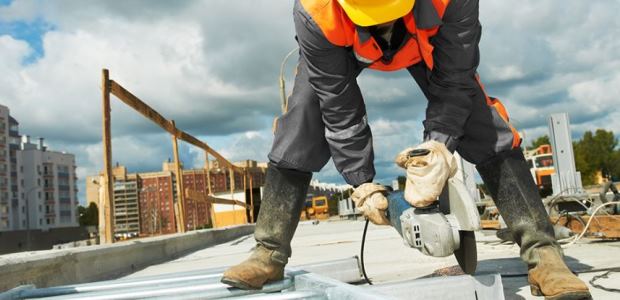
Take Matters into Your Own Hands: Understanding Hand Injuries in the Workplace
All too often, hand injuries occur when employees are distracted and aren't focused on where they are or what they're doing. It's incredibly important for employers to eliminate as many distractions as possible.
- By Amy Meister
- Aug 01, 2018
The hands are among a worker's most valuable tools, used for everything from threading delicate electrical wires to cutting through a thick steel pipe. Yet, despite how often the hands are used, hand safety and injury prevention can often be overlooked by both employers and employees.
According to the U.S. Bureau of Labor Statistics (BLS), more than 1 million workers are sent to the emergency room each year because of serious hand injuries. From lacerations and cuts to burns and broken bones, these injuries can be costly for employers. In 2011, the National Safety Council estimated the cost of hand injuries, and the results may be surprising to some employers: The direct cost of a laceration can be $10,000, stitches are often $2,000, and a severed tendon can be more than $70,000. It's also important to note that these numbers don't account for the indirect costs, like time away from work and lost productivity due to long-term damage, that are associated with even minor hand injuries.
The good news is that with the right tools, resources and education, many workplace hand injuries can be prevented. In order to protect employees from injury and reduce workers' compensation costs, employers need to first understand the who, what, where, when, and why of hand injuries.
Who is At Risk for Hand Injuries?
Everyone is potentially at risk for hand injuries. Regardless of gender, age, or industry, employers should always take steps to protect employees from even minor bumps and bruises. However, there are certain groups of employees who may be at a higher risk. Less-experienced workers, for example, or those whom the Occupational Safety and Health Administration considers to be new to the workforce, may be at higher risk for injuries at work. Whether it's due to less on-the-job experience or a heightened sense of pressure to complete tasks quickly, employers should take special care especially with less-experienced workers. Make sure new hires feel comfortable speaking up about safety concerns and create a comfortable work environment where questions are both welcome and encouraged. Safety training is also an important step, especially for younger workers who are new to the industry and unfamiliar with common, and potentially hazardous, machinery and tools.
Employers also should take steps to make sure workers over the age of 55 are protected. While less likely to be injured on the job given their level of experience, workers in this age group often require a longer recovery time and may sustain more serious injuries when they do get hurt at work. According to BLS, workers ages 55 and older can require a median of 12 to 14 days away from work after a non-fatal injury, while workers between the ages of 20 and 44 typically require only 5 to 9 days. This may result in costs stemming from days off work and lost productivity. Employers can help workers in this age group prevent injury by implementing a workplace wellness program that encourages a focus on ergonomics, stretching, and healthy lifestyles. Pay special attention to any previous injuries or illnesses that may make it difficult for any worker to properly lift heavy objects or see thin blades on a piece of machinery.
What Types of Hand Injuries Are the Most Common?
The hands are incredibly versatile, but they're also exposed to a variety of threats that can result in injuries ranging from minor cuts and bruises to serious lacerations and burns. Some of those injuries include lacerations, crushes, avulsions or detachments, punctures, and fractures.
- Lacerations. Lacerations are deep cuts or tears in the flesh. While most lacerations are easily treated, nerve or tendon damage is possible if the cut is deep. This can result in longer recovery time and possible long-term damage.
- Crushes. Crushes occur when a body part—in this case, the hand, wrist, or arm—is caught between heavy equipment or machinery and another hard surface, like the floor or a wall. Depending on severity, this type of injury often causes permanent damage, particularly in cases where the crush injury prevents blood supply to the muscles.
- Avulsion fractures or detachments. Avulsion fractures are fractures that occur when a bone is moving one way and a tendon or ligament is moving or pulled in the opposite direction. A common avulsion injury occurs when a wedding ring or other piece of jewelry gets caught on machinery and pulls a small piece of bone that is attached to a tendon or ligament away from the main part of the bone. Detachments can occur the same way but are typically more serious and often involve entire fingers or hands becoming separated from the body.
