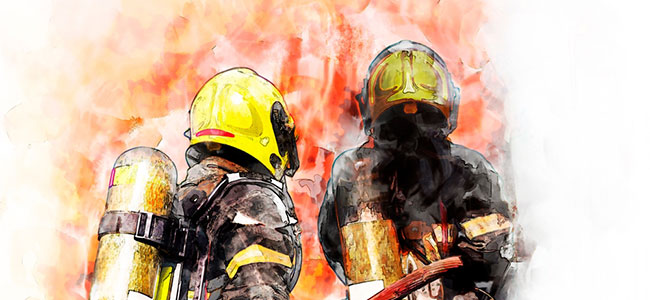
Top Mistakes in Addressing Thermal Hazards
Fires happen every day, often with minor consequences, but plant operators and staff underestimate the importance of thermal hazard risk mitigation and response planning.
- By Nelson Duran
- Oct 13, 2023
Assessing risk is tricky and often prone to subjectivity, with people equating familiarity with safety. Unless we work hard to take an objective approach, our past encounters with and repeated exposure to specific risks can affect our understanding of their potential for damage, muddying the waters to sometimes devastating effects.
For example, while most people feel safer in cars than airplanes, this phenomenon is not rooted in empirical evidence. On the contrary, the average American is over 2000 times more likely to die in a car accident than in a plane crash. This false feeling of safety is based entirely on lived experiences—and the same goes for understanding of thermal hazards.
The National Fire Protection Association (NFPA) estimates that American fire departments respond to nearly 38,000 fires in industrial manufacturing environments each year (based on a study conducted between 2011 and 2015). Just like car accidents, fires happen every day (over 100 each day in industrial environments alone), but the consequences of these events are generally minor and well-contained. As a result, plant operators and staff tend to underestimate the importance of engaging in ongoing and thoughtful thermal hazard risk mitigation and response planning.
That can lead to critical mistakes, such as:
- Hoping for the best and not expecting the worst.
Just because something is unlikely doesn’t mean it’s impossible. Still, many operators and facility managers “risk away” identified hazards because they conclude that low risk means no risk. Most fires, they reason, have no casualties. Additionally, few thermal incidents in industrial settings ever reach the public consciousness. In essence, they accept the risk—to their people, equipment and businesses’ reputations—and move on.
It makes sense. Why prepare if it’s unlikely to happen? But falling into this line of thinking can send operators down a dangerous path. With risk landscapes changing on a dime, assuming a complete understanding of a facility’s risk can be dangerous unless an operator is working to proactively control the risk with safeguards and engaging in rigorous evaluations. Unfortunately, “risking away” often comes with a lack of attention to these critical ongoing assessments.
That aside, the potential damage of this approach to organizational reputations is significant. Sure, most industrial fires escape public scrutiny. But what about blazes that spread to surrounding areas or pollute the air? What about blasts? Explosions? All of them fall under the umbrella of “thermal hazards” too, and their impacts on public perception as well as operations can be devastating.
- Cutting staff out of the conversation.
When it comes to safety and risk, company hierarchies make little difference. Regardless of title or tenure, any person that interacts with industrial equipment or comes into the environment should not only be given proper protective equipment but should also participate in thermal hazard risk mitigation training and be held to the same rules and regulations.
Lower-level employees can be invaluable to managers looking to firm up their thermal hazard risk mitigation protocols. Due to employees’ operational knowledge, they have insight into areas or processes that contribute to thermal hazard incidents that managers may lack, such as which equipment sparks, where liquid pools can form and more. In turn, these employees should be a risk manager’s first stop when evaluating the efficacy of existing or proposed guidance in practice.
- Ignoring extenuating circumstances.
It's easy to view fires and other thermal hazards as isolated risks related only to the flammables and ignition sources within the facility, but there are many other factors that can play a role in these events. Facility culture, changing regulations, process adjustments, scientific findings, new employees and a wide range of other factors can all change the potential for ignition within an environment.
Furthermore, external climate and environmental factors may also play a role. Fluctuations in temperature can lead to volatility in stored chemicals, dry conditions can fuel fires, wind can contribute to growing blazes and wildfires can come knocking on a facility’s doors despite their best efforts to prevent ignition on the floor. If a facility’s thermal hazard mitigations don’t consider these factors, it’s likely to be exposed.
Thwarting Thermal Hazard Risk
Remediating these mistakes will generally hinge on shifting operational mindsets related to these risks. Traditionally, the approach to fire risk management has been rooted in the idea of fire as an inevitability, with mitigation efforts centered on reactive measures designed not to prevent fires from starting, but rather from mitigating their impact when they do start.
While harm reduction is important for any type of hazard, relying on these tactics alone leaves businesses exposed. It may only take a split-second for equipment to overheat or accelerant to ignite. When it does, the damage can quickly become catastrophic. For example, a fire can completely destroy a wind turbine in just a few minutes, and it takes less than one minute for a small fire to turn into a major event. And this doesn’t even scratch the surface of what blasts and other, more instantaneous thermal events can do. In short, thermal incidents can do significant damage in the blink of an eye. Therefore, preventing them from starting in the first place is the best way to mitigate their impact.
Leveling the field between proactive and reactive safeguards should begin with developing a holistic and comprehensive risk profile to contextualize and quantify thermal hazard risk within the enterprise ecosystem. This will help managers diversify their approach and split their investments between reactive measures (sprinkler systems, extinguishers and adequate fire exits) and proactive ones (remodeling or restructuring based on the results of infrared thermography evaluations, finite element analysis, gas dispersion modeling and re-engaging employees in comprehensive training). Balancing these two approaches can help managers ensure they’re taking steps to prevent ignition and be better prepared to respond if it happens.