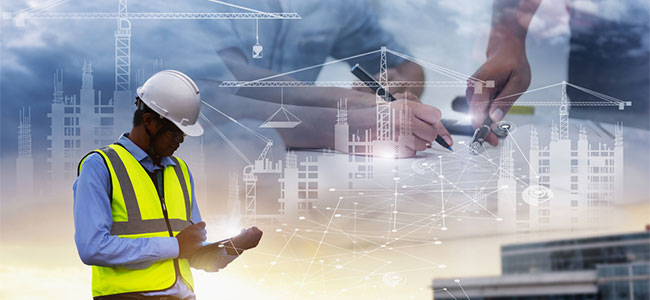
Connected Safety Culture
How to leverage connected safety to reinforce a culture of safety.
- By Lorenza Ordonez
- Nov 08, 2023
Whether we realize it or not, safety technology is ubiquitous in our personal lives. Phones have apps that can send alerts when family members arrive to a destination safely. New cars have technology that can brake before the driver can react in emergency situations. And wearables can even detect medical events and send out “SOS” signals.
Connected safety solutions also have the potential to transform the workplace by protecting both employees and the bottom line. These solutions, including video analytics, sensors, wearables, robotics and other IoT devices, have emerged as a tech-enabled way to help savvy organizations build, establish, and maintain a culture of safety. This is especially important, considering that workplace injuries cost companies more than $167 billion in 2021, according to the National Safety Council.
Your organization likely already has some safety technology and technology-lead programs in place, but how do you use them to take your safety culture to the next level? Let’s break down the key innovations, how they work together, and how structuring an adequate pilot program can increase operational efficiencies, mitigate risk, and manage compliance for bottom line benefit.
Specific Technology Applications
Innovation abounds when it comes to safety technology. Here are some of the new and emerging technologies businesses are utilizing to power their safety efforts:
- Smart cameras can detect and analyze trip hazards or spills, evaluate occupancy in compliance with regulations, and assess ergonomics and PPE compliance. They can also be a valuable component of any security program. The data they collect can be used in combination with other IoT-driven applications or used as standalone insights.
- Wearable devices can perform a wide range of functions that impact worker safety. They can provide immediate haptic feedback if a user engages in unsafe motion that may cause injury and can also monitor worker location and exposure to unsafe conditions, and alert them if needed. For example, if a worker wanders into a dangerous area, or if carbon monoxide levels become too high, a wearable device can alert them that they need to leave. Wearables can also monitor biometric data, such as heart rate and temperature, and send alerts if they reach unsafe levels.
- Sensors can be used to monitor several environmental conditions, such as indoor air quality (IAQ), floor sweat detection (dewpoint) and temperature, among others. Sensors can also be added to equipment to provide notifications when they need to be taken out of service or inspected. The ability to consistently monitor the conditions around your employees can help your organization be proactive in detecting and responding to issues before they become a major safety hazard.
- Robots can handle repetitive, physically demanding or hazardous tasks. For example, a robot could perform measurements and inspections in environments that are too hot or potentially toxic, removing employees from those dangerous situations. Additionally, they can lift and move heavy objects around a warehouse floor, which can reduce the risk of worker fatigue and injury. As an added benefit, by taking on these tasks, robots can free workers up for other more skilled activities, which is critical as industries grapple with an ongoing labor shortage.
- Virtual reality (VR) can be used for safety training purposes. A powerful tool that simulates real-world situations, VR allows workers to train on potentially hazardous scenarios in a safe and cost-effective manner.
- Safety management software helps businesses manage their safety program, assets, and track metrics associated with their environmental, health and safety (EHS) efforts. By integrating all key data feeds into one system, organizations can have a comprehensive view of their safety program, as well as any key metrics or goal progress.
5 Considerations for Connected Solutions
Connected safety solutions vary widely in terms of their capabilities, use cases, install requirements and maintenance needs. Therefore, it’s important to understand the considerations for each and how to maximize their potential. Here are the key elements to consider when working with connected solutions:
- Hardware: Most connected solutions come with a hardware component, whether that’s a wearable device, an actual sensor, or a camera. These will need to be installed, calibrated or adjusted to the appropriate settings in order to achieve the desired objective. Before implementing, make sure these devices meet your needs, fit your budget, and can function within the physical space.
- Software: All connected safety solutions have a software component, which can perform a variety of functions. Software can organize the data, create visualizations and integrations that help us gain deeper insights, initiate a response, and maintain a record of events and safety performance. Consider what features and level of complexity are right for your safety program and make sure any software can integrate with your other devices and systems.
- Connectivity: As the lynchpin of the entire ecosystem, connectivity is a critical consideration. Supporting your connected safety solution with Utility Grade Infrastructure (UTG) will ensure ample bandwidth for low latency applications. This includes wired and wireless connectivity. Depending on the application and environment, you may need to support Bluetooth, Wi-Fi, radio, cellular or private cellular connectivity.
- Solution architecture: When evaluating solutions, you need to consider whether a cloud, on-premise or hybrid option would best fit your needs. However, it’s also important to factor in criticality, bandwidth and the environment. High-bandwidth solutions may require data rationalization near the edge to reduce data costs over a cellular network. Analytics that operate on a smart device, like a camera, can offer greater resiliency, continuing to operate if there is a single point of failure elsewhere. And, the physical environment will often dictate the type of wired and wireless network needed to support your solution.
- Interoperability: Ideally, you’ll want a solution that delivers as much interoperability as possible, but it’s still important to consider your individual needs as well. For example, sometimes a point solution might be an excellent fit, even if it doesn’t integrate with everything else. Generally, though, a solution that allows for interoperability with open APIs has greater potential to combine with other data sources to deliver even deeper insights and automations.
The Power of a Pilot
Adopting new workplace safety technology can be a major investment, and employees may be skeptical of the benefits or have concerns about privacy or the impact it will have on their jobs. Beginning with a pilot program can be a low-stakes way to test solutions and demonstrate results without having to fully commit right away. Additionally, pilot tests give employees the opportunity to provide feedback and see the value of the new solution.
Pilots also allow organizations to identify challenges and work out the kinks before a larger rollout takes place.
At my company, we ran an eight-week pilot of a camera sensor solution in one of our North American distribution centers to gain unique insights into our safety efforts and demonstrate the power of the solution. The results were impressive. Post-pilot, our EHS and warehouse teams used insights gleaned from the video solution to make a measurable impact on workplace safety:
- Improper bending: 13 percent decrease
- PPE noncompliance: 47 percent decrease
- Extended parking duration of powered industrial truck (PIT): 32 percent decrease
- Overreaching: 26 percent decrease
- No stopping PIT at end of aisle: 91 percent decrease
Whether your organization operates in a busy manufacturing facility with heavy equipment or a typical office environment, workplace safety is critical. Safety incidents can disrupt operations, hinder productivity and cause financial harm.
Connected solutions and technology present unique opportunities to help enhance safety programs and reinforce your safety culture. Understanding which advancements are the right fit for your organization today and tomorrow will not only drive the adoption of connected solutions but protect your workforce and your bottom line.
This article originally appeared in the November/December 2023 issue of Occupational Health & Safety.