Five-Gas Comes of Age
Moving beyond the standard 4-gas confined space entry monitor makes for a very powerful instrument.
- By Werner R. Haag, Ph.D.
- Jul 01, 2006
MULTI-GAS detectors designed for use in confined space entry (CSE) are often not enough to protect against all chemical vapor hazards in the workplace. In their standard configuration, these meters have sensors for oxygen depletion, combustible gases (lower explosive limit or LEL), carbon monoxide (CO), and hydrogen sulfide (H2S). Such sensors cover the most common hazards--such as fires from natural gas, propane, or gasoline leaks, and asphyxiation in confined spaces due to lack of oxygen. Overexposure to carbon monoxide (CO) remains the most common cause of death by chemical poisoning in the United States.
Toxic Inorganic Compounds
However, many other toxic chemicals are used in industry to which a worker can be exposed without entering a confined space. Some of these toxic materials are inorganic compounds (containing at most one carbon atom), such as chlorine (Cl2), chlorine dioxide (ClO2), ammonia (NH3), nitric oxide (NO), nitrogen dioxide (NO2), sulfur dioxide (SO2), hydrogen cyanide (HCN), phosgene (COCl2), phosphine (PH3), arsine (AsH3), hydrochloric acid (HCl), and hydrofluoric acid (HF). The number of inorganic toxic vapors commonly encountered is perhaps a few dozen. Many of these can be measured using electrochemical (EC) sensors. Therefore, higher-level multi-gas meters are made that allow interchangeable sensors.
Typically, from one to four electrochemical sensors can be used in addition to or in place of the standard four CSE sensors. The main advantages of electrochemical sensors are that they are relatively inexpensive and are fairly selective for the compound of interest. That is, each sensor is designed to measure a specific compound by proper choice of catalyst, operation voltage, on-board filter, etc. Thus, a CO sensor shows no response to H2S, and vice versa.
The main disadvantages of EC sensors are that some of them have long response times of a few minutes, and they are not always as specific as desired. For example, the HCN and NH3 sensors take about 3-4 minutes to calibrate, and H2S gives a strong response on both of these sensors. In addition, some sensors can be overloaded, causing non-linear response or damage. For example, most NH3 sensors are burnt out in a short time by exposure to a few hundred ppm of ammonia.
Toxic Organic Gases and Vapors
While EC sensors cover many more chemicals than a standard 4-gas CSE meter can handle, there are even greater numbers of volatile organic compounds (VOCs) of concern. Organic compounds are ones with more than one carbon atom and typically also contain hydrogen, and possibly oxygen, nitrogen, sulfur, and others. Each year, more than 10,000 new organic chemicals are synthesized in the United States. Hundreds of these compounds are commonly encountered. More than 80 percent of the compounds listed in OSHA 1910 Subpart Z--Toxic ad Hazardous Substances are VOCs. They are the materials that drive industry:
- Fuels: propane, gasoline, diesel fuel, jet fuel, etc.
- Petrochemicals, plastics, and rubber precursors: vinyl chloride, butadiene, acrylates, isocyanates, etc.
- Paints and printing: toluene, methyl ethyl ketone, cyclohexane, mineral spirits, etc.
- Solvents and degreasers: perchloroethylene, methylene chloride, hexane, etc.
- Heat transfer fluids: Dowtherm®, Syltherm®, etc.
- Pesticides and fumigants: methyl bromide, acrolein
Most of these compounds are toxic to some extent and have exposure limits in the parts-per-million to parts-per-billion concentration range. Some are acutely toxic, but generally their effects are long-term, as opposed to the immediate hazards that the standard 4-gas CSE instruments protect against. Long-term effects include respiratory diseases and carcinogenicity, typically after years of exposure. A 4-gas CSE monitor keeps you safe to go home and enjoy your evening; a ppm-level organic vapor monitor allows you to enjoy your retirement.
Most VOCs are also flammable, so they present the dual threat of immediate explosion hazard when at high concentration and long-term toxicity at low ppm concentrations. Even the U.S. military, which regularly faces life-threatening situations, has recognized the need for detecting a broad range of VOCs and inorganic matierials because more and more battles are being fought in urban areas where chemical releases could result. Maj. Mark Lee of the U.S. Army Command & General Staff College wrote in 2001: "One of the capabilities we must develop for the future is the ability to protect the [U.S. Army] force for the effects of Toxic Industrial Materials . . . [and] oxygen deficient & flammable atmospheres."
PIDs & Other Broadband VOC Detectors
Unlike the inorganic toxics, there are almost no simple, EC-sized sensors available that are specific for individual VOCs. Therefore, broadband VOC sensors are used. Organic vapor monitors such as flame ionization detectors (FIDs), photo-ionization detectors (PIDs), and infrared (IR) sensors are such broad-range sensors. Figure 1 shows a detection pyramid illustrating how broadband detectors measure many more compounds non-selectively, while CSE units and EC sensors measure fewer compounds with more specificity. Combining these sensors into a single unit makes for a very powerful instrument.
