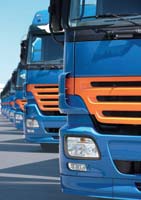
Technology Boosts Carriers' Performance
Using automatic on-board recording device data can improve organizational behaviors and drive key results.
- By Chuck Haffenden, Ken Yeomans
- Oct 03, 2007
WE live and work in a performance-driven culture. Everything is defined by how well it performs, from the companies we invest in and the vehicles we drive to the laptop computers, i-Pods, and cellphones we use to increase our personal productivity and individual performance. Interestingly, sometimes devices designed for a much humbler purpose turn out to be a bridge to other functional data that prove to be a significant boost to productivity, personal accountability, and major leaps forward in organizational performance. The story of the automatic on-board recording device (AOBRD) is one such story.
Several forward-thinking motor carriers have saved millions of dollars by using AOBRD data to develop information allowing them to target improvement goals with pinpoint accuracy. These motor carriers have made vast improvements in areas such as fuel economy, driver productivity, maintenance, vehicle optimization, and streamlining administrative processes. These improvements have brought about millions of dollars in savings. Let's examine how this came about.
The trucking industry has been operating in this performance-driven culture since de-regulation in the early 1980s, when the trucking companies that survived were those that could deliver products on time, safely, and at the most competitive cost while still producing a profit. These successful companies identified Key Performance Indicators (KPIs) that were closely tied to their operating costs and compliance opportunities to measure their progress toward achieving their KPI goals.
These KPI goals almost always include measurements in the following areas:
• Safety and compliance
• Labor costs
• Fuel costs
• Equipment utilization
• Equipment maintenance costs
In trucking, there are two variables that affect any motor carrier's ability to achieve its KPI goals: drivers and trucks. These variables have always presented two major challenges that each motor carrier has to decide either to address effectively or to ignore. These challenges are:
• Effectively holding drivers accountable for their individual performance and the achievement of their KPI goals
• Being able to accurately distinguish between driver and truck performance issues
Carriers that chose to ignore these challenges found themselves in the following scenario. As long as a driver could blame his/her individual performance on the truck and the motor carrier could not effectively dispute this challenge with real data, motor carrier managers realized a stalemate existed and no real progress could be made. Individual driver accountability could not be solidly established or enforced. Similarly, when drivers were faced with real truck performance issues and no data to back their claim, they felt extremely frustrated because they were not listened to, believed, or offered any real assistance in terms of an equipment change or repair.
For carriers that elected to tackle these challenges, however, there was an even greater challenge: How could the human element--the driver--meld with the mechanical element--the truck--into a single, effective delivery system that consistently operates optimally and at a profit?
It takes knowing the truth about driver and truck performance to resolve these conflicts. Motor carrier managers can effectively address both the performance of the driver and/or the truck when they have accurate data. Drivers can be motivated to modify their truck driving behaviors when they have confidence the data about their performance is accurate and when they can see the positive changes their behavior modifications bring about. Carrier managers can effectively and positively recognize drivers for behaviors consistent with organizational goals--not just results that could happen because of dumb luck. Mechanics can fix trucks when they possess accurate data about truck and subsystem performance. The old adage "what gets measured, gets done" most certainly applies here.
But how could motor carriers effectively measure all of these aspects of driver and truck performance, including the individual driver behaviors involved in driving a truck? Twenty years ago, gathering all this information and organizing it into a usable form would have taken an army of administrators and a huge IT budget. But in 1988, the U.S. Department of Transportation opened a window of opportunity in recognition of advances in technology by authorizing motor carriers to voluntarily use AOBRDs for the purpose of recording their drivers' records of duty status.
In the late 1980s, as AOBRD technology was beginning to take shape, the earliest adopters were those that found value in capturing record of duty status information and, to a smaller degree, automating fuel tax processes. During the economic downturn in the early 1990s, great pressure was put on delivery organizations to cut costs. Development activities by AOBRD vendors quickly shifted toward reporting on driver productivity and vehicle performance.
