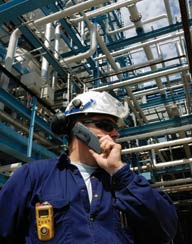
High-Stakes Helpers
Using wireless toxic gas monitors for confined space entry during plant turnarounds provides needed backup for fixed systems and human spotters.
- By Bob Durstenfeld
- Aug 02, 2007
WHEN power plants, oil refineries, and food processing, pharmaceutical, chemical, paint, and plastic plants need to have major service, that work is called a plant turnaround. These times without production are both high stress and high cost, in terms of labor as well as lost production revenue. The positive side can be substantial: increased equipment reliability and a lower risk that broken equipment will cause an unscheduled outage or catastrophic accident.
Many times, repairs need to be made in the "confined spaces" of pressure vessels, separators, feeders, storage tanks, and valve systems. These limited-access, limited-ventilation confined spaces present a challenge to worker safety and a challenge to retrofit time. A "confined space," as defined by OSHA, has limited or restricted means of entry or exit, is large enough for a person to enter and perform work, and is not designed for continuous occupancy.
Confined space entry is inherently dangerous. In the high-intensity environment of a plant turnaround, it becomes especially challenging to balance worker safety against the need for efficiency and the economic pressures of getting the plant back on line as quickly as possible. Employees who work in confined spaces can be seriously injured or killed by entrapment, engulfment, or the hazardous atmospheric conditions found in these spaces. The atmosphere in a confined space can become hazardous for a variety of reasons. Welding operations can produce toxic fumes, and decomposing organic material can release chemicals such as hydrogen sulfide or methane. Inert gases such as carbon dioxide or nitrogen can reduce the percentage of oxygen to fatal levels. Oxygen also can be consumed by chemical processes, such as the formation of rust or bacterial action in the fermentation process. And there may be residual chemicals from the production processes, including volatile organic compounds (VOCs) or hydrocarbons, which are both toxic and flammable and pose an explosion hazard, depending on the concentration.
Monitoring Confined Space Gases
All of this work falls under the guidelines of confined space entry found in OSHA's regulation in 29 CFR 1910.146. This regulation was originally written for sewer entry where the decomposition of biological material produced expected hazards including methane gas, carbon monoxide, and hydrogen sulfide while deleting oxygen. Those threats have traditionally been handled by a four-gas confined space entry monitor.
When working in the industrial environment, the hazardous threats change based on the processes and chemicals in use. The OSHA regulation was revised with the addition of subpart 146 Appendix E, Sewer System Entry, which states:
" . . . where the employer has not been able to identify the specific atmospheric hazards present or potentially present in the workspace, broad range sensors are preferable because they indicate that the hazardous threshold of a class (or classes) of contaminants (i.e., hydrocarbons) in the [work environment] have been exceeded."
In OSHA 1910 Subpart Z, more than 80 percent of vapors listed as "Toxic and Hazardous Substances" are VOCs or hydrocarbons. And most are toxic at concentrations well below their combustible levels; they also go unobserved by the standard four-gas monitor.
VOCs, depending on the concentration, call for the use of either a dedicated photoionization detector (PID) or a multi-gas monitor that includes a PID. In the past few years, five-gas monitors have been made available in both hand-held and wireless configurations.
As a turnaround work shift begins, each of the confined spaces to be entered needs to be monitored prior to entry. OSHA requires that confined space entry permits be reissued every 12 hours or when a new shift starts. This has traditionally been a manual process, and it takes several hours to revisit the work sites, resample the environment, and then reissue the permit. Hours of downtime during each shift of a plant turnaround can be expensive. After each work break, the confined space in question must again be monitored before work can resume.
In addition to the work crew, a "spotter" is assigned to each hole or work site. This person would be responsible for making sure the working atmosphere of the work site does not pose a safety threat. Typically, the spotter would be issued a hand-held monitor that might include a drop line of extended tubing for sampling the work area. If there is a problem, it is the spotter's job to clear the work site. Approval to return to work is usually left to a more senior individual, such as an operator. The spotter has to know how to interpret the alarm, and he or she has to get help if workers are endangered. The "hole watch" is required to be in visible contact with the workers.
The advent of wireless gas detection has given facility operators and safety officers a new approach to solve "hole watch" concerns. Site safety officers initially began deploying wireless monitors to back up the fixed-gas systems that were turned off during the service cycle. They soon realized they could also provide a backup to the spotter and even continuously monitor atmospheric conditions inside the vessel.
Using wireless gas detection networks with sensors at each confined space work site and a central command center, safety officers could continuously monitor a work site, even when workers were not present. Procedures were developed so that if no alarm had sounded during the break, then it could be assumed it was safe to re-enter the work site immediately. This cut the wait time after each break and provided a cost-effective way to safely increase productivity.
Wireless Monitor Deployment
One East Coast refinery using wireless technology has six independent wireless networks that are linked to local control rooms. Data from each of the six control rooms are uploaded to an off-site data server that integrates all of the site data. The master control room monitors all six production areas through the Web-based terminal viewer. The viewer provides visibility to all 36 deployed wireless monitors, as well as real-time maps showing the location and alarm data for all units.
This facility deployment currently includes:
1. a coker system with five monitors
2. a crude unit
3. a desulferizer
4. a cat cracker with 10 monitors
5. a hydrocracker
6. a sulfur plant with seven monitors
Alarm notification could be handled in this way:
1. Individual monitors provide local alarm notification at the work site.
2. The local control room is notified of an alarm over the wireless network and is displayed on the remote base station so a response can be initiated, if necessary.
3. Each local control room uploads the real-time data over hardwire Ethernet cable onto the secure off-site data server.
4. Data are monitored in real time on a secure Web terminal in the Master Control Room (or from any Web-linked computer).
5. As a backup, e-mail alerts are issued whenever any wireless monitor on the site goes into alarm.
One of the other advantages of the wireless gas monitoring system is that the data for all of work sites are immediately stored on a computer for both future reference and as part of the legal safety record for the site. This has given OSHA inspectors instant access to the exposure data for each work site.
Better for Safety, Better for Cost Reduction
The use of wireless toxic gas monitors has come of age. Today's monitors are quick to deploy or reconfigure and offer the ability to use global positioning satellite technology to know exactly where an alarm is coming from. Wireless gas monitors provide better worker safety and significant cost savings to industrial facilities that seek to continually improve their production and manage their costs.
References
1. NIOSH: Pocket Guide to Chemical Hazards, NIOSH Publications, Cincinnati, OH 1994
2. DHHS (NIOSH) Publication No. 79-142, 2002
3. "Worker Deaths in Confined Spaces--A Summary of NIOSH Surveillance and Investigative Findings," January 1994, DHHS (NIOSH) Publication No. 94-103
4. OSHA 1910 Subpart Z--Toxic and Hazardous Substances
5. "Guide to Occupational Exposure Values," 2002, compiled by ACGIH
6. NFPA 325, Guide to Fire Hazard Properties of Flammable Liquids, Gases, and Volatile Solids, 1994 Edition
7. RAE Systems: Correction Factors and Ionization Potentials (Technical Note TN-106)
8. RAE Systems: AP-211: PIDs for Continuous Monitoring of VOCs
This article originally appeared in the August 2007 issue of Occupational Health & Safety.