From Compliance to Excellence
Dig deeper and change the system if your results aren't satisfactory. One tool to achieve excellence is eLearning.
- By Ron A. Kirsch, Ph.D.
- Jun 01, 2005
AT the end of the day, the goal of occupational health and safety professionals is not only to keep all employees safe, healthy, and on the job, but also to send them home safe and sound to their families and loved ones. Getting to that goal has sparked numerous debates and philosophical discussions over the years.
This article compares and contrasts the components of basic compliance with the elements of safety excellence and the benefits of reaching beyond compliance. We will discuss the use of technology for delivering online training, measuring the effectiveness of training, and eLearning's role in driving safety excellence.
Basic Compliance
What is basic compliance? Quite frankly, it's the bare minimum standard. Basic compliance as it pertains to safety is covered by a number of regulatory bodies such as OSHA, MSHA, DOT, and EPA. Within these agencies are rules and regulations in the form of standards, directives, interpretations, enforcement guidelines, etc. In addition to the federal regulations, there may be requirements at the local and state level to consider.
However, even if you are meeting the basic requirements of the OSHA regulations, you may still be out of compliance. OSHA's catch-all regulation, the General Duty Clause, may be one of the most overlooked aspects of OSHA compliance, and yet it is the backbone of the OSHA standards. Section 5 (a)(1) of the OSH Act requires employers to furnish a workplace that is "free from recognized hazards that are causing or are likely to cause death or serious physical harm." Note that the language "likely to cause" implies a level of risk assessment that is already beyond mere compliance.
Even if there isn't a specific standard on a safety hazard, an OSHA inspector, by way of the General Duty Clause, can cite your company for non-compliance because of an observation or opinion concerning a hazard that is not covered under any other standard. Remember, OSHA is performance-oriented and results-driven. Your organization will be evaluated based on the results of your programs. Basic compliance is just the first step toward safety excellence.
Beyond Compliance
Now, let's compare the components of both.
Basic compliance begins with a safety culture driven from the safety department. In safety excellence, the safety culture is driven from top management down. You have management commitment, leadership, and direction. As you start to weave safety as a value into the fabric of your organization, you create a culture that expects zero accidents. Employees are involved in the process, and continual improvement is in place.
Basic compliance includes written programs and job safety analysis (JSAs). In an environment of safety excellence, written programs are active, living documents. JSAs are coupled with proactive risk assessments.
In basic compliance, forms and processes are in place, accidents are investigated, inspections and audits are performed, and OSHA logs are kept. In safety excellence, retrospective and root cause analysis is used. This starts with your OSHA log information, including the number of recordables and reportables, injuries, illnesses, frequency, and severity. These are key indicators of your program's performance. However, looking at your OSHA logs and claims history is like looking in a rear-view mirror. In safety excellence, you look for leading indicators and opportunities for early intervention, as well as determining root cause and investigating incidences and near misses. You have appropriate performance metrics in place and use them to determine your opportunities for continual improvement.
Ask yourself--is your system/program working? Systems are designed to produce exactly what they're producing. If you are not getting the desired results, dig deeper and change the system. Examine your workplace environment, worker capabilities, and their motivation to perform. Examine how these elements are integrated and working together and where they are not.
Basic compliance programs have reactive safety management. Have you ever felt like a firefighter or the safety cop trying to enforce your safety department's standards? You end up doing triage and caring for your injured workers rather than preventing injuries. Safety excellence is proactive safety management. You track near misses and use the event as a learning opportunity. Once you have a solid foundation in place, you can work on behavior based initiatives and programs and utilize peer-to-peer observations and interventions. You may wish to consider an incentive-based program that encourages both reporting and the culture of zero accidents.
Basic compliance programs have adequate tools and PPE in place. In safety excellence, you are constantly re-analyzing your systems and processes; engineering controls are sought first.
