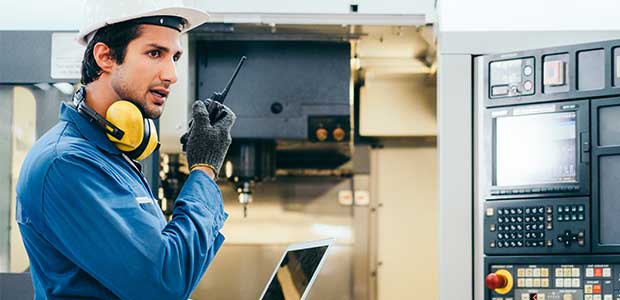
Lockout/Tagout Procedures—Keep it Simple, Keep it Safe
Employing these techniques can be the difference between a safe, routine maintenance activity and a serious injury.
- By Tom Burgess, Justin Wilson
- Dec 01, 2020
If you have ever pulled your car into a garage for an oil change, the first thing the technician asks you to do is take your keys out of the ignition and put them on the dashboard. It isn’t enough to make sure the car isn’t running—before someone puts their hands near the oil pan, they need to be certain there is zero chance the engine will come roaring to life. In rendering the car inoperable, they are protecting themselves—and you, too—by taking the possibility for human error out of the equation.
The same principle applies when it comes to machinery on the work site, whether it’s an HVAC system or a piece of production equipment. According to OSHA, lockout/tagout (LOTO) protocols are “specific practices and procedures to safeguard employees from the unexpected energization or startup of machinery and equipment, or the release of hazardous energy during service or maintenance activities.” In this column, we’ll provide a high-level overview of lockout/tagout procedures and best practices to ensure they are taken seriously at all levels of the organization.
Controlling Hazardous Energy
Workplace safety is always important, and one would hope that equipment operators and those in their vicinity have the appropriate safety precautions and training in place during normal routine operations. But what about non-routine activities, such as needing to repair something? We have all heard horror stories: A worker sticks their arm into a machine to clear out a jam, or steps into an industrial oven to make an adjustment, and an unaware colleague turns on the power. LOTO procedures are meant to prevent such disasters.
LOTO programs are all about the control of hazardous energy. That means electricity of course, but also anything else that can hurt someone, including air, heat, water, chemicals, hydraulics and so on. During the course of typical operations, most machinery is equipped with physical safeguards to protect operators, such as the handguard on an industrial saw. But during service and maintenance, it may be necessary to remove or disable these safeguards to conduct repairs. It is vital that hazardous energy is controlled and dissipated before this can happen.
The eight basic steps to a LOTO procedure are as follows:
1. Prepare for the shutdown. An important part of preparedness is being appropriately trained and aware of the hazardous energy sources involved and how to control them.
2. Notify affected employees. Ensure that workers in the affected area are fully aware of the impending lockout.
3. Shut down the equipment. This should be done in a safe and orderly manner, in accordance with the equipment-specific procedure or operating manual.
4. Isolate energy sources. For example, a circuit breaker or valve that supplies energy to the equipment.
5. Apply LOTO devices to energy sources. This is a device, such as a padlock, that physically prevents the equipment from being energized. Each person involved in the lockout (OSHA defines them as authorized employees) will have their own lockout device, and it will feature a tag displaying who locked it out, when and why. Multiple lockout devices on one piece of equipment are common.
6. Release/control all stored energy. For example: compressed air, capacitors that hold an electrical charge or stored mechanical energy like compressed springs.
7. Verify the lockout. This is the most important step, and the one most easily overlooked. It is absolutely critical that personnel double-check that all hazardous energy has been isolated.
8. Maintain the lockout. Be certain that the equipment remains in a lockout state until service can be safely restored.
Just as important as following these steps is ensuring that appropriate LOTO release protocols are followed and that service is restored after the work has been completed. This means making sure that workers and materials have been cleared from dangerous areas, that all lockout devices are removed and equipment tested and that the appropriate personnel have been informed that the LOTO is removed. None of the equipment should be re-energized until these actions are taken, at which point workers can be notified that equipment is ready for use.
A potentially dangerous form of hazardous energy, which may be taken for granted, is gravity. If you have ever slid under the car in your garage to perform a repair, you were probably keenly aware of the two tons of unforgiving metal balanced right above you. Which is why, if you are smart, you won’t rely on a floor jack to keep the car aloft. You will also use jack stands in case the jack’s hydraulics should fail. Gravity, after all, can never be turned off.
Best Practices for LOTO Safety
Regardless of your role in the organization—whether you’re a maintenance worker, a safety officer or the president of the company—it pays to be aware of these common-sense best practices for an effective LOTO program and equipment-specific procedures:
- Keep it simple. Focus on the user, not on the OSHA standard. You can develop the most detailed and thorough written procedure in the world, but if the user doesn’t understand it, it isn’t useful.
- Be consistent. Facilities may have hundreds or thousands of pieces of complex equipment, each with its own protocols. Strive to simplify things by ensuring consistency in the way equipment is labeled and procedures are described.
- Enforce accountability. If an employee has not been properly trained and coached on equipment and procedures and ends up hurting themselves or someone else, it isn’t just their fault – it may also be yours. Ensure that safety training is conducted and requirements are enforced at all levels of the organization.
- Did we mention “Verify”? We said it before, but we’ll say it again. There have been real-world situations in which initial LOTO procedures have been carefully followed, but a failure to observe the final step—verifying that all energy sources have been controlled—has damaged or destroyed equipment, caused serious injury and even caused some of the many fatalities that still happen every year.
Lockout/Tagout procedures need not be unnecessarily complicated, and we hope this has cleared up some of the mystery surrounding this vital safety practice. When you hear about a worksite injury or death involving machinery or energy, chances are that steps in the LOTO process were missed. By ensuring that programs are effective and enforced, and that everyone is trained on what to do and how to do it, we can keep ourselves and others safe.
This article originally appeared in the November/December 2020 issue of Occupational Health & Safety.