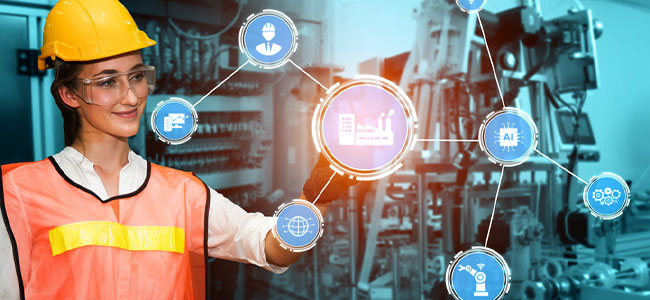
Embracing Change: How Connected Gas Detection is Reshaping Safety — and Organizations
Beyond safety technology, the rise of connected gas detection underscores a deep need for organizational change and human adaptation. How does change management help integrate connected gas detection into company safety cultures?
- By David Kopf
- Oct 11, 2023
In today’s worker safety world, technological evolution is constant, but it’s not just about the tools — it’s about the organizational transformation they usher in.
As connected gas detection systems elevate safety standards, a parallel narrative emerges: the intricate dance of change management. This journey from basic alarms to sophisticated networks isn’t solely a story of advanced hardware. It’s creating a roadmap for how companies are navigating, adapting, and embracing change, ensuring not just the safety of their workforce, but also cultivating a culture that understands, values, and integrates these technological leaps.
The Importance of Connected Gas Detection
Connected safety technology, particularly in the realms of lone worker safety and gas detection, has seen significant advancement. It has moved from personal monitors to a sophisticated cloud-connected network of devices. This network offers advanced data analysis and enhanced reporting capabilities.
Today’s safety measures have vastly improved from the past, where alerts remained local to the worker. In earlier times, when an employee faced a gas hazard, the device might have alerted the user, but if the user couldn’t act, no one else would know. Tragically, this often led to late interventions and devastating outcomes.
Now, with the evolution in technology, an immediate alert system ensures that when a high gas concentration is detected or when a worker signals distress, immediate assistance is dispatched. These systems work 24/7, providing a lifeline to workers in distress, ensuring their safety, and reducing the potential for tragic incidents.
“I think corporations are realizing the importance of connected technology and investing in the implementation because it provides visibility to improve the safety of the employees both proactively and reactively,” says Ealat Chaachouh, Manager of Client Implementation in North America for Blackline Safety, which offers connected gas detection solutions. “We can provide reporting and visibility on the safety of the employee to drive safety culture change, and also improve workflow safety process, as well as the automation and compliance within corporations.”
Connected gas detection technology isn’t limited to just one kind of industry or a specific company size. Chaachouh notes her company’s technology has been implemented in more than 15 industries, including oil and gas, biotech, pharma, utilities, transportation and logistics.
The size of the companies using connected gas detection ranges as much as the type, Chaachouh notes. “The clients that we serve range from five to 10 employees to thousands of employees; local companies in small towns or cities, up to global corporations that are adopting our safety solution,” she says. “So it’s a very wide range.”
Change Management in Connected Gas Detection
At its core, change management is not just a sequence of actions or a checklist. As Chaachouh explains, it’s a holistic process involving everyone in an organization, from the frontline user of a gas detection device to the executive leadership. More than just “doing things differently,” it’s about fostering understanding and buy-in at every level.”
This comprehensive approach addresses the human side of technology transitions. While change is a constant, it often generates discomfort. Chaachouh acknowledges the human resistance to change, stating, “The one thing that we can guarantee is that things constantly change, but I also understand the human side of it; that it is uncomfortable for people to change,” she says.
Navigating those changes, especially when introducing novel technologies, requires meticulous planning, communication, and training. Some examples of the steps involved:
- Communicating in advance what changes are coming.
- Explaining why this change is required and the benefits of it.
- Understanding the nature and quality of training that’s required and ensuring that end users have all the training they need.
- Creating frequently asked questions, and documentation.
Those approaches help ensure there’s that full understanding and adoption, but the key in that process is conveying the “why” behind a change. Chaachouh references Simon Sinek’s book titled “Start With Why: How Great Leaders Inspire Everyone to Take Action.” In this book, Sinek introduces the idea that hinges on communicating “why” they do what they do, rather than just “what” they do or “how” they do it. Starting with the “why” resonates more with people and is a more effective way to inspire and lead.
“Understanding ‘why’ a change is happening can mitigate resistance,” she emphasizes. “It’s not just about knowing what is changing, but grasping the purpose behind it.”
Moreover, to support these shifts, especially when integrating new technologies like connected gas detection, a critical tool comes into play: change management. Change management ensures a smooth transition, aiding organizations in anticipating potential roadblocks, addressing them proactively, and ultimately ensuring successful implementation.
