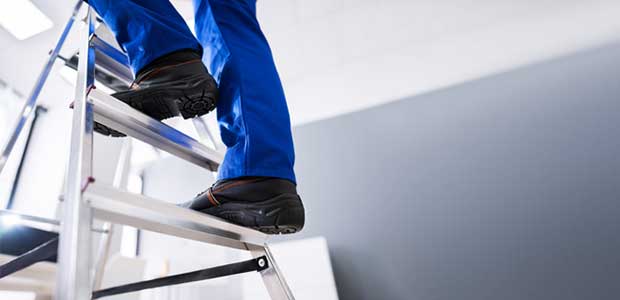
Problems with Safety Management: Accident Issues
Clear communication of objectives can play a big part in avoiding confusion and clarifying expectations.
- By Peter Furst
- May 25, 2021
An accident investigation was conducted in a commercial high-rise office building. The investigator started out with where did the accident happen? It occurred on the fourth floor. The next question was, "When did it happen?" The answer: it happened at 11:15 AM. This was followed by, "What happened?" A worker fell of a step ladder while installing duct work. Then: How did the fall occur? The worker was on the top step of the ladder working when he lost his balance and fell.
After talking to the injured person and others working in the area who were able to contribute to the investigation; the conclusion was that the worker was working unsafely because the standards as well as company safety program state that no work should be done by standing on the top two steps of a step ladder. The safety manager then discussed this with the foreman indicating the worker violated a basic safety rule, and should be admonished and made to understand that such behavior is unacceptable.
Back at the office he reviews a summary of all accidents to that date on the various company work sites and found three other ladder use accidents happened that year. He then informed management that all the workforce should be given a refresher training on all ladder use. Problem solved... right? Not really. The safety manager should have asked the foreman as to why he did not observe this in his walks around the site that morning.
Better yet he should have asked why did the worker use a ladder that was too short for that task. This may have pointed out that a taller ladder was not available, and that there was a concerted “push” from supervision to improve on production. This would have highlighted another significant reason for the accident as poor planning on the part of managements for not having sufficient appropriate ladders available on site.
Basis of Control
It is generally some act on a worker’s part that ends up resulting in the accident. Over the years, there have been numerous studies of accident data which indicated that just about all accidents are caused by workers making choices which lead to incidents, injuries, and ultimately losses (see Herbert Heinrich, & Frank Bird on accident causation). As a result, safety practitioners have structured their organizational programs, policies, and procedures to generally focus their interventions to deal with controlling the physical environment and more importantly the action and behavior of the part of the workforce.
The underlying premise governing safety performance improvement is that somehow by "fixing" the worker, most safety problems will be resolved. There is no question that the workers do have control over their own behavior, and that they do make choices or mistakes that sometimes lead to incidents, but in the workplace, there is much, much more at play than individual worker decisions and choices. A significant, overlooked area is the jobsite management's ability to exercise considerable oversight and control over virtually everything that transpires at the workplace, involving planning, organizing, staffing or task assigning, directing, problem solving, coordinating and controlling, including affecting the worker's decision-making, as well as safe behavior.
Typical Practices
Safety performance improvement strategies typically start with a review of past losses. From this analysis flows the interventions for the upcoming time period. These interventions typically include more training, emphasis on certain program elements, writing of new procedures, or more rigorous inspections. More than likely, in the short-term, some of these interventions do garner improved result in the safety outcome metrics. But in the long run, the results never live up to expectations. And so more training, retaining, priority programs, incentives, or discipline are instituted which ultimately result in less than stellar outcomes.
Some of this is because the improvement strategy is based on historic data and the future is never exactly the same as the past. The data analyzed may not give a true picture of all the contributing causes, see example above. The focus generally is on the worker and not on the task factors, performance objectives, operational systems, work climate, and culture which influence the worker’s actions. Focusing on "changing" the worker's behavior does not remove the underlying drivers of the behavior. These remain and influence the actions of the next worker. This approach to safety improvement has been in effect for over a century, and is still utilized by many construction organizations.
Safety objectives are usually out of alignment with business goals. Safety management is not integrated into operational processes, and safety metrics have little relationship to measures used to manage the operation. There should be an organizational integrated strategy with defined objectives, aligned metrics, and achievable goals. Safety should report to senior management and have a part in the operation's overall strategy. Safe operations should be an organizational core value—it should be instinctual.
ConclusionTo solve the safety problem, we primarily have to look at the people overseeing the operations, (foreman, supervisors and management) much more than we do the "worker". We will find most of our solutions at the organizational/operational level than the unsafe condition or worker’s act level. It is the management people who define the values and create the culture that delineates the norms, symbols, rituals, artifacts, heroes, and stories of the culture. We must assess the work climate to see what is deemed acceptable and what is not. We have to look at management in the organization and the systems they devised to drive it. How much emphasis is placed on leadership as opposed to management? Is dealing with risk and safety an intrinsic part of everything that is planned and done? It is leadership that inspires excellence while management stresses achieving goals. Are people put into situations where they have to choose between production goals and safe work practices? We have to determine why workers do what they do, how the organizational systems allow and the work climate encourages such actions. Until we get to that causal level, we are not going to get very far in improving our safety results.
There is another issue to note. Unless we eliminate the systems that allowed risk to enter into the operations as well as allowed it to exist, intervention focused on changing or removing a worker will not effectively solve the problem. The system will eventually "get" the next worker and then the next and the next and so on. Therefore, management must be vigilant to ferret out any possible situation that may cause confusion or is open to misinterpretation. Clear communication of objectives can play a big part in avoiding confusion and clarifying expectations. The organizational metrics, how people are measured and rewarded, the culture of the organization, and the work climate all may lead the worker to thinking that unsafe behavior is somehow okay. Excess pressure to achieve goals or to meet the schedule increases stress and may lead to errors resulting in inferior work quality or worker injuries.