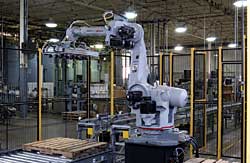
Robot to the Rescue
Robotic palletizing adds flexibility, avoids injuries, and yields floor space savings for this Ohio manufacturer.
- By Tom Simone
- Jul 17, 2007
DAN Schodowski faced a challenge. As
president and CEO of Solon, Ohiobased
JTM Products, Inc.,
Schodowski knew the company was ready
to grow, and making the right investment
choices would be critical. Should the
company buy an existing facility or build
a new one? What new material handling
equipment would be needed to support
its growth?
Perhaps best known as the remaining
piece of the original manufacturer of
Murphy® Oil Soap (sold to the Colgate-
Palmolive Company in 1991), JTM was
founded in 1890 as the Phoenix Oil Company
and today is privately held by grandsons
of the founder, Jeremiah Timothy
Murphy. Its product lines are Murphy’sTM
tire mounting and demounting lubricants
and PhoenixTM pipe joint lubricants used in
the construction of water and sewer lines.
For Schodowski, JTM’s steady performance
of up to $10 million in annual sales
and an estimated 65 percent market share
gave the company financial stability on
which to grow. But in the back of his mind,
Schodowski knew that if he were to expand
JTM, changes in production techniques
would be inevitable for the company, its
employees, and its owners.
“We were
pretty much pigeonholed into an old
building,” he said. “We couldn’t expand.
Even within the building, we could not add
a lot of machinery or equipment. If we
wanted to expand our business, we needed
more room.”
The other challenge was to meet the
material handling demands of JTM’s
product range. While the Murphy’s line primarily
is packaged in 25- and 40-pound
pails, the Phoenix line primarily is packaged
in cases of either quart or gallon containers.
Both sets of products need to be palletized
before shipment, so factory staffers were left
with a lot of slow and heavy lifting.
“When
we decided to move,
we looked at how we
could set up our operations
differently,”
said Schodowski.
“Our layout was fragmented
in the old
building, and we
could not bring in
automated palletizers
or other automated
equipment. We were
faced with having to
keep adding people to
manually load the
product on the pallets
and truck them somewhere
else to have
them shrink-wrapped.
“When we started laying out the new
facility, we knew that we had a lot more
room and that we would be able to run
both lines at the same time. Running
simultaneously in the old plant was a
predicament. To do that, we needed extra
staff on hand, staff that would be there even
if both lines were not running.”
What was needed was a solution that
could handle both product lines and allow
JTM to allocate more space in a new
70,000-square-foot facility. The answer
was an integrated robotic palletizing cell
that could palletize both pails and cases.
Flexibility in Motion
Roughly in the center of JTM’s new factory
floor, surrounded on one side by the processing
and packaging equipment and on
the other by pallets of stacked cases and
pails, the cell is enclosed in a safety cage.
Pails of Murphy’s tire lubricant paste being
filled, capped, and conveyed up to the cell
chug along in the background. With a whir
of motion, the robot rotates to pick up an
empty pallet from its pallet-loading station
and places it in position at the start of an
outfeed pallet conveyor so it can begin palletizing
the pails.
In the project’s original design, 10 pallets
are pre-loaded onto the pallet-loading
station at the start of a sequence and the
robot counts its way down. A modification
will allow the palletizer to sense how many
pallets have been loaded onto the pallet station,
letting the operator load any number
of pallets at the start of a run up to 10, providing
JTM flexibility to do shorter runs
and vary sizes without having to manually
pull pallets out of the cell.
On the infeed side of the cell, accumulation
conveyors take up the pails from the
production conveyors and queue them for
the robot on instruction from the robot’s
control system. Depending on the product
size and stacking pattern used in the particular
palletizing operation, the robot’s
vacuum tool picks up one or three pails at
a time by attaching to their tops, then puts
them down to form the rows and layers of
palletized product. When the pallets are
full, they are shrink-wrapped by an automatic shrink-wrapper and taken by forklift
to inventory on the shop floor. A similar
process occurs for the cases of Phoenix
pipe lubricant.
Safety and Ergonomic Benefits
The robotic palletizer has lived up to the
expectations of Schodowski and Larry
Wilson, JTM’s director of operations.
While JTM uses the system at only 65 percent
of capacity—with the excess capacity
available for continued growth—Wilson
estimated the cell now handles 75 percent of JTM’s annual business volume. That
volume translates into more than 200,000
pails and 150,000 cases per year, with 75
percent of the pails being the 25-pound
size and 75 percent of the cases holding
quart containers. In a typical day of palletizing,
the cell handles 60 pallets of 25-
pound pails, 20 pallets of the 40-pound
pails, 40 pallets of the quart cases, or 25
pallets of the gallon cases. The JTM factory
employs 20 and currently runs one
7.25-hour shift five days a week with a factory
crew of eight but does not palletize
every day.
