Preventing the Five Major Causes of Industrial Fires and Explosions
By: Stephen Watkins, Applications Engineer
Industrial fires and explosions cost companies and governments billions of dollars every year, not to mention the loss of life, which can’t be described in monetary terms. According to the most recent fire statistics from the National Fire Protection Association (NFPA), an average of 37,000 fires occur at industrial and manufacturing properties every year. These incidents result in 18 civilian deaths, 279 civilian injuries, and $1 billion in direct property damage.1
These disasters happen for many reasons, often because managers and employees aren’t aware of the risks that surround them at work every day. When dealing with the risk of fires and explosions, it’s important to understand the most common causes.
Combustible Dust
Often overlooked, and highly deadly, combustible dust is a major cause of fire in food manufacturing, woodworking, chemical manufacturing, metalworking, pharmaceuticals, and just about every other industry you can name. The reason is that just about everything, including food, dyes, chemicals, and metals – even materials that aren’t fire risks in larger pieces – have the potential to be combustible in dust form.
And these explosions aren’t easy to contain. In a typical incident, combustible material comes into contact with an ignition source causing a small fire. These small fires go unreported, but they don’t come without consequences. Even small fires in industrial facilities cause loss of product, time and sometimes bodily injury.
The outcome can also be much worse. If there’s dust in the area, the primary explosion will cause that dust to become airborne. Then, the dust cloud itself can ignite, causing a secondary explosion that can be many times the size and severity of the primary explosion. If enough dust has accumulated, these secondary explosions have the potential to bring down entire facilities, causing immense damage and fatalities. Most people recall the Imperial Sugar explosion as an example of a devastating loss due to combustible dust accumulation.
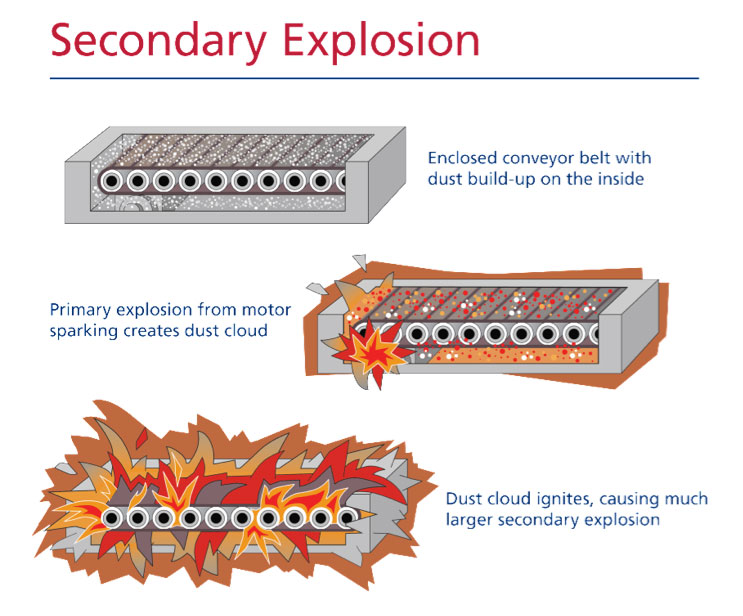
The key ingredient in combustible dust fires and explosions is the presence of dust itself. While dust cannot be eliminated entirely, you can make sure it doesn’t accumulate to a dangerous level simply by following a regular housekeeping regimen.
Take the steps to safely collect combustible dust in any environment:
1. Understand your facility and your responsibilities
It is ultimately your and your company’s responsibility to select safe equipment. You can be held accountable by multiple authorities having jurisdiction (AHJ), including your insurance company, local officials and OSHA.
2. Get to know the regulations, standards and recommendations
Stay up-to-date on the current state of regulations, standards and recommendations so you make informed decisions.
3. Select the safest industrial vacuum for your application
Select equipment that will help you become safe and stay safe, meeting all requirements set forth by your facility, AHJ, insurance company, NFPA, OSHA and, most importantly, your users.
Hot Work
Although hot work is commonly equated with welding and torch cutting, there are many other activities – including brazing, burning, heating, and soldering – that pose fire hazard. This is because sparks and molten material, which reach temperatures greater than 1000⁰F, can easily travel more than 35 feet.2
In 2014, a pier fire in California caused by a welder’s torch resulted in more than $100 million in damage when it caused a partial collapse of a warehouse floor.3 In 2012, three workers performing hot work died disassembling a metal crude oil tank. The sparks from the work ignited vapors inside the tank, causing a fire that then spread to nearby woods.4
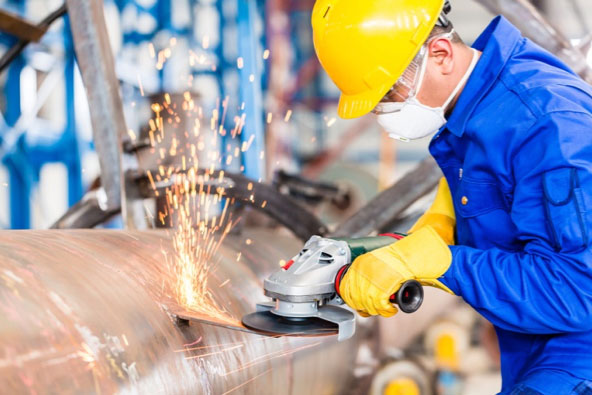
Hot work is also a major culprit in combustible dust fires, as the sparks generated from the work can ignite in the surrounding area.
