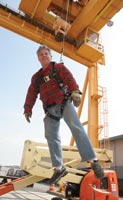
High-Level Hazards Averted
Naval Support Activity Mechanicsburg is a big believer in fall protection, having recently deployed a "first of its kind" overhead system for riggers' safety.
ACCORDING to recent information from OSHA and the Bureau of Labor Statistics, workplace fall-related deaths in the industrial and construction sector rank second only to occupationally related traffic accidents. When it comes to industrial fall protection systems, while challenges exist in designing systems that facilitate workflow, worker protection and safety must come first: Failure is not an option.
With that in mind, between March 2006 and April of 2007, safety program personnel at the Naval Support Activity Mechanicsburg in Mechanicsburg, Pa., culminated months of planning and design by successfully deploying a first-of-its-kind retrofit of one of the base's large-tonnage overhead cranes to help enable mission accomplishment and to protect crane riggers.
NSA Mechanicsburg encompasses more than 800 acres and features 35 commands that occupy close to 9 million square feet of combined administrative, industrial, and warehousing space. The base, which is the largest in central Pennsylvania, employs about 5,000 civilians, military, and contractor personnel. Approximately 8 million square feet is occupied by industrial and warehousing end uses. A wide range of fall protection systems are in use on the base, from flat-roof fall arrest systems to air handling units, cooling towers, sawdust collectors, and overhead crane ways. If put end to end, base-wide fall protection systems span more than 3 miles.
Each system provides compliant measures for protecting personnel, but some clearly are better than others. Some may or may not be feasible given the actual work to be preformed, the structure itself, or the frequency of the work.
Overhead bridge cranes, which are used at NSA Mechanicsburg to move very large ship parts, require a special type of fall protection solution. The base's crane population includes a 200-ton, a 25-ton, a dozen 10-ton, and one 5-ton units of different types. It is not always practical to protect overhead crane ways with a guardrail to protect personnel performing inspections or riggers, so a fixed fall arrest system on both sides running along the length of the building is a strong consideration.
NAVOSH Funds the New System
In the case of the base's 200-ton overhead crane, there was a clear need to find a better way to protect riggers from potentially serious fall hazards at heights up to 25 feet in various weather conditions as they loaded and unloaded massive components from railcars and trucks. As shown in Photo 1, the crane, manufactured by Ederer, LLC (Seattle, Wash.), stands 60 feet high and operates with a cab-controlled trolley. The trolley traverses about 35 feet with a motorized lift hook, which traverses about 20 feet perpendicular to the trolley. The crane is manned by 10 riggers.
Historically, riggers either used a 40-foot aerial work platform and a forklift with a secured safety pallet to elevate them upward, or they climbed up the component. However, they still had to climb out onto the component without any fall protection to attach their rigging to the crane hook, thus creating a serious fall hazard. This is the primary reason a fall arrest system was needed.
To help alleviate the problem, the base's Regional Safety Office submitted a Navy Occupational Safety and Health (NAVOSH) project early last year to secure the necessary funds to outfit the crane with a retractable fall arrest system. A NAVOSH project is a special Navy funding request vehicle to obtain funds to correct serious safety and health workplace conditions. This system had never used before on this or any other Navy base on an Ederer bridge crane.
In May 2006, NAVOSH approved the project and awarded the design, installation, and fabrication to General Dynamics of San Diego. General Dynamics worked closely with base safety personnel, riggers, operators, and the crane manufacturer to develop a solution. Ultimately, the team selected a self-retracting lifeline (SRL) system that was installed March 20-25, 2007.
The following briefly outlines the installation timeline and milestones:
Tuesday, March 20:
• Met with key personnel and reviewed the implementation sequence with NSA. Two 60-foot lifts dropped off at the site location.
Wednesday, March 21:
• Material arrived. Started welding the 8-inch-wide I-beams to the underside of the two large bridge flange rails (east and west sides).
Thursday, March 22:
• Completed welding installation of attachment plates. Raised and located the two trolley flanges at the attachment plate location with a 54-foot lift. Started welding the clips to the two flanges. Attached the clips with bolt/nut connection to the attachment plates.
Friday, March 23:
• Completed welding of the clips to the flanges. Installed the six trolleys and mounted the four trolley stops. Started welding of the top side gusset plates on the east side bridge flange rail.
Saturday, March 24:
• Completed the installation of the bridge cut-off switch in the bridge crane trolley cap. Completed welding the gusset plates. Primed and painted all weld locations.
Monday, March 25:
• Reviewed the implementation activities with key project team members and riggers. Installed two flange rails, six trolleys, and six SRLs with lanyards. Confirmed the operation of the cut-off switch of the bridge crane. Acceptance certificate issued to NSA Mechanicsburg stating that the new fall protection system meets all appropriate OSHA requirements.
• Total project cost: about $200,000
The system was engineered to safeguard riggers and give them free movement to connect and detach the crane hook from its loads. Primarily, the retrofit consisted of two 8-inch-wide I-beams equipped with trolley stops permanently mounted underneath the crane's bridge. A total of six trolleys were positioned on the I-beam track, three on each beam. However, the trolleys can be easily re-positioned on the same beam if needed.
A 6-foot lanyard equipped with a snap hook on each end is attached between the trolley and a 50-foot self-retractable lanyard that reaches to ground level. Additionally, the crane cab is equipped with an electrical disconnect to shut down power to the bridge as necessary, but still enabling the crane trolley and hoist to function. Furthermore, 10 full-body harnesses with individual storage bags were provided with a four-hour training/certification program. Each rigger has his own harness.
When riggers need to use the system, they will use the 40-foot lift to attach the trolleys and the SRLs to the beam, then attach taglines to pull the 50-foot SRL cable to the ground so they can connect to the system. Once they are attached they can hook up or remove their rigging and load or unload the component.
The system allows them the flexibility to move around, but they can't cross the SRL cable. If someone would fall, the system allows a free-fall distance between 3 and 6 inches. This allows the person to perform a self-rescue. The taglines will also be used to return the SRL cable to the SRL.
This is No Time for Shortcuts
Choosing the most appropriate, cost-effective, and safe method may involve some problem-solving processes and may require investing in equipment that is untested by or unfamiliar to the end user, as was the case here at NSA Mechanicsburg. Qualified or competent personnel must oversee all systems and most equipment. There are specific training requirements on use, care, handling, erecting, dismantling, and advising employees of hazards associated with this type of system or equipment. In addition, a fall protection plan developed and overseen by a competent person must be in place specific to the physical site.
Just because there were no safety mishaps on this crane to date, the consequences of a serious accident or fatality do not justify the attitude of "let's just get the job done." The total "turnkey" cost of the project, including training, was about $200,000, but the dollar value by no means is an accurate measure of the system's true worth. Proper fall protection is certainly a challenge and an economic consideration in the short term, but will pay off in the long run with increased productivity, increased morale, and less downtime.
This article originally appeared in the October 2007 issue of Occupational Health & Safety.