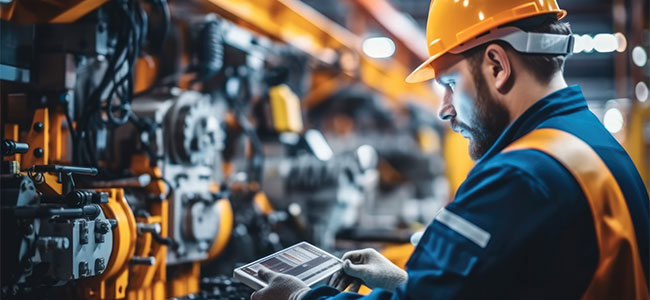
A Comprehensive Exploration of the Role Safety Plays in Manufacturing and Industrial Organizations
Despite advancements, workplace safety remains secondary in many firms, highlighting the need for a cultural shift and dedicated roles to prioritize it based on historical and research insights.
- By Beemal Vasani
- Mar 25, 2024
The realm of workplace safety has undergone significant transformations since governments worldwide began taking worker and occupational health seriously in the 1970s. Despite these advancements, many manufacturing and industrial organizations still relegate safety to a secondary status, often adding it as an afterthought to a manager's list of responsibilities. In this comprehensive exploration, let’s delve into the historical context and current practices.
This will include emphasizing a cultural shift towards prioritizing safety within organizations, highlighting the crucial necessity for a dedicated safety role from the upper echelons to the grassroots level of organizations. Drawing on third-party research and insights from workplace safety reports, the aim is to spotlight the critical importance of making safety a proactive and integral part of organizational processes.
Historical Perspective
To understand the contemporary challenges surrounding workplace safety, it's essential to acknowledge the historical context. Governments around the world only began prioritizing worker and occupational health in the 1970s, marking a significant shift in attitudes towards employee welfare. Examining safety's journey, it becomes evident that its position within organizations has not evolved at the same pace as technological and industrial advancements.
At the onset of the safety revolution, the focus was primarily on complying with basic safety regulations. Fast forward to the present, and safety has become a multifaceted concept, encompassing not only compliance but also a proactive approach to prevent accidents and injuries. However, the implementation of safety measures is often an afterthought in the innovation and implementation process, leading to potentially avoidable incidents and injuries.
Drawing from third-party research, workplace safety reports illustrate the consequences of neglecting safety measures and highlight the correlation between proactive safety processes and accident prevention. Safety, despite its undeniable importance, still struggles to secure a primary seat at the corporate table.
Flipping the Safety Paradigm
Traditionally, safety considerations come into play towards the end of the innovation and implementation processes. This reactive approach leaves organizations vulnerable to inherent risks that could have been mitigated with a proactive stance. By integrating safety considerations at the onset of discussions, companies can ensure that their processes are not only innovative and efficient but also safe from the outset.
This shift in approach requires a cultural change within organizations. Safety should not be viewed as an additional step but as an integral aspect of business operations. Workplace safety reports emphasize the need for a cultural transformation, where safety is considered a priority at every stage of the decision-making process. The proactive integration of safety practices leads to a reduction in accidents and injuries, contributing to a safer and more productive workplace.
Higher Education's Role
Recognizing the growing importance of safety in the workplace, higher education institutions are expanding safety programs to meet the demand for qualified safety professionals. Colleges and universities, including Murray State University, Strayer University, Fordham University and the University of Miami, offer specialized courses in safety and occupational health. This influx of educated safety professionals represents a new generation equipped with the knowledge and skills to drive change within the manufacturing and industrial sectors.
These programs not only educate individuals on safety regulations but also instill a proactive mindset, emphasizing the importance of preventing accidents rather than merely responding to them. The graduates from these programs play a pivotal role in reshaping safety practices within organizations, contributing to the establishment of a safety-conscious culture from the ground up.
Introducing a 'Safety Champion' in the Workplace
While some large corporations have the luxury of chief safety officers, not every company can afford such a dedicated role. However, every organization can take steps to ensure that safety remains a priority at all levels. This includes the establishment of a safety committee composed of key ambassadors within the organization.
These safety champions can play a crucial role in disseminating regular communications on various health and safety topics. This decentralized approach ensures that safety information reaches every corner of the organization, fostering awareness and accountability. By appointing safety ambassadors, organizations create a network of individuals who actively contribute to promoting a culture of safety, even in the absence of a dedicated safety officer.
Leadership's Evolution in Safety
The concept of safety within manufacturing and industrial workplaces has evolved significantly from a leadership standpoint. Initially seen as a mere compliance requirement, safety has now emerged as a strategic imperative for organizational success. However, there is still a considerable gap between acknowledging the importance of safety and implementing effective safety practices.
Leaders must reevaluate how safety is currently handled within their organizations. This involves scrutinizing existing processes, identifying potential hazards and implementing tangible solutions to create safer job sites. Workplace safety reports and third-party research underscore the importance of recognizing and mitigating factors such as repetitive or sustained motion that can lead to injuries.
To take safety more seriously, leaders must foster a cultural shift within their organizations. Safety should not be focused on compliance but as a catalyst for efficiency and employee well-being. Implementing safety measures from the outset can prevent not only accidents but also long-term health issues, creating a more sustainable and secure work environment.
Creating a Safety Culture
The transformation of safety from a reactive to a proactive approach necessitates a cultural change within organizations. Safety should be an integral part of daily operations, discussions and strategic planning, rather than an afterthought. This cultural shift requires commitment from leadership, active participation from employees and the integration of safety into every aspect of the business.
The workplace safety report data emphasizes the significance of embedding safety practices into the organizational culture. Metrics measuring safety and performance can be instrumental in setting tangible goals for improvement. Wearable technology provides a tangible solution by offering insights into how movements affect workers. This technology generates concrete data metrics on issues like musculoskeletal disorders (MSD), enabling proactive intervention before health concerns escalate.
Towards a Secure Future
Understanding the crucial role of safety within manufacturing and industrial organizations, certain limitations may hinder the establishment of a dedicated safety position. Thus, it becomes essential to prioritize a top-down approach to safety, ensuring that the responsibility for cultivating a safety culture starts from leadership and extends throughout the organization. The historical context, current challenges and potential solutions outlined in this comprehensive exploration highlight the urgency of making safety a proactive and integral part of organizational processes.
Moving forward, safety should hold a prominent seat at the corporate table, guiding strategic planning and fostering a safer, healthier and more productive working environment. The prevention of accidents through strategic planning can save companies time and money while simultaneously creating a better working environment for employees. Metrics measuring safety and performance should be used to set tangible goals. Wearable technology provides an avenue for uncovering concrete insights about the risk profile of workers, allowing the prevention of injuries before they occur.
The road ahead involves not just acknowledging the importance of safety but actively integrating it into conversations surrounding operations, innovation and decision-making. Safety should be an inherent part of the organizational DNA, contributing to a workplace culture where the well-being of employees is prioritized at every step. In this way, safety becomes not just a compliance requirement but a strategic advantage that ensures the long-term success and sustainability of manufacturing and industrial organizations.
This article originally appeared in the June 2024 issue of Occupational Health & Safety.