In one incident in North Carolina, three contract welders were seriously burned when sparks ignited the wood dust in the silo where they were working. The investigation found a trifecta of problems; the silo hadn’t been cleaned of dust before the work began, no hot work permit had been issued, and there was no fire protection and prevention plan in place.5
Like combustible dust incidents, hot work disasters are preventable by following proper safety procedures.
1. Avoid hot work if possible
This isn’t always a feasible solution, but if there’s an alternative, take it.
2. Train personnel
All workers should understand the hazards associated with hot work, any site-specific hazards, the proper policies and procedures, and the use of safety equipment.
3. Ensure that the area is clear of flammable or combustible materials including dusts, liquids, and gasses
4. Supervise the work
Especially if you use outside contractors, make sure a safety professional is on hand to provide supervision.
Flammable liquids and gasses
These fires, which often occur at chemical plants, can be disastrous.
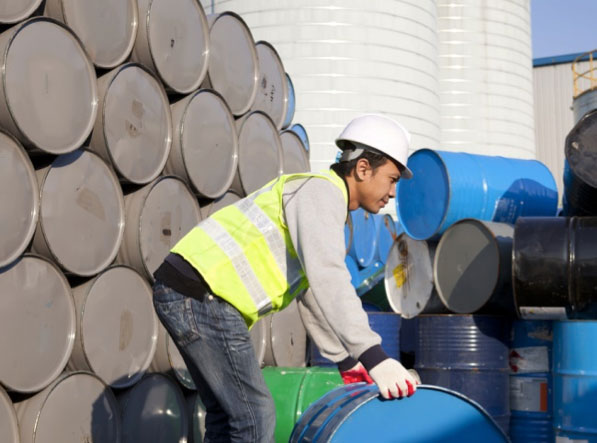
A 2010 power plant explosion in Middletown, CT killed six people and injured more than 50, and can all be traced to flammable gas. In this case, the subsequent investigation revealed hundreds of safety violations, many of which OSHA deemed “willful.” As a result, the agency fined the companies involved $16.6 million, one of the largest penalties ever issued.6
There is certainly some danger inherent in any work involving flammable liquids and gasses, but all available safety precautions should be taken to mitigate these risks.
1. Know the hazards
One major component of prevention is simply knowing the safety information for every liquid on your premises. This information is available on the material safety data sheet (MSDS) that comes with such products.
2. Store flammable liquids properly
Make sure all hazardous materials are stored according to OSHA-compliant procedures.
3. Control all ignition sources
Except for when you’re intentionally heating the flammable materials, keep ignition sources as far away from them as possible.
4. Provide personal protective equipment
This is a must across all categories of fire hazards but especially when liquids and gasses are involved.
Equipment and Machinery
Faulty equipment and machinery are also major causes of industrial fires.
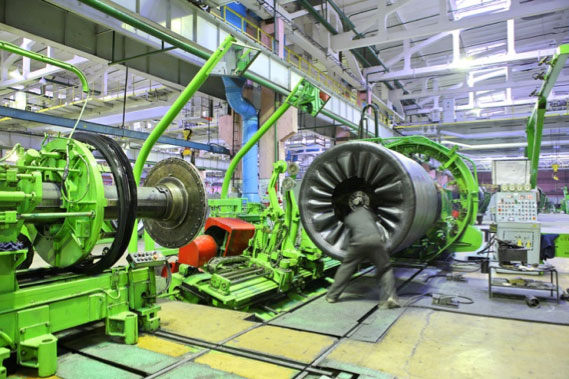
Heating and hot work equipment are typically the largest issue here – in particular, furnaces that aren’t properly installed, operated, and maintained. In addition, any mechanical equipment can become a fire hazard due to friction between moving parts. This risk can be practically eliminated, simply by following recommended cleaning and maintenance procedures, including lubrication.
Even seemingly innocuous equipment can be a hazard under the right circumstances. And, in many cases, the equipment least likely to be thought of as a fire risk turns out to be the biggest problem, due to companies not recognizing the risk and not taking the proper precautions.
Strategies for preventing fires due to equipment and machinery issues fall into three main categories:
1. Awareness
You can’t prevent risks you don’t know exist and neither can your employees. Provide safety awareness training so everyone in your facility knows what risks to watch out for and what to do if they find one.
