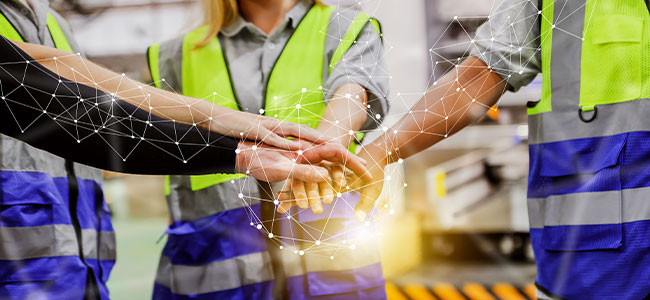
Building a Successful Safety Culture
Many leaders understand what a safe working environment looks like but might not have the tools to creat a productive safety culture.
- By Michael Farlow
- Apr 04, 2024
A productive safety culture is an elusive but vital component of successful operations. Many leaders understand what a safe working environment looks like but might not have the tools to set that vision in place at every level of the organization.
In more than 30 years of overseeing safety operations, I’ve worked with organizations at all levels to align EHS strategies with business goals and slowly build out a culture of safety. Across industries from services to manufacturing, I’ve seen the positive transformation that comes from putting an emphasis on safety as well as the hurdles along the way. Here are the best practices leaders can take in promoting and strengthening a facility’s safety culture:
- Invite feedback from all levels. Decentralizing the power to create safety systems is a vital part of making sure no part of an organization is left out of the conversation. Guidance on safety is expected from top-level management, but at scale, it works best when all employees feel ownership in their safety. Safety protocols affect employees at all levels. So when everyone is empowered to voice their concerns, they’ll often find creative solutions that top-level leaders might miss.
- Communicate honestly about safety concerns. To give everyone a say in safety operations, it’s vital to understand how different teams within an organization communicate. It’s the leader’s responsibility to share and enforce safety improvements in a way that’s meaningful to the team they’re working with at that moment. Discussions around safety should be two-sided, empathetic and occur regularly. In my work with clients, I’ve seen regularly scheduled safety conversations help create a noticeable reduction in accidents. Working to normalize these discussions takes the corniness out of the conversation and shows employees they’re invested in their safety and productivity.
- Create safety systems. As Atomic Habits author James Clear said, “You don’t rise to the level of your goals, you fall to the level of your systems.” Even the most well-intentioned safety practices will fall through the cracks in peak demand when there aren’t regular systems in place to back them up. Systems, routines and repeated behaviors turn safety initiatives into habits. Many of the facilities I’ve worked with have a system of backups to allow employees to safely complete their tasks without having to actively choose that safer option. Once they become no-brainers, some of the decision fatigue facing the team will be relieved, making the safest option the automatic one.
- Choose to support instead of punish. Safety leaders aren’t always the most welcome faces in facilities. I don’t always get the warmest welcome when I enter a new facility, since people associate my position less as enforcement and more as punishment. We often get a bad reputation for looking for reasons people are falling short. But this isn’t what we’re here for. Driving safety changes in an organization leads to more engagement and positive reactions, especially when leaders treat their role as a support to theirs. Though they might encounter some pushback along the way, safety measures that don’t fit the risk can create an excess burden on workers and slow productivity. Be mindful of the small trends, but never lose sight of the big picture when balancing risk reduction with the current practices employees are used to.
Creating a true culture of safety is a long process that often includes unlearning certain habits to make way for more positive practices. Take the time to transition to new ideas, and remember to hear out everyone impacted by new policies. A little empathetic communication and a lot of strategic thinking will inevitably reduce the risk of injury, boost productivity and create plenty of happy employees, thereby strengthening the safety culture in the workplace.
About the Author
Michael Farlow is an accomplished Environmental, Safety and Health Professional with 30+ years of success aligning EHS strategies with business goals to establish industry-leading results. Michael is currently the Director of Environmental Health & Safety at Concentric, the first national industrial power services organization delivering uninterrupted, sustainable facility power and equipment electrification. Prior to his time at Concentric, he served as a health and safety leader at ONE Gas, Baker Hughes, and Norris. Michael has also mentored future EHS professionals through various organizations and served as a 3rd Class Petty Officer in the U.S. Navy.