Basic compliance establishes the required training schedule, and basic training materials are in place. In safety excellence, training is part of the corporate culture. Training materials are customized and kept fresh to keep employees engaged. Your compliance-driven training is running smoothly while your resources are focused on addressing risk management concerns and proactive/just-in-time training events.
Training & Technology
Now, let's zero in on the importance of training. In many ways, training reflects your corporate safety culture, creates awareness, and builds knowledge of your programs. It is a core component of any safety excellence program. However, training workers in a system that is broken will only produce better-trained injured workers. And if your employees are not engaged in training, they are not going to learn.
Effective training programs can help to change employee behavior and drive accountability outward in your organization. The use of technology in the form of eLearning can play an important role in managing your overall program.
In an independent study on trends in safety training conducted in December 2004 by Management 21, a Nashville-based market research and consulting firm, 32 percent of 410 safety and risk management professionals responded that they use some form of eLearning. Five years ago, that number was probably less than 5 percent. Five years from now, that number probably will be above 80 percent.
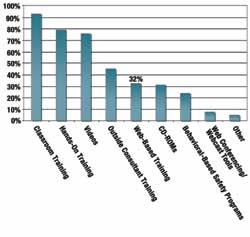
When asked what percentage of their program is currently delivered via the Internet and how that will change in the next 12 months, the responses showed a marked increase in the use of eLearning.
As you can see, the trend is moving toward greater utilization of eLearning to deliver training programs. Safety professionals recognize that in this age of technology, eLearning is a critical part of a safety program and required to be competitive.

Understanding eLearning
When examining eLearning's role in safety excellence, it is important to understand what it is and what it isn't.
What it is:
- A comprehensive way to manage your safety program, both online and instructor-led. Technology in the form of eLearning allows you to assign, deliver, track, record, and report on your training program in an automated fashion in real time, 24/7.
- An efficiency tool that increases flexibility and improves productivity.
- An ideal solution for orientation, refresher, or just-in-time training.
- An easy way to deliver a consistent message.
- A way to appeal to multiple adult learning styles and multiple language requirements.
- A way to raise awareness and improve knowledge retention.
What it isn't:
- Your job replacement! To the contrary, eLearning is a tool designed to make you more efficient and effective as a safety and risk management professional. You will find that eLearning will provide you with more time to spend on other proactive safety and risk management functions and interaction with your employees.
- Rocket science. It is quicker and easier to implement than you might think. All you need is an Internet-connected computer and basic computer skills.
- The answer to every training need. Some training requires hands-on, instructor-led activities. Operating a powered industrial truck or fit testing a respirator are just two examples. While eLearning won't train your employees to drive a forklift, it can allow you to raise awareness, transfer knowledge, and learn from scenario-based events.
Measuring the Effectiveness of Training
Let's face it: What gets measured gets done. There are several ways that you can measure the effectiveness of training. You can do assessments or tests. You must also inspect what you expect with routine observations, inspections, and audits. Employees should be able to demonstrate skills learned and safely and competently perform their assigned job functions. You can also do a pre-test, a post-test, and a gap analysis to measure the baseline knowledge and the knowledge gained.
Some of the regulatory agencies have training time requirements for initial and refresher training. For example, DOT requires two hours of reasonable suspicion training on drugs and alcohol for those who supervise commercial drivers. However, measuring the effectiveness of your training based on attendance or how much time you spend in training is like grading students performance based on how much time they spend on campus. The seat-time requirements from the regulatory agencies are antiquated and need to be changed sooner, rather than later.
Measuring the effectiveness of training is a process, not an event. The number of incidents, frequency, and severity are the true measure of your overall program and a key indicator of the effectiveness of your training.
The bottom line is that occupational health and safety excellence improves organizational performance. When used appropriately, eLearning and other technologies can be a great facilitator of occupational health and safety excellence and can truly assist organizations to reach beyond compliance.
This article appears in the June 2005 issue of Occupational Health & Safety.
This article originally appeared in the June 2005 issue of Occupational Health & Safety.