“In the old facility, without the
robot, I would have had to add two
people to get up to this volume,”
Wilson said.
Beyond adding capacity, the decision
to install a robot was in large part
due to the founding family’s values and
to the safety and ergonomic issues surrounding
a loyal, but aging, factory
crew. The robot has eliminated some
of the crew’s most labor-intensive
work. “It was the right thing to do,”
Wilson said. “The Murphys have a
good relationship with everybody who
works for them, and there’s a mutual
respect between everyone at JTM.
“The ergonomics factored into our decision,”
he added. “We have an older workforce.
Since we’ve moved here, we’ve retired
three people. We had people picking up
1,800 or 1,900 pails a day. That’s a long day.”
“Not everything is based on hard economics,
even though we thought there was
a pretty good payback on the project,”
Schodowski said. “We could be saving
someone’s back, which could be a worker’s
comp claim somewhere down the road.
Those can be very expensive. When you
factor in all of those types of costs, you can
say the payback is definitely worth it.”
When the robot first arrived, Wilson
said, his crew was a bit skeptical and a bit
concerned. But those feelings soon turned
into appreciation as the crew members
realized the benefits. They took it upon
themselves one day to reconfigure one of
their heavily manual secondary lines so it,
too, runs through the robot. “They took
the line, reversed all the conveyors, and ran
it through the palletizer,” he said. “All they
have to do now is pack the boxes, and the
robot gets them all stacked.”
The robotic palletizer is rated for a
lifespan of up to 20 years and has performed
reliably since it was installed.
CHOOSING ROBOTICS FOR AUTOMATED PALLETIZING
Increasing options can blur the decision-making
process when choosing between conventional and
new technologies. While JTM’s decision to go with
a robotic palletizer instead of a conventional palletizer
seemed the logical way to go, the decision
may not be as clear for other companies in a similar
situation.
While high-throughput applications have
demanded a traditional high-speed palletizer in the
past, today’s high-speed applications can be achieved
with either robotic or conventional technology. The
lines between the types of solutions tend to blur even
further when it comes to pattern flexibility. Both
robotic and conventional palletizing solutions can be
configured for virtually any pattern. The trick is determining
which solution is the best fit to meet the other
parameters in an application.
Managers should carefully consider their options
when deciding on the type of system they need to
automate a palletizing operation. Though not a rigid
rule, conventional palletizers are more commonly
used for applications requiring higher speeds or
involving products with reduced packaging. Reduced
packaging is particularly common in today’s highvolume
retail environments and is due in part to the
high cost of corrugate.
Robotic solutions generally fit lower-speed lines
and situations where the palletizer needs to handle
multiple lines simultaneously. Because of their typically
smaller footprint, robotic solutions also are an
option where floor space is at a premium. A variety of
factors, including return on investment, require
careful consideration when deciding which way to go.
If robotics appears to be the answer, the types of
robots and components to be used also will be part of
the decision. Most modern robotic palletizers use
either gantry robots known as “square” robots or
jointed-arm robots known as “round” robots. (They
are nicknamed for their pattern of motion.) Gantry
robots are linear-motion robots, meaning they move
up, down, and across in a work envelope that can be
more than 80 feet long. They are typically built to the
dimensions of a specific project and offer more overall
flexibility, including the capacity to work with a large
number of pick-and-place locations. Jointed-arm
robots are more constrained in the size of their work
envelope but are typically more economical and faster.
In a typical palletizing application, a jointed-arm robot
can build four pallet loads within its work cell.
Another important decision in a robotics application
is which type of end-of-arm tool, or “end-effector,”
to use. While vacuum-type end-effectors have many
uses, they are sometimes not suited for palletizing
operations, particularly for items that are packaged for
product display, such as open-top cases and shrinkwrapped
trays. In these types of situations, side-clamp
or fork-and-clamp tools are a better choice.
Another key is choosing the right partner to build
the solution. Core knowledge of palletizing engineering
is required to adequately spec this kind of
solution, so choose a business partner that has experience
with these types of operations.
Whatever the solution—robotic or conventional—
a trusted partner who can identify and recommend a
solution for a complex production requirement is an
invaluable resource, especially when that partner is
able to integrate a palletizing system into a company’s
wider material handling system and controls. |
This article originally appeared in the July 2007 issue of Occupational Health & Safety.