Job-Made Guardrails: Are They Strong Enough?
The way to be sure that temporary guardrails will do their job when needed and comply with OSHA standards is to use commercially available, laboratory-tested guardrail stanchion bases.
- By C. Ray Asfahl, Erica R. Asfahl
- Mar 01, 2007
A difficult issue faced by nearly every safety coordinator for a
construction site is what to do about temporary guardrail protection.
The temptation is to do the job quickly, get open-sided edges or
platforms closed in as quickly as possible, and caution all personnel
to be extra careful when it is necessary to approach the edge during
the temporary exposure period.
This solution is simply not acceptable to the Occupational Safety and Health Administration, as evidenced by the extremely
high frequency of citations of the standards for guardrails for
construction.The two principal OSHA standards requiring guardrail protection for
construction sites are OSHA standard 29 CFR 1926.501(b)(1) for general
construction sites and standard 29 CFR 1926.501(b)(13) for residential construction sites.
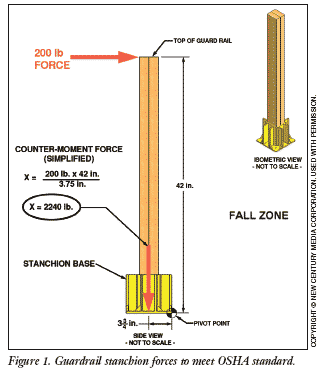
According to our OSHA enforcement files, the following enforcement
statistics apply for these standards from nationwide OSHA statistics
(except Alaska, California, Hawaii, Michigan, Oregon, and Washington,
where state coding systems vary from the federal code) for FY 2006:
501(b)(1):
Total number of alleged violations: 3,223
Total number of alleged serious violations: 2,892
Percent of citations designated as serious: more than 89 percent
Total proposed penalties for this standard: $4,873,200
Average proposed penalty per alleged violation: $1,512
501(b)(13):
Total number of alleged violations: 3,398
Total number of alleged serious violations: 2,997
Percent of citations designated as serious: more than 88 percent
Total proposed penalties for this standard: $4,639,680
Average proposed penalty per alleged violation: $1,365
In the face of OSHA's posture of such stiff enforcement of
violations of the construction guardrails standards, the safety
coordinator often recommends the erection of temporary, job-made
guardrails.
But are job-made guardrails actually safe? They certainly can be.
The primary critical design feature is the base of the stanchions.
OSHA's standard for the engineering of standard guardrails is that the
guardrail must withstand a 200-pound force applied to the top of the
rail in any direction. This is a tall order. The most important
direction, of course, is the horizontal one, the direction that arrests
the fall of a worker who would otherwise go over the edge. Ironically,
this horizontal 200-pound force places a much greater force on the base
of the stanchion, as the diagram in Figure 1 (above) illustrates.
The counter-moment force is applied at the centroid of the base,
which would be appropriate for a symmetrical placement of bolts or lag
screws to hold down the base of the stanchion. Because of the physical
leverage of the 200-pound force at the top of the guardrail, the
counter-moment force must be 42/3.75 = 11.2 times the force at the top
of the guardrail. Thus, the counter-moment force must be at least 11.2
x 200 = 2,240 lbs. This counter-moment can be delivered via the
combined force of the symmetrical bolts or lag screws holding down the
base.
To intuitively picture the large counter-moment required to balance
the 200-pound force at the top of the rail, imagine the stanchion as
the handle of a huge hammer being used to remove an enormous nail at
floor level. The tremendous moment of force produced by applying a
200-pound force to the end of such a huge hammer would be very
effective in prying out a nail at floor level. But that is exactly what
a guardrail stanchion must NOT do! The fasteners at the bottom of the stanchion must hold, or the guardrail will fail!
False Sense of Security
The OSHA minimum specification of 200 pounds applied at the top of
the rail is a reasonable one. Even though leaning on a guardrail
usually does not generate a 200-pound load, it is reasonable to imagine
an occasional shock load of 200 pounds. Anyone who has tried to handle
a sheet of 4X8 plywood in a brisk breeze realizes the potential of the
plywood getting caught by the wind and forcing the worker carrying it
to slam against a guardrail. Of course, the reasonable strategy in such
an emergency is to let the plywood fly off the platform, but there is
strong motivation not to let that happen. The worker in such an
emergency realizes that a flying sheet of plywood can be a serious
hazard to workers at lower levels, and he will try to hold onto the
flying sheet of plywood if at all possible. He needs to be able to
assume that the guardrail is sturdy and will arrest his fall if
necessary, which brings us to a second reason to build sturdy
guardrails: false sense of security.
A guardrail can do more harm than good if it is unexpectedly flimsy,
generating a false sense of security. Absence of a guardrail quite
naturally motivates workers to be careful and respect the edge; at
least, it should. But the presence of a seemingly reliable
guardrail will give the worker a degree of complacency about the edge
of the floor or platform. If the guardrail is weak or fails when a
worker needs it, a terrible accident will likely ensue that might never
have happened, even with no guardrail present.
Besides the integrity of the lag screws or bolts holding the base of
the stanchion, the base itself and its bottom plate flanges must be
able to withstand the enormous 2,240-pound force applied by a top load
of 200 pounds. The way to be sure of the entire stanchion assembly is
to subject the stanchion to an engineering laboratory test with the
stanchion mounted in the manner it will be used on the job site. There
is no other way to be sure.
There simply is no substitute for providing guardrails in accordance
with OSHA requirements and using standard, laboratory-tested bases for
the guardrail stanchions. The way to be sure that temporary guardrails
will do their job when needed and comply with OSHA standards is
to use commercially available, laboratory-tested guardrail stanchion
bases. Another suggestion: Keep a copy of the engineering laboratory
test record in case the OSHA compliance officer comes knocking. A
reputable supplier of guardrail stanchion bases will be happy to supply
customers with a certified engineering laboratory test report to verify
that the base meets OSHA minimums.
This article appeared in the March 2007 issue of Occupational Health & Safety.
For information on nationwide OSHA citation statistics and average fines for various OSHA standards, contact New Century Media at 800-913-1133 or www.oshastandardsdigest.com.
This article originally appeared in the March 2007 issue of Occupational Health & Safety.