How Top Carriers Use AOBRD Data
In a March 2007 study done by the Aberdeen Group, best-in-class motor carriers were twice as likely to achieve fleet utilization rates better than their counterparts by using AOBRD technology. Companies using onboard technology reported vehicle utilization improvement of 13 percent, vehicle downtime reductions of 15.4 percent, and operating cost decreases of 10.4 percent, while operator compliance was up by 27.9 percent. This same study showed that regulatory compliance improved by 25.8 percent.
The question is, how did these carriers drive such significant results? AOBRDs capture driver log data and vehicle mileage information as a part of their design. It became apparent to users that these same data could be used for reporting which of their vehicles were being used and for what time period, which customers required the most time to deliver, and which drivers were the most efficient in completing their routes. In essence, these outgrowths started to become a competitive advantage to anyone that had employed this technology. What had started as a compliance tool soon became an integral management tool for controlling cost.
Forward-looking safety professionals began to embrace the operational efficiencies gained through utilization of the AOBRD. After all, these were the same devices that filled a regulatory compliance need. The challenge now was how to drive safe work habits with the same technology and exploit the real differentiating value of these products.
To understand how best-in-class carriers have achieved best-in-class performance, we must first understand how they have organized, formatted, and generated AOBRD data to form reports and set performance goals (KPIs) and then used that data to drive the improvements that make them best in class. Here are some examples of the type of data and reports that can be generated from AOBRDs.
AOBRDs tie together data collected from several sources, including:
• The AOBRD itself and driver inputs:
1) Internal calendar/clock
2) Driver identification
3) Crossing state lines
4) Route/load data
• Electronic Control Module (ECM) information
1) Speed
2) Mileage
3) Fuel consumed
4) Maintenance codes and alarms
5) Truck idle time
6) Rapid deceleration/final minute data
7) Hours/days the truck is not used
• Speedometer/Odometer
1) Speeds driven
2) Mileages
From these data, reports on the following information can easily be generated to target specific areas for improvement:
Targeted Result Area |
AOBRD Data |
Application |
Potential Outcomes |
Fuel Efficiency -- MPG |
• Idle time by driver
• Speeding by driver
• Over RPM shifting by driver |
• Individual accountability to MPG standards |
• Savings of 0.5 MPG fleet-wide are common
• Less engine usage • Environmentally friendlier |
Fleet Equipment Utilization |
• Days/hours used
• Days/hours not used
• Miles/day, week, or month
• Total idle time over any period of time |
• Local management accountability to standards
• Identify and redistribute or remove under-utilized fleet equipment |
• Lower fleet equipment costs
• Greater use of remaining assets |
Driver Utilization |
• Time worked • Miles & Stops accomplished
• Days absent or assigned tasks other than driving |
• Individual accountability to productivity standards |
• More productive driver force
• Lower delivery costs • Right-sized driver force |
Route Optimization |
• Miles to first stop • Miles between stops
• Total time/stop -- time to deliver to each customer • Reasons for delays en route and at stops
• Additional work performed |
• Identify non-revenue producing time and activities
• Identify accurate "cost to serve" customers • Evaluate routing efficiency |
• Reduce non-revenue producing time/ activities • Price products & services to ensure profits
• Redesign routes for more efficiency |
Driver Payroll |
• Time records -- time-in and time-out
• Miles driven
• Stops
• Other compensated time or activity |
• AOBRD data can link directly to existing payroll systems for pay purposes
• Overtime tracking |
• Eliminate multiple sources for driver time reporting -- regulations require retention of "supporting documents," but only if they exist
• Data justifying transition from hourly pay to activity-based pay |
Safety |
• Rapid deceleration
• Final minute reporting (before impact)
• Speeding
|
• Identify drivers with at-risk behaviors -- following too closely, speed too fast for conditions & speeding
• Accident investigation |
• Accident avoidance
• Improved driver retention/lower turnover • Improved safety record • Lower insurance premiums |
Hours of Service Compliance |
• Records of duty status
|
• Compliance with Federal Motor Carrier Safety Regulations
• Individual accountability to hours of service standards |
• Fewer drivers placed out-of-service • Improved compliance posture
• Improved safety record -- fewer fatigue-related accidents |
Fuel Tax Reporting |
• Miles driven by state
• With GPS-equipped AOBRD, routes operated in each state
• Amount of fuel put in vehicle at refueling
|
• System-generated fuel tax reporting for use by carrier staff or outsource vendor |
• Lower administration costs associated with fuel tax reporting from drivers to staff |
Equipment Maintenance |
• Maintenance codes and alarms • Miles driven since last PM
|
• Early warning to maintenance personnel |
• Improved PM scheduling • Fewer breakdowns |
Gains in Fuel and Driver Efficiency
Best-in-class motor carriers have achieved huge operational savings in fuel efficiency (MPG) simply by monitoring truck idle time caused by drivers and eliminating speeding in their fleets. At $2.81 per gallon, the average cost of diesel in the United States in June 2007, the annual fuel cost savings for just one truck and driver that operate 100,000 miles per year and managed to improve MPG performance from 6.5 MPG to 7.0 MPG (just 0.5 MPG) is $3,088.
