Pouring It On
Despite hellish conditions, Jencast's safety numbers are heavenly. How?
THE last time Jencast Inc. experienced a lost-time
accident, Ken Starr's "Report" was a work in progress, Viagra was on the verge of getting FDA approval, and fears of the so-called Y2K bug were starting to gain national attention. The Spice Girls were still on the charts.
On Feb. 26, 2005, Jencast, an iron foundry in South Coffeyville, Okla., celebrated its seventh straight no-lost-time year. That milestone was overshadowed two months later when the ironworks plant raised the safety bar even higher by reaching one million man-hours worked without a lost-time occurrence. The hours, days, and months are, as of this writing, still accruing. It is an ongoing accomplishment that would be notable under any circumstances, but considering that the site's internal milieu resembles an artist's best rendering of the bowels of hell, it's a staggering achievement.
A manufacturing division of Coffeyville, Kan.-based Jensen International Inc., the Jencast foundry has the capacity to melt 100 tons of iron per day using two 9-ton coreless induction furnaces, two kinds of sand, and various chemical mixes to pour up to 40-grade gray, ductile, and compacted-graphite iron. With about 100 employees, the Jensen family-owned and -operated plant specializes in 25- to 1,500-pound castings in quantities from 25 to 5,000. Given the work's inherent hazards, safety is, by necessity, not only a top priority for the company, but, according to Alvie Hornburger, Jensen's corporate environmental and safety manager, it's in the very furnace-blasted air employees breathe.
"Foundry work is really, really dangerous," Hornburger said. "You're dealing with temperatures of over 3,000 degrees with the furnaces. There are a lot of foreign bodies in eyes from the sand and dust and the grinding the workers do. There's a lot of heavy equipment, a lot of hoisting cranes, forklifts moving material around in there. It's just dark and hot, so we have to worry about heat stress, potential burns from the molten metal that can splash up on people, the eye injuries, the lacerations, strains, trips and falls. . . . There are a lot of different hazards."
Against All Odds
With such a preponderance of potential perils, injuries and illnesses can and do occur at the plant, Hornburger said, but not nearly on the scale they once did and not--since Feb. 27, 1998--with the severity to cause an employee to miss the next day's work. Avoiding injuries that are of lost-time caliber is, in a sense, "playing against the odds," he said, but that's only if you believe a certain number of workplace accidents are inevitable. If, he added, you approach safety believing all injuries are preventable, as Jencast does, with employees and managers alike looking for ways to prevent any kind of accident or dangerous situation from occurring, then suddenly the odds are reversed.
This was not always Jencast's approach. As recently as a decade ago, the foundry floor was "like a battleground out there . . . like a small war, where people were getting hurt all the time," said Hornburger, who began working for the company in mid-January 2005. He said his predecessor, Jensen Purchasing Manager Roger Hensley, was instrumental in changing the company's safety culture and turning around the results. Hensley downplays his role but does say that, prior to being given safety management duties in addition to his job in purchasing, the plant's focus was more on production than safety and that, consequently, worker injuries and lost-time cases were "out of control." The NCCI-regulated worker's compensation experience modifier (WCEM) back then was, he added, "horrendous."
"There just wasn't anybody there watching or paying attention to detail and taking care of things when they did happen," Hensley said. "They brought me in there, and I did that. I didn't do anything amazing--just made everybody aware of their actions and that they were responsible for what they did."
The effects were dramatic. Since 1998, Jencast's WCEM has remained consistently below the national average of 1.0 and has not been higher than 0.68. For 2004, it was 0.67.
Ironing Out an Incentives Program
One of the ways Hensley went about making workers aware of their actions was devising an in-house incentives program. Working with a limited budget, Hensley based the program by departments within the facility and began doling out awards to any group that went a specified time without having an OSHA recordable.
"We did them on a monthly basis for a while," he said, "but then the workers got to doing so well, we had to back off to doing them quarterly." The plan, he said, was simple: "Anyone in a group who had a claim for whatever the timeframe was, then that group was off the list to receive the award. It got to where it was kind of personal to everybody, and it did help."
The quarterly awards continue and are supplemented by year-end-improvement awards per department, as well as periodic companywide catered meals, as when the million man-hour milestone was reached, and any time the company achieves another no-lost-time year, which has become an annual tradition.
