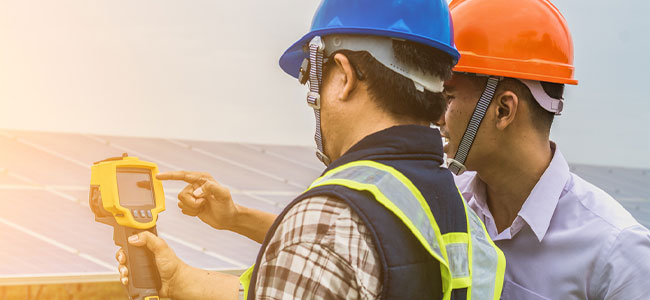
Tips for Using a Computerized Maintenance Management System to Enhance EHS
Using a computerized maintenance management system helps with costs and efficiency but also improves safety and reduces environmental impact.
- By Lindsey Walker
- Dec 07, 2023
The Health & Safety Act 1974 says that employers must keep workplaces safe and healthy. They need to find and fix potential dangers instead of just giving workers safety gear.
Companies can get in trouble if they don't show they're safe and eco-friendly. Using a computerized maintenance management system (CMMS) helps with costs and efficiency, but not everyone realizes it also improves safety and reduces environmental impact.
Fixing things only when they break can lead to accidents. Preventive maintenance is better; it cuts the chances of accidents in half. Here are six ways companies can use a CMMS to enhance EHS (environment, health and safety).
How is CMMS Enhancing EHS?
Reduce Material Waste
A CMMS helps cut down on waste in two simple ways:
- Equipment Life: By taking good care of assets through optimal maintenance, the system ensures they last as long as they're designed to. This means needing fewer replacements, saving money and reducing the amount of stuff thrown away.
- Smart Replacement Planning: The system keeps track of maintenance and repair history, helping plan replacements for assets nearing the end of their useful life. Newer replacements are often more energy-efficient, which not only saves energy but also cuts down on waste.
Using the CMMS for predictive maintenance can also mean fewer routine check-ups, which saves resources like materials and time. All in all, it's a win-win for efficiency and the environment.
Enhance Technician and Operator Safety
A CMMS helps a company follow safety rules and EHS regulations by making sure equipment gets checked regularly and fixed. It also keeps track of accidents and near-misses. The information collected helps plan ways to prevent accidents and improve safety training.
On a day-to-day basis, using the CMMS for predictive and preventive maintenance lowers the chances of things breaking unexpectedly. This is important because it keeps the people working with the machines safe. It also makes maintenance tasks more efficient so that workers are exposed to fewer risks when fixing or starting up equipment.
Save Energy
Using a CMMS helps organizations keep track of how much energy they're using in real time. By looking at this information, we can find patterns and opportunities to save energy. This helps us make smart decisions to use less energy.
For example, regular checks on equipment through preventive maintenance or fixing things before they break can stop machines from using too much energy. Things like dirty filters, dull cutting tools or parts without enough lubrication can make machines work harder and use more energy. Fixing these issues early can save energy and run things more efficiently.
Minimize Environmental Exceedance
Equipment issues such as leaks, spills and excessive waste can harm the environment. Using a proactive maintenance program with a CMMS helps prevent these problems.
The CMMS can watch over hazardous materials and waste. This means it tracks where they are and how much is used or thrown away. By doing this, a company can catch possible environmental problems early and fix them before they become serious. For instance, the CMMS can check if hazardous materials are stored, labeled and thrown away correctly, following all the rules.
Reduce Paper Waste
A CMMS helps cut down on paper usage in four ways:
- Digital work orders. Instead of using paper for creating, assigning and managing work orders, a CMMS does it all digitally. This not only saves paper but also gives a real-time view of how the work is progressing.
- Online forms and checklists. Digital forms and checklists replace their paper counterparts. Filling out and submitting these online reduces the need for physical paper, cuts down on errors and makes collecting and reporting data easier.
- Electronic documentation. A CMMS can store equipment manuals, procedures and other documents digitally. This means no more paper copies, ensuring all information is current and easily accessible to the right people.
- Mobile accessibility. Technicians can use mobile devices to access and update work orders, forms and documents. This cuts down on the use of paper forms, allows for instant updates and improves communication between team members. Plus, it lowers the chance of losing important paperwork.
Optimize Delivery Miles
If a company uses a CMMS, it can help make things more organized. By keeping an eye on inventory levels at different places and getting alerts when things are running low, the company can avoid having to make lots of trips to deliver supplies.
The CMMS also gathers data about maintenance and supplies, and this information can be used to make the supply chain better. This means fewer delivery trips, less pollution and more efficient routes. So, in the end, using a CMMS not only helps avoid equipment problems but also helps the environment by reducing the need for emergency deliveries and cutting down on delivery miles.
Best Practices that Enhance EHS
Focus on the Company’s Culture from the Top Down
Focus on the company's culture right from the top. The key to better EHS training is ensuring that top executives follow the safety guidelines they teach. If the leaders don't follow the rules, it's hard to expect staff to. The organization's culture and management support are crucial for effective health and safety training.
Consider the overall culture of the company when creating EHS training materials. For example, if explaining how to use safety equipment on the work floor, highlight that leaders and managers must also follow the same standards. Change and a strong safety culture start at the top of an organization.
Encourage Everyday Accountability
Encourage accountability among staff members. Safety training is more effective when employees take responsibility for their safety and that of their colleagues. Designate safety companions, like spotters for those handling machinery, to alert each other to unsafe behavior. When employees feel responsible not only to management but also to their peers, they are more likely to engage in and remember EHS training.
Use Data and Analytics to Verify Training Effectiveness
Use data and analytics to confirm the effectiveness of the training. Look for statistics that show fewer injuries, reduced regulatory citations and compliance with internal EHS audits. This indicates that employees are retaining the information from EHS training, such as how to handle dangerous equipment or manage hazardous waste.
Make it Engaging and Interesting
Make the training engaging and interesting. While EHS training is serious, it should also be compelling. Consider conducting it in a virtual or game-like setting. Incorporate questions and anonymous polls during training modules to understand what information employees find most engaging. Ask employees for input on topics that should be covered to make their jobs safer and involve them in the training development. This ensures their support and helps them remember the EHS training, ultimately enhancing workplace health and safety.
Closing Thoughts
Using a CMMS doesn't just fix problems; it helps businesses be kinder to the environment and save money. By using fewer resources, making maintenance operations smarter and causing less harm to nature, businesses can cut costs and work more efficiently. It's not just a tool for fixing things; it's a way for companies to be eco-friendly and boost their profits. Ultimately, a CMMS is a crucial tool for companies wanting a greener future for themselves and the planet.