Best-in-class motor carriers also use AOBRD data to identify assets such as trucks and drivers that are under-utilized--costing more than they either save or generate in revenue. Assuming a full-service lease cost for a tractor of $1,600 per month, eliminating one truck from a fleet would save $19,200 per year.
Savings in labor costs can be achieved by more efficient routing leading to work force reallocation or downsizing. Motor carriers that paid drivers by the hour find that using AOBRDs allows them to accurately identify how drivers spend their time; accordingly, they price compensable activities and transition to a much more cost-efficient activity-based pay program for drivers. Motor carriers that have employed this compensation strategy have experienced improvements in driver productivity, driver safety, driver retention, and individual driver pay while overall labor costs decrease.
Similarly, best-in-class carriers achieve large improvements in hours of service compliance and fleet safety using AOBRD data. Drivers can be motivated to change at-risk behaviors such as following other vehicles too closely or traveling too fast for conditions by pointing out rapid decelerations recorded by the AOBRD immediately after they occur and then recognizing drivers for improved performance when they eliminate these behaviors from their personal repertoire. Coupled with other motorist observations and management observations when riding with drivers, AOBRD data can be a powerful tool to bring about individual and organizational behavioral changes.
AOBRD data can help take the guesswork out of accident investigation. The AOBRD captures the speed of the vehicle and the activity since the last stop. However, in this case, AOBRD data can prove to be a double-edged sword. Carriers that employ AOBRDs in their fleets but fail to regularly monitor and manage speeding and rapid deceleration data may find that the data work against them if their drivers' behavior was not what was reported or what they expected.
Regulation 395.15 Being Updated
Best-in-class motor carriers realize further savings by reducing administrative costs associated with records of duty status and fuel taxes. AOBRD data can be stored (if backed up appropriately) in electronic form, virtually eliminating the need for paper file storage for driver records of duty status. Motor carriers using AOBRD often have a deliberate objective of capturing and using far more data than drivers' records of duty status. These carriers probably consider the electronic capturing of the record of duty status as an added benefit, not the real reason they purchased the AOBRDs in the first place.
Historically, the Federal Motor Carrier Safety Administration has taken a passive role by permitting use of AOBRDs to record drivers' records of duty status. This is outlined in current Federal Motor Carrier Safety Regulation (FMCSR) 395.15. This historical stance is set to change: FMCSA proposes replacing FMCSR 395.15 with a new regulation, FMCSR 395.16, which FMCSA has published in draft form for public review and comment. One of the key elements of this change is that use of Electronic On-Board Recorders (EOBRs)--an update to the term AOBRDs--could be required for some motor carriers.
Much of the success that individuals and companies enjoy in life comes not so much from knowing all the right answers, but from asking the right questions.
"Will AOBRDs be required in the future?"
"Who will be required to use them?"
While these questions are occupying a lot of attention in the trucking industry these days, there seems to be an entirely different group of motor carriers that have already asked an entirely different question:
"How can we get the data we need to drive improvements in specifically targeted areas to lower costs, improve safety and compliance, and build effective operating teams that are accountable for their results as individuals and teams?"
The answer for these carriers has been and continues for the foreseeable future to be automatic on-board recording devices.
What question should your company really be asking?
This article originally appeared in the October 2007 issue of Occupational Health & Safety.