Hornburger, whose experience includes stints as EHS manager at companies both larger and smaller than Jensen, said he had never previously worked anywhere that had an incentives program in place. His immediate impression upon arrival at Jensen, he said, was of an overwhelming sense of family and of the teamwork its program had clearly inspired. "Because it's department-based, the program pushes more of the people in a given department to kind of watch over each other," he said. "It pushes them to be more observant, more careful. If somebody's not wearing his safety glasses or something, then others around him are more apt to speak up and say something. It definitely fosters a team approach. You get a sense of everyone working together on it."
Fuel for Thought
While the company budgets for the program, the funds set aside for the actual awards are limited; however, the imagination behind them is not, Hornburger said. The product of brainstorming sessions conducted in monthly safety meetings attended by employees from each department, the awards tend to be personal, useful, and therefore atypical, he said.
For example, because many employees have to drive 40 to 50 miles or more to get to work, the award for one recent work quarter was gas cards. Because employees frequently visit a local farm and home store as well as a nearby giant discount retailer, gift certificates to both places have been awarded. Other prizes have included screwdriver sets, wrench sets, T-shirts, leather gloves, and various other items of personal protective equipment.
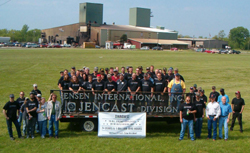
"We try to make the awards a group decision, with the employees themselves having a big voice in it," Hornburger said. "We try to make them useful and go for things that mean more, staying away from what I think of as throwaway stuff like keychains and the little squeeze balls for stress. You know, those aren't things people really care for. But when you award them something like the store gift cards or the fuel card, those are things they need or are going to use themselves anyway. The T-shirts are something they can wear to work to save their good clothes from getting messed up. And the tool sets: I think every time they use one of the screwdrivers, they'll remember where it came from, and in general it will just mean more to them than the gimmicky things like the company-name-embossed pens."
Hornburger and Hensley agreed that, as popular and successful as the incentives program continues to be, its purpose is primarily to provide a relatively inexpensive way of communicating thanks to Jencast workers. After all, Hornburger said, "The real incentive is not getting hurt, not going to the doctor. No one wants that." He added that while the awards program "helps focus the safety more and gives something back to the employees," it is merely one facet of an overall culture of safety the company espouses.
"Safety is a behavior," Hornburger said. "It's a mindset, and it takes a long time to change that. The awards help drive home the message that we want our employees to go home the same way they came to work."
Seven-Year Stretch
After seven-plus years without a lost-time accident, the longevity of the achievement has created a momentum among employees that has become an incentive in itself. No one wants to be the one who has the accident that breaks the record. That being said, Hensley added, "We have a completely open-door policy here, and everybody is thinking safety at all times. If there's a problem, all anyone has to do is tell somebody--anybody. It's encouraged, and there's no reprimand for anything like that."
Hensley said Jencast benefits from a solid, older employee base with members of some families having worked there for generations. Not only are they the company's best teachers, he said, but they well remember the "not-so-good old days" and realize how far the company has come regarding workplace safety.
Even before Hensley began Jencast's in-house incentives program, he helped institute a light-duty/back-to-work system in which workers who suffer slight injuries can return to the job and temporarily fulfill alternate duties until they are back to full strength. "It allows them to still contribute to production and not stay home eating bon-bons and watching the soap operas," Hensley said. "Meanwhile, having them back on the job, we aren't losing any time, and they're being responsible for maintaining their own restrictions. . . . That has helped a bunch and has been as instrumental in the company turnaround as the awards program."
Outside of the light-duty and incentives programs, the company has adopted other measures designed to keep safety top-of-mind for all employees. In addition to conducting the monthly safety meetings, Hornburger writes a monthly newsletter that covers safety topics and is included with each paycheck. Upper management is proactive in injury prevention efforts, and when an accident does occur, management is very involved with "figuring out what happened and what they can do to keep it from happening again," Hornburger said. The company also has a strongly safety-focused orientation program for new hires and temporary workers, as well as ongoing training for the long-term employees.
Modern Alchemy
On May 26, 2005, Jencast turned its ironworks to gold in the form of the Oklahoma Governor's Award of Excellence for Safety, an award the foundry has received twice before. This year, the site was chosen from a field of 24 nominees in the mid-sized business group.
Hornburger said that, as with all of the other achievements the company has seen in 2005, this latest accolade is a direct result of the dedication and teamwork of Jencast's employees. "It's been a busy year for the company," he said. Make that seven years--and counting.
This article appeared in the September 2005 issue of Occupational Health & Safety.
This article originally appeared in the September 2005 issue of Occupational Health & Safety.