Figure 1. Gas detection pyramid for portable monitors |
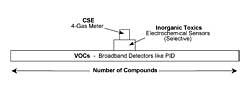
PIDs are the most common VOC detectors used because of their relatively low cost, simple operation, small size and weight, fast response, and good range of sensitivity. Most CSE instrument manufacturers now include a PID option in their multi-gas meters (see Figure 2). These units measure VOCs typically in the range of 0.1-2000 ppm and have response times of 10-20 seconds. Dedicated PIDs can measure down to low ppb levels and up to 10,000 ppm with response times as low as 3 seconds.
PID DesignFigure 3 shows how a PID works. A lamp shines low-wavelength UV light onto the sample gas. A small fraction of the VOC molecules are split into ions, and the resulting current is measured at the electrodes. Only VOCs with low enough ionization energy get ionized; common components of clean air do not interfere.
Because the response to various compounds can differ significantly, a good PID will have a library of built-in correction factors. These factors are automatically applied to display directly in ppm of the gas being measured. Thus, a single calibration gas, typically isobutylene, can be used while measuring the concentration of hundreds of different compounds accurately.
Select the Right Concentration Range
Figure 4 shows the approximate measuring ranges for common sensors. When selecting a portable gas monitor, it is critical to choose a sensor that not only detects the desired compounds, but does so in the proper range. For example, LEL sensors and PIDs can both detect benzene (a known carcinogen), but the LEL sensor cannot detect benzene at all near the OSHA time-weighted average (TWA) concentration of 1 ppm. Similarly, LEL sensors were formerly used to measure jet fuel explosion hazard, but recently ACGIH established a TWA of about 30 ppm, and a PID is now needed to detect these lower levels. In fact, poor response to jet fuels by catalytic bead LEL sensors, even at the 10 percent LEL level of 0.06 percent by volume (or 600 ppm), has led many military facilities to rely on the PID to measure explosion hazard instead of the LEL sensor.
Thermal conductivity (TC) sensors and oxygen sensors operate in the high range of a few percent to 100 volume percent. LEL sensors are most useful between a few hundred to about 100,000 ppm (0.02-10 percent volume). Gas detection tubes are available for more than 300 chemicals and a variety of ranges; they are low in cost and especially useful for corrosive vapors and mists, where direct-reading monitors have difficulty from corrosion, poisoning of sensors, or loss on filters. FIDs, standard PIDs, and IR and EC sensors typically operate in the middle concentration range of 0.1 ppm to above 10,000 ppm. Only ppb-level PIDs can measure down into the low parts-per-billion range. Also, multi-gas meters are not available with FIDs, but some do come with PIDs sensitive down to 10 ppb.
Figure 4. Approximate measuring ranges for common portable gas monitors |
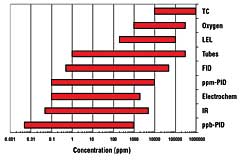
Wireless Data Transmission
While most instruments now automatically record continuous readings, peak, time-weighted average, and short-term exposure limits (STEL) for later download to a PC, units with wireless transmission have recently become available. Multiple monitors can communicate to a centrally located host computer that displays the readings and alarm status of each monitor up to 2 miles away. As shown in Figure 5, several instrument groups can be linked to one another in case of a large chemical release event. By linking the host computer to the Internet, it is possible for a user in Boston to check the status of monitors 2 miles away from a host computer in Los Angeles. Some systems allow tracking of the monitor location by GPS via satellite.
Figure 5. Multi-gas meter network with wireless data transmission |
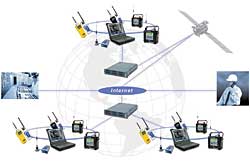
The ability to interoperate is especially useful for large-scale chemical releases to which several hazmat teams respond, each bringing its own wireless systems, while an incident commander can see the delineation of a plume from a remote location. Such systems have been rapidly deployed at major temporary events, such as All-Star baseball games, the Olympics, and presidential inaugurations.
Not all applications need be so sophisticated. For example, remote units have been installed permanently for perimeter monitor of chemical plants so that data can be observed at a central location without needing to drive to each site. In another instance, chlorine tanks were monitored for leaks without the need for an operator to put himself at risk (Figure 6). And at a refinery, the ability to monitor remotely the status of a multi-gas meter for confined space entry meant that certifications were no longer needed when a work shift changed, saving great costs.
Figure 6. Wireless, remote monitoring of chlorine tanks using a multi-gas meter with built-in modem |
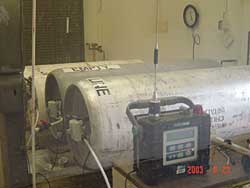
Summary
PIDs and a range of electrochemical sensors have become commonplace as extra sensors in conventional 4-gas confined space entry meters to protect workers from exposure to a broad array of toxic organic and inorganic vapors. New wireless transmission systems have opened up a host of safer and faster detection capabilities, requiring less operator involvement and thus saving costs.
This article appeared in the July 2006 issue of Occupational Health & Safety.
This article originally appeared in the July 2006 issue of Occupational Health & Safety.