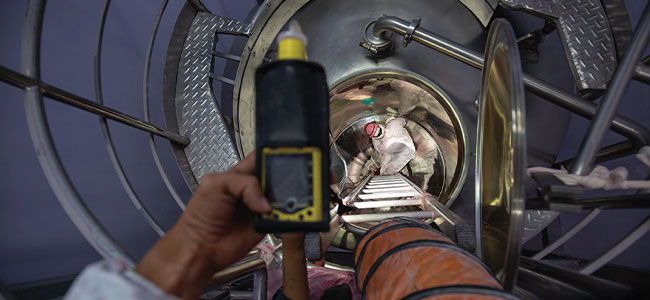
5 Ways Connected Gas Detection Devices Can Boost Your Organization’s Productivity
Here’s why safer work doesn’t have to mean slower work.
- By Anne Osbourn
- Mar 01, 2024
Does safer work mean slower work? It certainly does not have to. PPE and gas detection solutions can help enhance worker safety, visibility and accountability while also driving productivity. These measures could be especially impactful when you consider that workplace injuries in 2021 caused U.S. companies to lose an estimated nearly $170 billion in wages, productivity, medical expenses and administrative expenses.
With the benefits of connected work for your gas detection program, you can help enhance safety as well as productivity. Connected work programs can allow you and your team to make more efficient and productive use of your time and resources.
Put simply, the term “connected” not only means a connected device — one that comes with cutting-edge cellular connectivity through leading national networks — but also a comprehensive solution inclusive of hardware and software. This type of solution can provide the real-time data to help gather insights in order to help drive adaptable, proactive safety programs.
By itself, a properly calibrated and bump-tested gas detector is a powerful personal protective device, for example, for the individuals on-site and to provide the organization with historical data for consideration.
But a connected work platform can take a gas detection program to the next level.
A connected work platform combines real-time data, connected PPE/gas detection wearables and advanced software solutions to help provide more visibility across these areas of concern:
• Workers
• Worksites
• Workflows
In fact, connectivity enables the kind of visibility that can further enhance a safety program and improve safety outcomes. Connected gas detection programs provide powerful data which can be harnessed to help improve operational efficiency.
Even better, a strategic connected worker-worksite-workflow platform helps take your gas detection program a step further in terms of safety and productivity. Plus, it sets you up for a scalable and adaptable safety program for today — and tomorrow.
Here are five ways in which connectivity can help make your organization more productive.
1. Data and Insights
Get deeper insights into your operation with the generation of critical data points about off-site workers and your fleet of detectors. You can help keep lone workers safe with data including gas exposure alerts, man-down alarms, panic button presses and device concern warnings so that you can act as swiftly as possible for the circumstances. Access to data also enables you to optimize deployment of your assets and to identify areas for safety training, common trends across events, and opportunities for efficiencies and possible cost reduction. Improved practices also help reduce safety incidents, along with their related downtime and productivity losses.
2. Incident Analysis
A connected program enables access to events in real time including emergencies, evacuations, warnings and alarms. You can manage events remotely and digitally handle post-event documentation, helping make the process more efficient. Information on important factors involved in an incident can be easily gathered and correlated from all parts of the connected system, which helps in identifying and understanding root causes. Systematic analysis forms a sound basis for making process changes to help reduce future risks.
3. Process Automation
Processes such as manual preparation of reports can often be time-consuming and cumbersome, as well as potentially prone to errors. With a connected gas detection program, reporting and documentation are digital and automated, helping to streamline processes and drive accuracy and efficiency. Managers can produce a usage report for a device in minutes, leaving your team with more time to focus on putting data insights into practice and optimizing productivity. Device check-in and check-out can be automated for daily, project-specific and long-term work, and to help improve inventory management and the return of devices following each shift.
4. Asset Management and Maintenance
A connected work program makes devices and their associated data visible, including details such as when its next service is needed. Maintenance scheduling software tools can automatically help you to keep your fleet of devices compliant with minimal downtime so that workers can focus more on work. Digital device assignment with RFID tagging helps simplify the process for checking devices in and out each day and helps make individual workers accountable for assigned devices. With over-the-air updates, you can even remotely adjust the settings of individual units, groups of devices or the entire fleet.
5. Compliance
Manual auditing of device compliance in a large fleet is another process that swallows up time and may be susceptible to errors. With connected gas detection devices, it can become quick and easy. For instance, automation of checks and compliance test procedures helps prevent non-compliant units from being assigned for use. Connected devices recognize when calibration and bump tests are due and run the appropriate test automatically when next docked.
Connected programs help remove the administrative burdens and time obstacles associated with the traditional ways of keeping a gas detection fleet compliant by predicting when a sensor will come to the end of its useful life or when calibration gas is nearly empty based on actual use data. Out in the field, automated lockouts can prohibit the use of devices that have become non-compliant. You can see certain compliance status for all devices, wherever they are. Again, these time savings help enable workers to concentrate on continuous improvement and growth in productivity.
Connected gas detection programs can help build connections between workers, worksites and workflows, providing actionable data that helps safety managers create safer, more efficient and more productive work environments. Implementing a connected gas detection program does not happen overnight. One possible next step is to take a deeper dive into understanding where you are on your connected journey and identifying the right partner to help support the organization’s safety, compliance and productivity goals.
This article originally appeared in the February/March 2024 issue of Occupational Health & Safety.