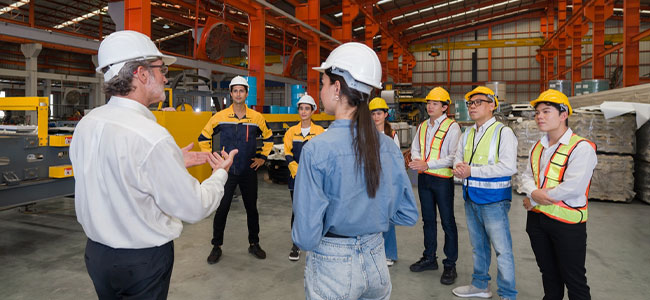
The Secret to Fortune 500 Companies' Success Lies in a Proactive Safety Culture
As demonstrated by successful organizations across the globe, a safe work culture benefits every area of a business.
- By Aron Yellott
- Dec 08, 2023
Fortune 500 companies share a crucial trait: an unwavering commitment to safety.
Consider the story of Alcoa. In a state of decline due to years of inefficient processes and several failed product lines, the manufacturer brought in Paul O’Neill, a leader who they hoped would transform the aluminum manufacturing corporation. During his 13-year tenure as chairman and CEO, O'Neill championed safety above all else, implementing robust processes and establishing a culture of collective accountability.
O'Neill's focus on safety paid off. Alcoa's lost workday rate due to accidents fell by 80 percent, its market value increased from $3 billion to $27 billion, and its net income increased from $200 million to $1.4 billion.
Alcoa’s story is a testament to the impact that prioritizing safety can have on both human well-being and corporate prosperity. This trend reverberates throughout successful Fortune 500 companies, including Bayer’s focus on employee safety training programs and Schneider Electric’s dedication to empowering employees through safety ownership.
And the trend isn’t just anecdotal. Research confirms that prioritizing proactive safety solutions improves productivity and company culture, which in turn benefits employee retention, organizational profitability and OSHA compliance.
Where Reactive Safety Programs Fall Short
Over the past decade, several prominent organizations have sought such expertise in transforming their safety cultures and improving the organizational environment, health, safety and sustainability (EHS&S) standards. And the most common barriers to proactive safety cultures are twofold.
- Lack of collective accountability: Employees often believe that reporting safety issues is someone else's responsibility, or even worse, they fear they will get in trouble for reporting concerns or incidents. As a result, many employees fail to report safety incidents or potential hazards.
- Inefficient processes: In many cases, organizations rely on manual processes and antiquated tracking methods, which are slow, inefficient and error-prone. The outcome is that employees may not know how to report safety incidents or even what incidents need to be reported. And when a report is made, inefficient processes prevent quick responses.
To create a proactive safety culture, organizations need to address these two barriers. Let’s imagine a scenario in which safety becomes a collective obligation, and employees possess the tools to address incidents effectively:
- In a reactive culture, a crack in the ceiling leads to a wet factory floor. Multiple employees notice the wet floor and continue working in the area; eventually, an employee suffers from a slip and fall incident and fractures their knee. Employees did not know how to report hazardous conditions or why reporting was even necessary. Therefore, both the hazard and incident were never reported. This results in a cascade of issues which may include insufficient employee medical care, inadequate medical compensation, a safety lawsuit, fines and operational disruptions. In this scenario, the ceiling crack continues to be ignored due to the lack of safety ownership and collective responsibility.
- In a proactive culture, the employee notices water on the floor and immediately reports the hazard. All employees are aware of how to make a report and can do so using their mobile devices. This action triggers an immediate response from management, ensuring the appropriate mitigation measures are taken, the water is cleaned up and the roof is fixed. The result: An employee fall was prevented.
In an active safety culture, communication thrives, compliance is assured and hazards are swiftly neutralized. While establishing a proactive safety culture can be challenging, it ultimately reduces accidents and injuries, saves on costs, improves employee morale and reduces legal liability.
How to Create Safety Programs that Rival Fortune 500 Companies
So, how can organizations move from reactive to proactive safety programs? The most successful and profitable businesses, including Fortune 500 companies, have these key characteristics embedded in their culture and processes:
- Easy pathways to reporting:
To encourage employees to take part in safety reporting, it’s vital to make the reporting process simple, accessible and intuitive. This means removing any barriers that might prevent employees from reporting an incident, such as requiring them to use a desktop computer or report a hazard in person. Mobile apps are a great way to empower employees in the field to report hazards quickly and easily.
For example, Co-op, one of the world’s largest consumer cooperatives, conducted a major overhaul of its safety infrastructure, adopting a new software that made reporting accessible to all employees and contractors. Over the course of a year and a half, more than 1 million events were reported, resulting in a 26 percent reduction in high-severity incidents, a 53 percent reduction in physical assaults and an improved incident-to-near-miss ratio.
When barriers to communication are removed and avenues for reporting are easily accessible, the workforce becomes a safety net, identifying threats before they escalate.
Employees who see positive outcomes from reported hazards are more likely to submit reports in the future. This can help create a safer work environment for everyone, nurturing a culture of vigilance and continuous improvement.
In the Co-op example, simply adopting a better reporting system wouldn’t have resulted in change, unless employees saw that their reports were taken seriously. When employees observe the positive change that comes from submitting reports, they are more likely to repeat the behavior going forward.
When an employee reports an unsafe condition, hazard or incident, management should respond promptly and efficiently. This includes thanking the employee, encouraging them to get involved in any action taken, mitigating the hazard and celebrating their example. Knowing their efforts have been seen, heard and ultimately have made a difference will encourage employees to continue reporting safety concerns or hazards in the future.
Ongoing training sets the tone for empowered, knowledgeable employees. It shows employees that safety is vital to the organization and that everyone has a role to play in maintaining a culture of safety. When everyone in the organization has a collective understanding of safety, it creates a strong front against accidents and injuries.
Training should cover safety procedures and practices, what to do in the event of a hazardous situation and how the reporting process works. These resources must be easily accessible to workers in the field if they need a refresher on a policy or procedure so that hazards can be addressed in real time.
A great way to elevate safety in the workplace is by hosting an annual Safety Week. Programming should remind employees of the importance of safety, introduce new procedures, host safety challenges and provide awards to employees who have demonstrated outstanding safety practices.
- Align procedures and practices:
Safety procedures are often written in a vacuum, removed from the realities that workers face in the field. This creates a disconnect between what workers are supposed to do and what they actually do, leading to accidents.
To bridge the gap between procedure and practice, organizations need to receive feedback from workers about the effectiveness of their safety procedures and processes and then make updates based on this feedback. Consider surveying new employees as part of the onboarding process to understand what’s confusing or unclear to newcomers and to determine if they can identify gaps that existing employees have grown accustomed to.
Given that only 40 percent of businesses have a well-defined plan for safety performance improvement and just 36 percent use learnings to prevent future incidents, it’s important to ensure that this commitment is ongoing and not a one-time effort. When you encounter a hazard or incident, take it as a learning opportunity and share takeaways throughout the organization to safeguard other areas of the company against similar issues. Learning from incidents, sharing lessons and modifying practices and procedures are essential to the continued vitality of the safety program. Remember: safety is an evolving program that changes with each new hazard.
Move the Needle on Safety — and Organizational Success
As demonstrated by successful organizations across the globe, a safe work culture benefits every area of a business, including employee satisfaction, employee retention, productivity and costs.
However, this dedication must extend beyond compliance and permeate the organization's core culture. It involves clear communication and processes, as well as a commitment to continuous improvement. Ultimately, an investment in safety is an investment in a company’s growth.