Industrial Door Safety
Door automation should be a positive feature for any facility, but remember to consider safety in your application.
- By Jim Boerger, PE
- Dec 01, 2005
THE evolution of automated doors during the past 40 years has provided real benefits to industrial customers. The ongoing changeover from slow, rigid doors to high-speed doors has brought about tremendous strides in the areas of increased productivity and energy savings. However, this quest for high-speed, high-cycle automation also brings with it an added awareness of the risks that high operating speeds can bring to a door opening. High-speed door operation has the potential to imperil worker safety when proper safety measures aren't instituted.
Door safety is just one of many health and safety issues that must be addressed in the industrial workplace. The U.S. Department of Labor's Bureau of Labor Statistics in Washington, D.C., says 17,800 non-fatal workplace door accidents were reported in 2003. While BLS does not detail whether these accidents involved high-speed automated or manually operated doors, it is clear that high-speed industrial door accidents can be greatly reduced if proper safety design measures and training programs are employed.
Peter Kimener, president of McCormick Equipment, a dock and door manufacturer's representative in Cincinnati, recalls an industrial door with a hard leading edge that closed unexpectedly on a forklift driver at a food distribution plant. The high-speed roll up door struck the driver with the leading edge, resulting in many months of worker's compensation and a subsequent lawsuit.
Safety Considerations in Design, Operation
In their response to a demonstrated customer need for increased productivity and energy efficiency at the doorway, door manufacturers also need to keep door safety in mind. While product design always involves balancing the practical with the ideal and can never take place without consideration of purpose and value, it is useful for engineers to keep the following principles in mind: 1) If possible, design the hazard out of the product or minimize its effects. 2) If the hazard must remain in the product for it to operate, then work to guard against the hazard. 3) Augment the first two principles with warnings, as appropriate.
Potential door purchasers can use these principles, as well as Underwriters Laboratories' standard UL-325, as helpful references when looking for industrial door equipment that has been designed with appropriate safety features.
There are four common accidents associated with automated doors: 1) entrapment; 2) downward impact; 3) lateral impact; and 4) secondary impact.
Entrapment
While impact accidents are the most prevalent in the BLS report, 940 of the aforementioned accidents in 2003 involved entrapment.
Unlike residential rigid sectional doors, a majority of newer styles of industrial high-speed doors today are made of fabric. On interior models, which are typically pulled from top to bottom by weighted bottom edges, the doors can typically be pushed back upward fairly easily if they come to rest on someone, thus making it difficult to entrap an adult worker. Exterior industrial doors, however, are typically pulled down with belts or straps with more torque to offset wind loads. Entrapment is more of a possibility because an object is subjected to the continuing downward pulling force associated with these doors.
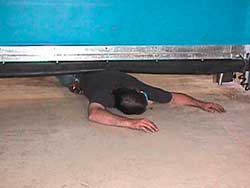
In the early days of residential garage door openers, entrapment problems involving children were resolved by reversing mechanisms. While it's an entirely different market than residential garage doors, industrial door designs typically also have resolved the entrapment issue by incorporating reversing mechanisms. A reversing mechanism is activated by either an electronic or pneumatic switch that senses an obstruction and reverses a closing door back to the open position. The electric switch is typically two pieces of metal foil that are brought together from the compression of foam on the leading edge. However, pneumatic switches sense increased pressure when a connected tube of air is compressed by an impact. A hole in the tube that allows enough pressurized air to escape can make the switch inoperable or undependable. Because doors get forklift impacts periodically in industrial applications, pneumatic switches and electric switches do require ongoing monitoring and repair.
Another disadvantage to either type of reversing mechanism is the coil cord that links the switch to the door electronics. Coil cords, which typically are exposed to traffic, are mounted at the halfway point of the door and stretch during full opening or closing. They inevitably lose their coil over time and are subjected to snagging. Consequently, they are prone to getting ripped off the door by passing forklifts. Many times, a dysfunctional coil cord isn't detected until the reversing edge mechanism fails during an accident.
In more recently modified door designs, manufacturers have addressed this problem by employing "fail-safe" monitoring with a four-wire electric switch, which will monitor for a damaged reversing edge switch and respond to a failure by holding the door open. Other possible devices include photo eyes mounted in the door opening, for example, to disrupt the door's operation if something lies in its field of view and safety switches that reverse the door when they sense the extra current used by the motor when encountering an obstruction.
