Operator Digital Twins: Doubling Up to Boost Safety in the Oil and Gas Space
We are living in the era of intelligence.
The fourth industrial revolution is well underway. Following in the footsteps of mechanization, the assembly line and the IT revolution, digital transformation including Cyber-Physical Systems, IoT Networks and Digital Twins are driving this latest installment of the industrial revolution. In fact, by the end of 2019, digital transformation spending will reach $1.7 trillion worldwide – with investments in everything from robotics, drones and connected sensors to virtual and augmented reality, big data and analytics, wearables, and apps.
Safety is driving change in the oil and gas workplace.
Many of these technologies – especially wearables – are helping us create safer work environments by creating awareness of operator location in context, tracking exposure to hazardous environments, removing operator fatigue as an incident root case, and getting real-time critical information to the plant floor when it matters most.
Say hello to the Operator Digital Twin.
The Digital Twin concept has been talked about a lot in relation to physical assets. So how might we exponentially improve worker safety by applying digital twin concepts to our human assets?
Here's how it works. Your employee is outfitted with wearable technologies . . . smart electronic devices incorporated into clothing or worn on the body as implants or accessories, such as:
- Smart watch
- Wearable holographic computers or Smart Heads-up Display (HUD)
- Bluetooth Low Energy (BLE) Tags
- Smart workwear (biometric vests, hard hats, boots)
- Microchips
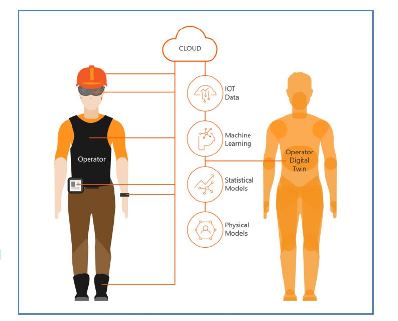
Via the cloud and utilizing the intelligent edge, IoT data is collected to inform machine learning, statistical models and physical models – thereby creating the virtual doppelgänger – the Operator Digital Twin.
These data are used to model the human twin's work habits, provide fatigue modeling, and identify hazards in the environment. For example:
- Measure trips, falls, step frequency, and acceleration, leveraging the data to identify previously unknown hazards and the person's exposure to them.
- Monitor location (GPS, RFID) and thereby be able to quickly assess proximity to potential hazards and incidents and advise the affected personnel in real time.
- Alert to unsafe environment conditions.
- Monitor various potential exposures such as weights being lifted, Fatigue prediction exposures, exposure to radiation, then generate immediate mitigation actions.
Resource extraction company deploys Operator Digital Twin for safer operations.
A case in point – to reduce safety incidents, a U.S.-based company employed Operator Digital Twins to track key biometrics data and used machine learning (ML) to build twin models specifically for fatigue prediction. This operation runs 24/7 and includes high-risk elements such as large earth-moving equipment, ledges without safety rails, and other factors that contribute to incidents resulting in serious injury or even death.
The outcome? The company runs a fatigue prediction score and has activated early fatigue alerting and equipment emergency shutdown in critical fatigue situations.
Opportunity is not without obstacles.
While the Operator Digital Twin model opens up a world of possibilities for the oil and gas industry, there are a few challenges to consider:
- Hardware – Wearables still need to improve in the areas of connectivity, power consumption, heat and emissions, ergonomics, functionality, durability and safety.
- Privacy – Due to the nature of the information collected, anonymizing the retained data is a must and GDPR creates additional challenges in that regard.
- Compliance – Wearables that aren't accepted by employees into the corporate culture tend to be damaged, forgotten, or otherwise neglected. In a recent personnel tracking project, Avanade found a 70 percent compliance rate – it needs to be higher.
- Cultural transformation – The move toward Operation Digital Twins requires a massive change in the way people think and work. Neglecting cultural change management will only lead to low compliance rates and ultimately reduce the ROI from both safety and financial standpoints.
The time is now to start thinking about how Operator Digital Twins can help improve workplace safety, security, and productivity at your organization.
Avanade Director and Southwest Innovation Lead Thor Schueler is a results-driven leader, engaging presenter, strategist, and subject matter expert in the digital innovation ecosystem space. His expertise spans more than 25 years working with transformative technologies, including SaaS/cloud, application development, Enterprise Content Management, and the Microsoft stack, including SharePoint, Office 365 and Azure applications. He joined Avanade in 2017, where he plays a key role as Innovation Lead for the Southwest region, working with clients in oil and gas, construction, and other industries to drive innovation with game-changing digital solutions. His earlier career includes customer-facing and technical positions at global and start-up consulting firms. He earned a Master of Science, Electrical Engineering and Information Technology degree from Dresden University of Technology in Dresden, Germany, and holds numerous leadership, project management, software development and technical designations.
Posted on Mar 26, 2019