An Evolving Business and Safety Discipline
“Change management is now a formalized process,” Chaachouh notes. “But I do believe un unformalized change management concepts must have existed for hundreds and really thousands of years prior because of advancements in civilizations, agriculture and so on.”
Truly, humans have always grappled with change. Think of it as an informal dance with change, one that has spanned potentially thousands of years. However, the end of the 20th century marked a turning point.
“In the 1990s, change management concepts were being adopted into businesses around the world,” Chaachouh points out. “Change management became formalized in the early 2000s. Technology had a huge impact on that because we’re changing at such a faster and more rapid rate than we ever have in the past.”
The rapid development and adoption of technologies have turned change management into a formal discipline. The aforementioned dance with change was no longer just an informal waltz. It became choreographed and systematized. Companies worldwide began to not just recognize the need for structured change management but also to integrate its principles deeply within their organizational fabric.
Chaachouh refers to the works of a cultural anthropologist named Van Gup, who delved into understanding human interaction with change before the 90s. Gup’s research underscored the journey humans take through three pivotal states when encountering change:
- Separation: This is perhaps the most challenging step, Chaachouh notes, in which individuals grapple with letting go of the familiar
- Transition: Here, there’s a delicate balance between the old and the new. It’s a phase of metamorphosis and understanding why the change is happening. “This is why change management concepts are very important,” she adds.
- Adoption: This marks the embrace of the new normal. Chaachouh explains it thusly: “We are now in our new current state, which is the future state, and this is what we’re going to be doing moving forward.”
Now, companies gravitate towards formalized change management. “Change management has become a discipline for companies to adopt these concepts, not only due to the results that they’ve seen but also because the formal structure has created processes and tools for those organizations,” Chaachouh says.
Unpacking the ADKAR Model
In other words, change management isn’t abstract; it is grounded in systematic models that can be implemented across corporations. One such model that has gained traction globally is the ADKAR model, which stands for awareness, desire, knowledge, ability, and Reinforcement.
The ADKAR method was introduced by Jeff Hyatt after his comprehensive study of change patterns across 700 organizations. A distinguishing feature of this model is its emphasis on individual change within a corporate environment. It pivots on the understanding that change originates from within, starting at the individual employee level and radiating outwards.
Chaachouh elaborates on some key steps of the ADKAR model:
- Awareness ensures that there’s an internal recognition and comprehension of the ‘why’.
- Desire makes sure employees see the value, for instance, in having a connected gas detection device because of its tangible benefits.
- Knowledge underscores that employees fully grasp the nuances of the change management or the new technology.
- Ability ensures employees and the organization can facilitate connected gas safety and the organizational changes entailed.
- Reinforcement helps in transition through the stages – from the present state to the future state, which will yield specific benefits based on a company’s unique criteria.”
Chaachouh says her company believes the success of connected gas detection is rooted in effective onboarding, thorough implementation, and widespread adoption and that the ADKAR model aligns well with that.
“It fits into our value system, but it also fits into the value system of our clients by ensuring successful adoption of the safety solution,” she says.
Again, the ultimate goal here is worker safety and ensuring every employee returns home safely to their families, Chaachouh stresses. To that end, her company offers dedicated client implementation coordinators when onboarding new clients who assist them in incorporating the ADKAR method for heightened success.
Measuring Change Management
Because connected gas detection is tied specifically to workplace safety, understanding and measuring the impact of change management is vital. It comes down to one ultimate question: How can we discern tangible benefits? The answer comes down to understanding the client, Chaachouh explains.
“We focus on the success criteria and the project scope that has been outlined with the client,” she says. “There are methods of quantifying that and ensuring that we have achieved the client’s success criteria and that we remain within the project scope to achieve their goals. And then internally within corporations, they will quantify the results of the ADKAR method, with the change in the safety culture within the organization.”
Chaachouh adds that her company offers an analytics platform to aid this journey. “This platform provides data on usage, compliance, and gas readings,” she explains, offering a snapshot of the technology’s integration.
However, she underscores the customization inherent in the process. “Every client’s needs and benchmarks differ,” she concludes. Though the specific metrics might vary, the goal remains consistent: creating a safer workspace.
The key is to ensure that the metrics help gauge shifts in a company’s safety culture. The results? A decrease in site-related incidents, increased user awareness, and adoption.
“That has been the biggest payoff,” Chaachouh notes, “finding that the end users are adopting the solution that the change management is trying to facilitate, and the knowledge and the desire for the change that is reinforcing the change.”
This article originally appeared in the October 2023 issue of Occupational Health & Safety.