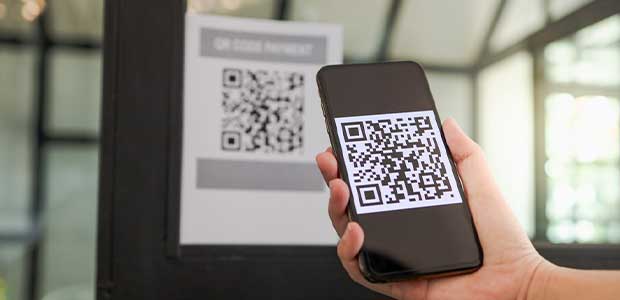
Construction Technology is Shaping the Post-Pandemic Workplace
Employers are encouraged to take a modern-day approach to make sure safety is put first.
- By David Brian Ward
- Jun 21, 2021
During the pandemic, construction was classified as an essential industry across most of the USA. Given its experiences working through the crisis, construction can offer a lot of insight to businesses that are now re-opening. Specifically, how to use technology to keep people safe at work, even after we shift to a post-pandemic world.
Early Pandemic Lessons Learned
When the COVID-19 pandemic first hit, general contractors (GC) were forced to take a closer look at the way workers, subcontractors and visitors come on a jobsite.
The traditional process of passing around a clipboard and pen for everybody to sign in would no longer work. It wasn’t because they feared sharing a clipboard would spread COVID-19 (it can’t). It was because they added more steps – health screenings and temperature checks – to the already time-consuming process of signing into a jobsite.
With the pandemic, everybody had to be interviewed and their responses securely recorded. When the check in process was complete, the information was either put into a spreadsheet or added to a growing stack of paperwork. Staff would spend hours conducting health screenings and then inputting the data or, more typically, throwing the check-in logs in a box and hoping they would never be needed.
Once it became clear that COVID-19 wasn’t going away anytime soon, paper-based record keeping systems showed their weaknesses. Even with data entered into a spreadsheet, contact tracing was still nearly impossible. There wasn’t even a way to know if an infected worker was still at a jobsite.
Headlines featured the frequent shutdowns of construction projects due to COVID-19 outbreaks. GCs feared additional shutdowns, having to send workers home for 14 days and possibly violating OSHA regulations based on the CDC guidelines.
Arguably, some of those shutdowns could have been avoided. According to Rod Courtney, health, safety and environment manager at electric transmission engineer Ampirical, “When the COVID-19 pandemic first hit, employees reporting to the office or a construction site were not allowed to enter without first having their temperatures taken and answering health questions in a .pdf.”
As another way to protect employees, Ampirical uses a machine to take employee temperatures. The machine captures the data from the temperatures and connects it to the company’s HR systems and building security. That same system also offers facial recognition so that employees and visitors can be tracked to the point of entry. Still, it was difficult to keep up with everybody on a job site. Courtney added, “It wasn’t long before those forms created mountains of files that were impossible to use.”
The Resurgence of QR Codes
In response, the tech industry stepped in with digital check-in apps based on QR codes. The apps eliminate paper-based processes and face-to-face interviews while providing a secure way to answer health questions and do quick and accurate contact tracing. Since QR codes have become ubiquitous in our daily lives, it was easy to adapt them for the office knowing there wouldn’t be a learning curve for anybody checking in.
Still, some employees were reluctant to participate in contact tracing for fear of “big brother” watching. While employers could mandate the digital check in, they were able to allay employee fears by choosing private check in and secure contact tracing.
According to construction litigation attorney Brian Junginger, “Since the health screening data is saved only on the employee’s phone, the answers to the questions are protected. Yet, the employer can still securely conduct private contact tracing without having access to the employee’s personal health information or any other data on the employee’s smartphone.”
The Safety Risks of Not Knowing Who’s Onsite
The pandemic forced awareness of safety risks caused by not knowing who is on your jobsite. This information is critical for emergency response, compliance and security. After using digital check in, GCs discovered they now have a better way to manage that process.
It was time to retire the paper sign-in logs with illegible handwriting and the sticky “Hello, my name is” badges. In hindsight, such processes were long overdue for a digital upgrade – one that prioritized safety.
Job Site Lessons for the Office Workplace
As employees return to the office, many businesses are requiring everybody onsite check-in and verify their identity. This includes employees, visitors and vendors. Some businesses want proof of vaccination; this is easy enough to do by simply adding from a technology app point of view. However, the decision to require a COVID-19 vaccination is still up to many employers.
A digital record is the best way to verify identity, the time of arrival and departure and privately determine vaccination or health status. A digital record also protects the company if they need to prove compliance, perform contact tracing or notification, or reconcile service, delivery or subcontractor invoices.
Going forward, health screenings make sense year-round. Nobody wants sick people at work. Screenings for seasonal flu will eventually replace the COVID-19 protocols.
Behind the scenes, check-in data and analytics provides insights into many business functions. Examples include spotting employee trends and following OSHA guidelines and state safety mandates.
The pandemic has raised awareness of a whole range of safety issues in the workplace that come under OSHA’s purview. The urgency is driven by the lessons learned from COVID-19 and the Biden Administration calling for an increase in the number of OSHA inspections. The safety protocols introduced during the pandemic and the related technology such as digital check in, facial recognition and temperature screenings will continue to evolve and become part of our daily business norms.