2. Cleaning and housekeeping
Keep your equipment and machinery – and the area surrounding it – clean. Equipment, especially electrical equipment, which is covered with dirt or grease, constitutes a huge risk. By keeping your equipment and machinery clean, you’ll up your chances that, should a fire start, it won’t have enough fuel available to burn for long.
3. Maintenance
Follow the manufacturer’s recommended maintenance procedures for all of the equipment and machinery in your plant. In addition to reducing your fire risk by preventing overheating, regular maintenance will also keep your equipment working in tip-top shape.
Electrical Hazards
Electrical fire hazards include wiring that is exposed or not up to code, overloaded outlets, extension cords, overloaded circuits and static discharge. The damage caused by these fires can quickly compound thanks to several of the other items mentioned above.
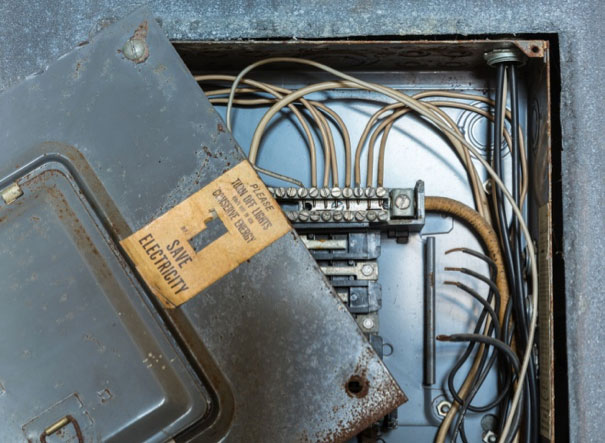
Any of these hazards can cause a spark, which can serve as an ignition source for combustible dust, as well as flammable liquids and gasses.
As with the previously mentioned risks, the key to preventing electrical fires is awareness and prevention. This involves training, maintenance, and abiding by the following best practices:
1. Don’t overload electrical equipment of circuits
2. Don’t leave temporary equipment plugged in when it’s not in use
3. Avoid using extension cords, and never consider them permanent solutions
4. Use antistatic equipment where required by NFPA or OSHA
5. Follow a regular housekeeping plan to remove combustible dust and other hazardous materials from areas that contain equipment and machinery
6. Implement a reporting system so that anyone who observes an electrical fire risk can report it without consequences
Steps to Avoid Fires & Explosions
Building fire safety into your daily operations is key to preventing industrial fires and explosions. These hazards are formidable, but don’t let it intimidate you. Fire safety is mostly a matter of establishing policies and procedures, and then ensuring they are implemented throughout your facility.
Conduct a hazard analysis. A Dust Hazard Analysis (DHA) is one of the requirements of NFPA 652. Although this standard refers to combustible dusts, don’t stop there. Conduct a hazard analysis of your entire facility to discover exactly where your greatest risks lie and what you can do to address them.
Establish fire prevention and emergency procedures. Make sure you have policies and procedures in place that cover everything from smoking, to personal protective equipment, to an emergency evacuation plan. Ensure everyone has access to these documents at all times.
Provide fire safety training. Be sure to provide both general and job-specific fire safety training for everyone working in a potentially hazardous environment.
Implement a regular housekeeping routine. With equipment and machinery running, sometimes 24 hours a day, sparks and static discharge may be hard to avoid entirely, but that doesn’t mean you need to run the risk of a fire or explosion, especially one due to combustible dust. By implementing a regular housekeeping routine, you can significantly decrease the chances of a small spark turning into a huge disaster.
Inspect and maintain your equipment and systems. Keeping all of your equipment and systems in properly working order will enhance safety and make your operations more efficient. This includes maintaining the machinery on your production line, as well as inspecting and testing your fire safety systems, like fire extinguishers and sprinklers. A good rule of thumb is to perform inspections every six months.
Although the causes of industrial fires and explosions cannot be completely eliminated, it is important to understand how to best prevent them to keep your facilities and employees safe.
References: 1. Fire in Industrial or Manufacturing Properties. http://www.nfpa.org/news-and-research/fire-statistics-and-reports/fire-statistics/fires-by-property-type/industrial-and-manufacturing-facilities/fires-in-us-industrial-and-manufacturing-facilities
2. Controlling Hot Work Fire Hazards. https://ohsonline.com/Articles/2009/04/01/Controlling-Hot-Work-Fire-Hazards.aspx
3. Large-Loss Fires in the United States in 2014. http://www.nfpa.org/news-and-research/publications/nfpa-journal/2015/november-december-2015/features/large-loss-fires-2014
4. Fatal Hot Work Accident Kills Three. http://hgi-fire.com/blog/fatal-hot-work-accident-kills-three/
5. Combustible Dust: A Major Hot Work Hazard. http://digital.ncdcr.gov/cdm/ref/collection/p249901coll22/id/12071.
6. $16 Million in Fines After Fatal Blast at a Connecticut Plant. http://www.nytimes.com/2010/08/06/nyregion/06middletown.html?_r=0