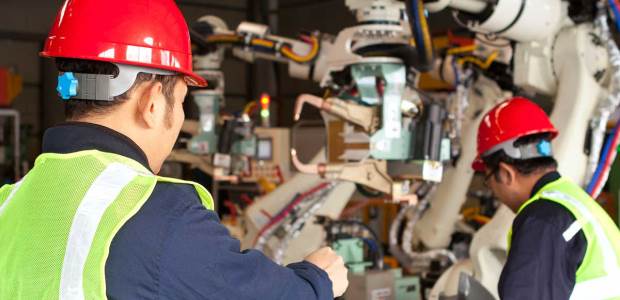
I, COBOT: The Rise of Industrial Robotics and the Need for Employee Safeguarding
In general, OSHA's view on robot safety is that if the employer is meeting the requirements of ANSI/RIA R15.06, the manufacturer has no issues.
- By Carrie Halle
- Feb 01, 2018
Tech executive and billionaire entrepreneur Elon Musk recently took to Twitter calling for the regulation of robots and Artificial Intelligence (AI), saying their potential, if left to develop unchecked, threatens human existence. Google, Facebook, Amazon, IBM, and Microsoft joined in with their own dire forecasts and have jointly set up the consortium "Partnership on AI to Benefit People and Society" to prevent a robotic future that looks not unlike the "Terminator" movie series. National media heightened panic by broadcasting a video released by a cybersecurity firm in which a hacked industrial robot suddenly begins laughing in an evil, maniacal way and uses a screwdriver to repeatedly stab a tomato. The video demonstrated how major security flaws make robots dangerous, if not deadly.
Is all this just media hyperbole, or are robots really that hazardous to our collective health? Are productivity-driven manufacturers unknowingly putting employees at risk by placing robots on the plant floor? What kind of safeguarding is required? Should robots be regulated, as Elon Musk believes?
'Dumb' Machines vs. Cobots
Until now, the robots used in manufacturing have mostly been "dumb" robots—that is, room-sized, programmed machinery engineered to perform repetitive tasks that are dirty, dangerous, or just plain dull. Typical applications would include welding, assembly, material handling, and packaging. Although these machines are very large and certainly have enough power to cause injuries, the instances of employees actually being injured by robots is relatively rare. In fact, during the past three decades, robots have accounted for only 33 workplace deaths and injuries in the United States, according to data from the Occupational Safety and Health Administration (OSHA).
So, you might ask, why the sudden uproar when there are already 1.6 million industrial robots in use worldwide? Most of the clamor behind calls for regulation stems from a new generation of robots called "cobots" (collaborative robots) that are revolutionizing the way people work. Unlike standard industrial robots, which generally work in cages, cobots have much more autonomy and freedom to move on their own, featuring near "human" capabilities and traits such as sensing, dexterity, memory, and trainability.
The trouble is, in order for cobots to work productively, they must escape from their cages and work side by side with people. This introduces the potential for far more injuries. In the past, most injuries or deaths happened when humans who were maintaining the robots made an error or violated the safety barriers, such as by entering a cage. Many safety experts fear that since the cage has been all but eliminated with cobots, employee injuries are certain to rise.
Because cobots work alongside people, their manufacturers have added basic safety protections in order to prevent accidents. For instance, some cobots feature sensors so that when a person is nearby, the cobot will slow down or stop whatever function it is performing. Others have a display screen that cues those who are nearby about what the cobot is focusing on and planning to do next. Are these an adequate substitute for proven safeguarding equipment? Only time will tell.
There is another, more perilous problem with robots in general: Robots are basically computers equipped with arms, legs, or wheels. As such, robots are susceptible to being hacked. But unlike with a desktop computer, when a robot is hacked it has the ability to move around. For instance, a disgruntled ex-employee could hack into a robot and re-program it to harm people and destroy property. The more functionality, intelligence, and power a robot has, the bigger its potential threat.
Types of Injuries
OSHA lists four types of accidents resulting from robot use in the Technical Manual "Industrial Robots and Robot System Safety" (Section IV: Chapter 4).
- Impact or collision accidents. Unpredicted movements, component malfunctions, or unpredicted program changes related to the robot’s arm or peripheral equipment could result in contact accidents.
- Crushing and trapping accidents. A worker's limb or other body part can be trapped between a robot's arm and other peripheral equipment, or the individual may be physically driven into and crushed by other peripheral equipment.
