or slippage, and reinvigorate structures with carefully planned staff transitions. And finally, organizations should look for new challenges, such as off-the-job safety or community engagement, to keep the momentum going toward the goal of zero.
In the end, safety is about protecting people, their lives, and their livelihoods, but it is heartening to know that the better we get, the greater the rewards can be.
This article originally appeared in the September 2013 issue of Occupational Health & Safety.