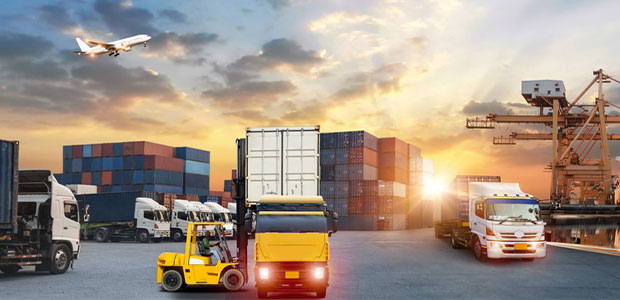
Occupational Safety and Health in Supply Chain Management
- By Devin Partida
- Jan 28, 2022
Supply chain management has become a point of focus for many organizations today. Logistics networks face increasing demand and complexity, and businesses are investing more in maximizing efficiency. However, these efforts may overlook occupational health and safety in the name of speed and profitability.
Transportation and shipping have the second-largest number of workplace injuries resulting in days away from work of any industry. Supply chains must ensure they don’t sacrifice safety for efficiency as they face increasing pressure from the markets they serve. Here are five ways supply chain managers can improve on-site health and safety.
Increase Data Collection
The first step to improving occupational health and safety is understanding each workplace’s unique risks.
Supply chains can gain this understanding by increasing their data collection practices. Internet of Things (IoT) sensors and electronic logs can provide insight into where and how incidents occur, informing more effective mitigation strategies.
Supply chains can feed safety data into artificial intelligence (AI) algorithms. These programs consider tens of millions of options in a fraction of a second, highlighting the most effective fixes for prominent safety issues.
Distance Workers from Hazards
Another important step in supply chain health and safety is removing workers from the most hazardous parts of the job. Robots can automate dangerous tasks such as heavy lifting, picking items from high shelves and moving materials.
Proper lifting techniques and frequent breaks can reduce repetitive strain injuries from these processes, but it’s more effective to remove the risk entirely. Automating these tasks can also help workers avoid getting tired. They’ll then be more alert working in other areas with less danger of injury.
Improve Communication
One of the most significant barriers to supply chain safety is communication. Logistics networks are complex systems, so it’s not always easy to learn of hazards as they emerge. More efficient communication systems can help all workers stay up to date on current risks or new safety policies.
IoT sensors can help by sending real-time alerts of emerging hazards, like a spill or weakening shelf. Workers will then know to watch out for and avoid or fix these hazards before they cause injuries. Organizations should also encourage employees and separate facilities to share safety considerations they’ve noticed to create a unified effort to improve overall safety.
Align Safety Standards and Policies
Many supply chains have facilities overseas. Different locations may face various regulatory landscapes, leading to uneven policies and standards across an organization. Supply chain management should compare all these considerations to create cohesive standards that apply to every facility.
Part of this alignment should include holding contractors to the same standards. Studies show that applying these pre-qualifications to contractors can lead to a 20 percent reduction in total safety incidents and days away from work.
Review Safety Measures Regularly
After implementing other safety controls, supply chain management should review their policies annually. As facilities grow, implement new technology or face rising demand, their safety considerations could shift. Reviewing safety data can highlight any trends that deserve attention.
Supply chains may find some safety policies ineffective as new data emerges. Similarly, they may see how changes in one area had considerable benefits, making it a promising candidate for more widespread application. Reviewing these considerations regularly will help supply chains maintain high safety standards despite changing circumstances.
Supply Chain Safety is Challenging but Necessary
Supply chains are complex, but that doesn’t mean that ensuring high safety standards is impossible. Logistics networks can overcome long-standing challenges to protect their workers’ health and safety with better management practices.
These five steps are not an exhaustive list of what supply chain managers can do to improve safety, but they are some of the most effective changes. Companies that include these considerations can remain efficient without sacrificing worker protection.