- Mechanical part accidents. The breakdown of the robot's drive components, tooling or end-effector, peripheral equipment, or its power source is a mechanical accident. The release of parts, failure of gripper mechanism, or the failure of end-effector power tools (e.g., grinding wheels, buffing wheels, deburring tools, power screwdrivers, and nut runners) are a few types of mechanical failures.
- Other accidents. Other accidents can result from working with robots. Equipment that supplies robot power and control represents potential electrical and pressurized fluid hazards. Ruptured hydraulic lines could create dangerous high-pressure cutting streams or whipping hose hazards. Environmental accidents from arc flash, metal spatter, dust, electromagnetic, or radio-frequency interference also can occur. In addition, equipment and power cables on the floor present tripping hazards.
Robot Safety Regulations
Robots in the workplace are generally associated with machine tools or process equipment. Robots are machines, and as such, must be safeguarded in ways similar to those presented for any hazardous remotely controlled machine, falling under the OSHA General Duty Clause (5)(a)(1), which requires employers provide a safe and healthful workplace free from recognized hazards likely to cause death or serious physical harm. Also applicable are OSHA 1910.212 (a)(1) "Types of Guarding" and 1910.212 (a)(3)(ii) “The point of operation of machines whose operation exposes an employee to injury shall be guarded.”
Various techniques are available to prevent employee exposure to the hazards that can be imposed by robots. The most common technique is through the installation of perimeter guarding with interlocked gates. A critical parameter relates to the manner in which the interlocks function. Of major concern is whether the computer program, control circuit, or the primary power circuit is interrupted when an interlock is activated. The various industry standards should be investigated for guidance; however, it is generally accepted that the primary motor power to the robot should be interrupted by the interlock.
In general, OSHA's view on robot safety is that if the employer is meeting the requirements of ANSI/RIA R15.06, Industrial Robots and Robot Systems—Safety Requirements, then the manufacturer has no issues. For guidance on how to select and integrate safeguarding into robot systems, refer to the Robotic Industries Association's Technical Report: RIA TR R15.06-2014 for Industrial Robots and Robot Systems—Safety Requirements and Safeguarding.
Published by the American National Standards Institute (ANSI) and Robotic Industries Association (RIA), ANSI/RIA R15.06 is a consensus standard to provide guidance on the proper use of the safety features embedded into robots, as well as how to safely integrate robots into factories and work areas. The latest revision of the standard, ANSI/RIA R15.06-2012, references for the first time ISO 10218-1 & 2 to make it compliant with international standards already in place in Europe. Part 1 of ISO 10218 details the robot itself; Part 2 addresses the responsibilities of the integrator.
There are also new requirements in ANSI/RIA R15.06-2012 for collaborative robots; in this case, ISO 10218 and the ISO/TS 15066 Technical Specification. This standard clarifies the four types of collaboration: Safety Monitored Stop, Hand Guiding, Speed & Separation Monitoring, and Power & Force Limiting. ISO/TS 15066 holds key information, including guidance on maximum allowable speeds and minimum protective distances, along with a formula for establishing the protective separation distance and data to verify threshold limit values for power and force limiting to prevent pain or discomfort on the part of the operator.
The requirement for risk assessments is one of the biggest changes in the new RIA standard. The integrator, or the end user if they are performing the job of an integrator, now must conduct a risk assessment of each robotic system and summarize ways to mitigate against these risks. This may involve procedures and training, incorporating required machine safeguarding, and basic safety management. Risk assessments calculate the potential severity of an injury, the operator's exposure to the hazard, and the difficulty in avoiding the hazard to arrive at a specific risk level ranging from negligible to very high.
In the future, as cobot use rapidly expands throughout industry, regulation of this technology will grow more focused and specific. Consider this: Although cobots currently represent only 3 percent of all industrial robots sold, they are projected to account for 34 percent of the industrial robots sold by 2025, a market that itself is set to triple in size and dollar volume over that period.
Conclusion
The next 10 years will be pivotal for American manufacturing, and success largely depends on companies' ability to navigate the transition from traditional manufacturing to Industry 4.0-style automation and the widespread use of robots. While few people have as dire a view as Elon Musk on the subject, it is critical that employee safety is not lost in the excitement as we shepherd robots out of their cages to work hand in hand with humans.
This article originally appeared in the February 2018 issue of Occupational Health & Safety.