- Punctures. Punctures often involve sharp objects, such as nails, needles, knives, tacks, machinery, or other tools. Punctures occur when one of these objects penetrates the skin and causes a wound that is typically narrower and deeper than a cut or scrape.
- Fractures. A fracture, or a break in one of the bones of the hand, is often caused by trips, falls, and crushes. Fractures occur in the bones of the wrist and typically require weeks to months of recovery time.
At MedExpress, one of the nation's largest occupational medicine and workers' compensation providers, more than half of hand injuries seen as a result of workers' compensation visits are due to open wounds, such as lacerations. MedExpress also commonly sees dislocations and sprains, as well as superficial injuries of the hand and wrist, such as bruises, abrasions, and blisters.
Where Are Hand Injuries the Most Common?
Hand injuries are not limited to just one industry. They happen every day across a wide variety of jobs, companies, and work sites. They range from carpal tunnel syndrome in an office setting to burns at a chemical plant.
However, employees who work in construction and manufacturing industries may be at greater risk for hand injuries. Construction, for example, not only involves the use of hammers, saws, and other tools, but also the regular use of large heavy machinery, including bulldozers, dump trucks, and cement mixers. These tools and machinery, when used incorrectly, pose a risk for possible hand and arm injuries through crushing, pinching, puncturing, and more. Employees in manufacturing also frequently operate large machinery, such as drill presses, lathes, and screw machines, that can pose a high risk for hand injuries.
When Are Hand Injuries Most Likely to Occur?
Hand injuries can occur anytime. However, all too often, hand injuries occur when employees are distracted and aren't focused on where they are or what they're doing. It's incredibly important for employers to eliminate as many distractions as possible, especially in work areas where there is frequent use of heavy machinery or power tools. Remind employees to stay alert and focused, and offer them the opportunity to take regular breaks to sit down, stretch, or take a walk.
Why Are Hand Injuries So Common?
Hand injuries can often be blamed on distraction, lack of education, or disregard for safety procedures. While, yes, negligence and inattentiveness are certainly a reason for injury, there is also an opportunity to increase preventative equipment and resources. In fact, in a 2015 study by DSM Dyneema, Majestic Glove, and the American Society of Safety Professionals, more than 400 safety professionals were asked to identify the top reasons why they believed hand injuries occurred in the workplace. The results showed that the majority of respondents believed that lack of personal protective equipment or cut-resistant gloves were to blame.
How Can Employers Prevent Hand Injuries in the Workplace?
Preventing hand injuries in the workplace doesn't have to be time consuming for employers. In fact, simply establishing and enforcing a set of rules and expectations for workers alone can be beneficial. Additional steps can and should be taken to avoid costly injuries, time off work, and lack of productivity. Consider the following preventative measures:
- Provide PPE. Ensure workers are well equipped with personal protective equipment, such as gloves, that helps protect the hands from cuts, lacerations, chemical and thermal burns, electrical dangers, and more. When selecting the type of protective glove for your employees, there are several important factors to consider that may vary based on industry. Not all gloves are made equal. For example, butyl gloves that are made of synthetic rubber to protect against chemical burns may not provide adequate protection against abrasions or cuts. Fabric gloves that protect against chafing may not be sufficient protection for workers who require heat protection. That's why it's important for employers to think about the types of chemicals handled, grip requirements, size and comfort, thermal protection, abrasion and resistance requirements, and duration of contact. Remember also to consider how much of the hand needs to be protected—is only the hand exposed, or does the entire forearm need protection, as well?
- Encourage education and set expectations. Employers should offer education about the tools and machinery used frequently at the work site. Implement a training program to help employees get to know equipment features and the location of important buttons, such as the emergency off switch. A training program also can help highlight danger zones on equipment, such as hot spots and pinch points. Employers also should hang a list of safety tips and workplace expectations in heavily trafficked areas, such as locker and break rooms. Remind employees to remove all rings, necklaces, earrings, and other jewelry before heading to the work site or onto the manufacturing floor, and to always wear gloves. Employees should always stay focused while handling heavy machinery and tools; help them do so by minimizing distractions in areas where potentially dangerous equipment is being used.
- Have an open door policy. Employees should feel comfortable reporting safety issues they identify in the field to supervisors. Employers should often—if not always—be present and available. Remind employees that your door is always open to report possible safety issues immediately. If and when issues do arise, take it as an opportunity to schedule one-on-one time with each employee and review what happened, what could have prevented the problem, and any other safety procedures to remember. Open and honest communication between employee and supervisor is key when confronting safety issues head on, because employees are the eyes and the ears in the field.
This article originally appeared in the August 2018 issue of Occupational Health & Safety.