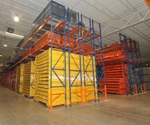
Safety and Warehouse Storage
Emergency preparedness is equally as important as prevention in maintaining a safe workplace.
- By Michelle Coleman
- Aug 01, 2011
Safety is the top priority when designing a warehouse and choosing storage. Well-utilized storage equipment is conducive to creating a safer work environment and reducing workplace injuries for the 145,000 warehouse workers in America. The fatal injury rate in the warehousing industry is higher than the national average for all industries, and taking necessary considerations for storage equipment and warehouse design will help to minimize workplace hazards while also creating an efficient warehouse.
Accidents and injuries in warehouses are preventable and come with many serious consequences. Preventable costs of a rack collapse include worker's compensation and insurance rate increases, fines and safety violations, legal expenses, and replacing storage and damaged material. To avoid the pitfalls and detrimental effects of an accident, use the utmost caution when planning warehouse storage and design. Proper design, installation, and maintenance of storage racks will make the warehouse environment a safe and healthy workplace for all employees.
Choosing a Provider
The first step to warehouse storage safety is choosing an experienced, reputable provider. When you choose a company to assist you with warehouse design and installation, you are placing your trust and employee safety in that company's hands. Conduct research about potential suppliers' safety history, brands used, and look for red flags, such as lawsuits and negative reviews. Researching prospective storage companies will prepare you to choose a reputable supplier.
Designing for Inventory
When choosing storage for a warehouse, the size, shape, and weight of the items to be stored needs to factor into the style of racking that is selected. Ensuring the pallet racking will accommodate the proper object size and weight capacity can reduce falling items and injuries related to overloading. Loads on the racks need to be stacked even and straight to ensure weight capacity is distributed properly. Spacing between items on the racks can affect the stability of storage.
Consider how the items held on racks will be retrieved, and plan accordingly. Heavier and larger loads should be stored on lower or middle shelves to minimize lifting and forklift injuries. Making sure stacked materials are accessible for handling will help to reduce injuries and strain from challenging lifting situations. Ensuring all hazardous chemicals are properly labeled and stored, and an MSDS sheet is kept in an accessible location, is an important step in having an emergency response plan.
Assembly and Maintenance of Storage
Safety begins with an effective warehouse design and installation of storage, performed by personnel experienced in the assembly of racks, according to manufacturer instructions. They will help you assess what will be stored and analyze the size, weight, and quantity to recommend the most suitable products and configuration.
Be sure that adequate aisle spacing is provided to allow forklifts to safely pass and transport loads. Check to make sure racks are not exposed to excessive dampness or other elements that would compromise the structural integrity. Appropriate lighting needs to be available to provide adequate visibility in work areas. It is highly recommended that capacity signs are installed on storage for reference.
A sprinkler system should be installed that corresponds with rack structure. Employees should be informed about the location of fire extinguishers, emergency response equipment, hazardous materials logs, and storage capacity information. Emergency preparedness is equally important to prevention in maintaining a safe workplace.
When installing new pallet racking, verify with the architect that the floor can safely handle proposed weight loads. The floor where storage will be installed needs to be even to support rack structure. Precautions also should be taken if there are risks for seismic or natural disasters in the region that could potentially damage the facility. Ensure columns are properly anchored to concrete slab flooring. Obtain the load capacity of the floor from the building's architect prior to planning warehouse storage and layout. Check local building codes and stay informed about OSHA regulations to prevent violations.
Regularly checking storage is essential to maintaining the safest possible working conditions. Pallet racking should be regularly assessed to ensure it is in proper condition, with no threats to structural integrity. Checking weight capacity is in line with storage guidelines, and installing capacity plates will help to prevent overloading. Check for cracks, dents, bends, and twists that may compromise the functionality of the storage.
Nuts and bolts should be checked to verify they are tightened and that safety locks are functioning. Inspections of pallet racking should involve checking the hardware to ensure it is tightened, looking for missing pieces in hardware, and a visible assessment to check whether racks are level, square, and plumb.
If racks need to be reconfigured or adjusted, always contact your provider to ensure proper set-up and compatibility. Different brands and style of racks are incompatible with each other and could pose a risk to employees if improperly assembled.
Buying Used Rack
Buying used pallet racking can offer savings in equipment cost, an option to recycle products, and can offer a similar quality to new product. However, extra precautions should be taken when assessing the quality of used storage.
If buying used rack, look for signs it has been repaired, such as areas that look painted or evidence of welding. There is no way of knowing whether the individual who repaired the rack is qualified or that it is in acceptable condition to use. Buy used rack only if it is in prime condition and shows no sign of rust, welding, dents, or bends.
Be sure used rack has been stored indoors in a climate-controlled area. Rust can be hidden by paint and other surface coverings, so an experienced eye is needed to determine quality. Make sure you recognize and trust the original manufacturer of the material. Confirm that racking is structurally sound and properly handled during installation and tear down. Rigorous inspection standards will help you avoid purchasing a product that will deteriorate and potentially put employees at risk for injuries.
Forklift Safety
A large portion of all warehouse injuries involve improper use of forklifts or insufficiently trained operators. First and foremost, hiring licensed and experienced forklift operators is essential to minimizing workplace injuries. Selecting storage racks that accommodate forklift traffic can help to facilitate a better working environment for forklift operators.
All aisles in the warehouse should be clear to allow safe forklift traffic and permit sufficient clearance. When forklifts will be used for item retrieval, consider purchasing drive in or drive through pallet rack. This type of rack will allow a forklift to pass under or through the shelves to provide easier access to the items being stored and can maximize floor space.
Drive in and drive through rack optimizes space and creates aisles but is more susceptible to damage from repeated forklift impact. Utilizing aisle protectors, upright protectors, and guardrails will help to reduce destruction and prolong the life of storage equipment. Corner protectors and other safety products are worth purchasing to protect the investment of storage materials and to help preserve the structural integrity of the rack.
When installing new rack or hiring new employees, ensure operators can have supervised practice loading and unloading materials. This will ensure they can confidently maneuver the storage and handle materials without damaging the product.
Ensure that the drivers center their loads when moving items to prevent forklifts from tipping and loads from falling. Make sure drivers are aware of weight limits of the forklifts and never overload them. Drivers should ensure the loads are secured during transport and loaded as close to the mast as possible to maintain balance and security. Establish an ongoing training program for forklift operators within your warehouse. Purchase safety equipment that will protect drivers from falling materials.
Conclusion
By taking the necessary precautions when planning warehouse storage and design, a safe warehouse environment will be created. Creating an ongoing education program within your company will help employees stay informed and keep safety in mind at all times for every situation. Addressing risks and effects associated with specific equipment will help employees avoid common mistakes and improve your rates of injury and lost-time incidents.
This article originally appeared in the August 2011 issue of Occupational Health & Safety.
About the Author
Michelle Coleman is director of Marketing Communications & Online Sales at Storage Solutions (www.storage-solutions.com/), a leading provider of warehouse storage racks. She can be reached by calling the Westfield, Ind.-based company's main line at 866-474-2001. For more material handling industry information, visit www.blog.storage-solutions.com.