While the reversing mechanism trend continues, other manufacturers have moved even further forward with safety by incorporating designs with lightweight, soft, and flexible leading edges. For soft leading edge doors, the flexibility of the edge itself helps prevent entrapment.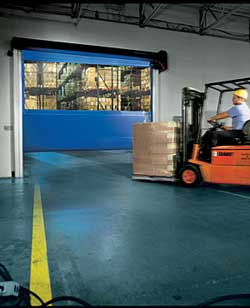
Warning signals such as audible alarms or flashing lights represent the third line of defense. As previously mentioned, designing the hazard out of the product or guarding against the hazard is the preferred strategy versus the use of warning signals. Some consider buzzers that are activated by a motion detection or other sensors and other warning devices that activate every time a door opens to be an unwarranted aggravation in the workplace.
Impacts
Of the four types of accidents, downward impacts are perhaps the most frequent type encountered in the industrial environment. Frequently, safety switches and equipment are used in door designs to address entrapment and impact situations. However, the next generation of industrial door safety appears to be the soft leading edge along with area detection sensors.
Soft leading edges employ the principle of designing to minimize the effects of the hazard. If safety switches, photo eyes, and warning signals break down or are ineffective in a particular situation, soft leading edges generally strike with lower forces than doors with hard bottom edges.
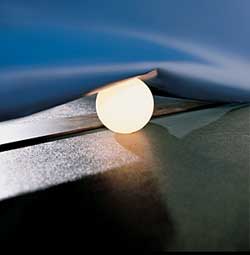
A door with a soft bottom edge is designed with enough weight to pull the curtain down, but the weight is incorporated into the door design in a manner allowing flexibility of the leading edge in order to help minimize the consequence of impact. The flexible weight is often wrapped in soft foam to further help mitigate the effects of the impact. For example, instead of experiencing the full weight of a door with a hard, rigid bottom edge during an impact, the soft leading edge flexes to distribute the load at impact.
Although such technology adds cost, and both its suitability and design may vary among applications, area detection sensors using infrared or microwave technology also can be used to monitor and guard the area in front of the doorway and to hold the door open while pedestrians are passing through.
Secondary impact is also a consideration in safety. A reversing edge mechanism that completely retracts a door back to its original position after an impact could possibly drag a worker with it or hit the worker again on the way up. Additionally, many doors open much faster than they close, so the upward impact is likely to carry more force. A door that stops on impact or employs a reversing mechanism that retracts upward only a few inches--just enough to take the load off--can help minimize these risks.
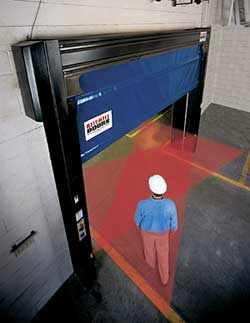
Another type of accident is lateral impact, where it is not the door's downward movement itself, but rather, a lateral collision with objects adjacent to a door that results in the impact. Forklifts can run into workers as well as other forklifts if visibility through to the other side of the door is poor. Vision panels or plastic windows manufactured into the automated door can help to eliminate many lateral impacts. However, vision panels require more maintenance and periodic replacement because they are prone to scratching over time, which limits their visibility.
Cold Storage Considerations
Cold storage applications typically use doors that close horizontally rather than vertically. From that sense, a worker may have better sight lines laterally and thus more advanced warning of a door closing.
The latest cold storage door design developments incorporate a flexible panel that greatly reduces the risk of entrapment and does not pose the same risk that rigid door styles pose. Photo eyes often don't work well in cold storage applications because they ice up if they're not outfitted with expensive heaters. Consequently, cold storage doors typically use leading edge sensing or motor current sensing to prevent entrapment or impact injuries.
Conclusion
Industrial manufacturers, warehouses, and distribution centers face increasingly intense competition from a rapidly changing global economy. Those facilities that strive more toward industrial door automation will undoubtedly increase their productivity and, more importantly, their energy efficiency, which will in turn make them more competitive. Therefore, door automation should be a positive feature for any facility, but only when safety is considered.
End users should request equipment that is subject to three door safety principles: 1) Use door designs that are effective at reducing the consequence of an impact. 2) Use doors that help guard against the risk of injury. 3) Consider the pros and cons of warning equipment in choosing what's best for the facility.
This article appeared in the December 2005 issue of Occupational Health & Safety.
This article originally appeared in the December 2005 issue of Occupational Health & Safety.