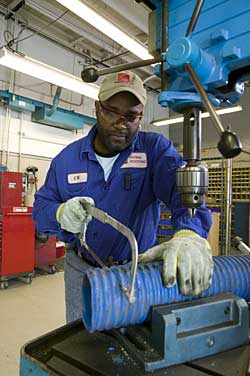
The First Cut is the Deepest
Tools that can help a safety manager choose the right level of cut resistance are much better today than they once were.
- By Daniel Ledwig, Kimberley Hosey, Alex Marks
- Mar 30, 2007
PICTURE, if you will, the new Safety Director at a sheet metal fabricator in
the early 1990s. Fresh out of college with a degree in Safety Engineering and a
desire to work in industry, he sincerely wants to "help" promote the idea of a
safe workplace. He wants to "make a difference."
On the first day of his new job, he is confronted with an accident that
results in a severe laceration of a worker's hand. A hospital trip is involved.
This one will definitely go down as a Lost Time Accident. There is grumbling
about a potential lawsuit.
It turns out that the injured worker didn't like the bulky cut-resistant
gloves he'd been provided and chose to go without them. They were Kevlar®
gloves, but they seemed too thick and slippery for the work. Many other
employees were dissatisfied with them, too.
Our new Safety Director had not even hung pictures on the wall of his office,
yet he already had a crisis on his hands.
Only a couple of decades earlier, his situation would have been worse,
however. To protect their hands from cuts, workers would have been given bulky
leather or leather and cotton gloves that would have been stiff, slippery, and
just plain difficult to work with from every perspective. And they could
still be cut rather easily.
'Hot' New Fibers Helped
In 1967, DuPont engineers patented
Kevlar®, and the company began producing the fiber in 1972. This aramid fiber
was conceived with many uses in mind: Body armor, rope, sails, and protective
fabric were envisioned and have since become reality.
For the safety professional, a new friend was born with the introduction of
Kevlar®. The ability to knit Kevlar® meant there would be many versions of the
material to suit a wide range of cut hazards.
Other cut-resistant fibers came along, as well. Other aramids such as Twaron®
(from Akzo Nobel) and Ultra High Molecular Weight Polyethylene (UHMWPE)
materials such as Spectra® (developed by Allied Signal and acquired by
Honeywell) and Dyneema® (from DSM Dyneema) entered the market. There are
advantages and disadvantages to each. For example, aramids such as Kevlar® tend
to be more heat resistant but less abrasion resistant, while Dyneema® has better
abrasion resistance while becoming weakened over time by heat. Dyneema® is
currently the "hot product" on the market because of its terrific protection
level while offering superb dexterity and feel. Its abrasion resistance gives it
a longer usable life, as well. "Miracle" fibers such as Kevlar® and Dyneema®
also could be combined with stainless steel and fiberglass to give even better
cut protection.
So by the time our new Safety Director began his career in the early '90s,
there were indeed many choices available to him to prevent cuts at his plant.
His predecessor had erred on the side of overprotection and purchased the
heaviest-weight loop-out terry cloth Kevlar® glove he could find. Sure, it was
bulky, but at least it gave a high degree of certainty against cuts--and the
last thing this director wanted was personal responsibility for choosing a glove
with too little protection. Of course, he failed to realize that a lack of
worker acceptance for such a glove would lead at least one worker to stop using
the provided gloves and get a severe injury as a result.
This scenario exemplifies what a Safety Director at the time faced when
confronted with the need for cut-resistant gloves that still offered dexterity,
grip, and worker acceptance. There simply weren't standards describing how much
protection was provided by cut-resistant gloves. A discussion of "good, fair,
and poor" was helpful but not quantifiable, and it typically left the Safety
Director feeling on his own when choosing gloves.
U.S. and European Standards
In 1994, help arrived. Out of Europe
came the first quantifiable standard, EN 388, which set standards on abrasion
resistance, tear resistance, puncture resistance, and, most importantly, cut
resistance. These standards were set using specific scientific methods. For cut
resistance, the numerical ratings of 1 through 5 are decided by the number of
cycles a rotating blade applied to the tested fabric needed to cut though the
material. More rotations needed means a higher numerical cut resistance rating
is given to the glove. The shield pictogram for "protective gloves for
mechanical risks" comes with the numerical ratings for abrasion, cut, tear, and
puncture resistance under it, in that order. This shield is included on gloves
sold in Europe and is clearly visible. Though not required in the United States,
some gloves are starting to carry the same EN 388 shield and ratings.
In 2000, the American National Standards Institute and the International
Safety Equipment Association created the ANSI/ISEA 105-2000 standard, giving
employers and Safety Directors another tool in choosing appropriate gloves from
the perspectives of cut resistance, but also abrasion, puncture, heat, cold,
chemical permeation, and flame resistance. For cut resistance, this standard
ranks gloves from 0 through 5. The test method used is different from the EN 388
method. For the ANSI/ISEA standard, the test determines how much weight is
required for a straight blade to cut through a material traveling 25 millimeters
(1 inch). As the weight required increases, the glove's rating increases.
Though different in testing methods, both EN 388 and ANSI/ISEA 105-2000 reach
similar conclusions that higher rating numbers represent higher cut resistance.
Because of these method differences, though, a glove will not always have the
same rating for both tests. It is important to remember to compare "apples to
apples" when considering cut resistance ratings and not compare an EN 388 rating
to an ANSI/ISEA 105-2000 rating.
There is some opinion that the European EN 388 standard will become the norm
for the United States, as well, owing mostly to its simplicity and head start as
the first mechanical hazard standard.
With the adoption of these standards becoming much more common, customers are
increasingly asking for gloves that meet a pre-chosen cut resistance level. It
is reasonable to expect these cut resistance ratings to become common reference
points, similar to the noise reduction ratings (NRR) referenced for hearing
protection devices. Generally, this is a good thing, but it might lead some
Safety Directors to rely only on the ratings and not consider equally a glove's
grip, dexterity, and worker acceptance. For a truly appropriate cut-resistant
glove choice, these points need consideration, as well.
Our Safety Director Hero muddled through his crisis and became an expert on
cut resistance on his own. If he were starting out today, he'd have much better
tools readily available to help him make his decisions.
This article appeared in the April 2007 issue of Occupational Health &
Safety.
This article originally appeared in the April 2007 issue of Occupational Health & Safety.