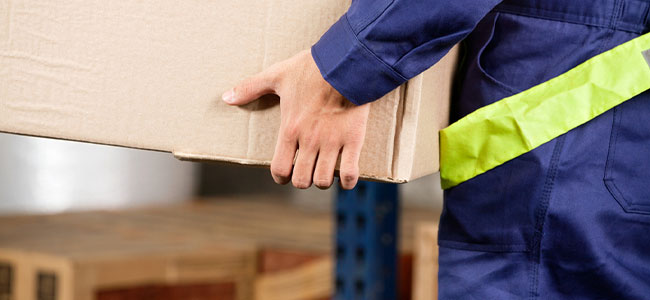
Rethinking Manual Material Handling in Warehouses
Unpacking the training of manual material handling — from current challenges to future trends, and the strategies warehouse managers can employ for a safer, more efficient workplace.
- By Holly Pups
- Oct 11, 2023
Manual material handling is critical to warehouse operations, but it can be extremely challenging and dangerous for employees. Warehouse managers can implement best practices to improve safety and efficiency and embrace emerging technologies to make manual material handling more efficient and ergonomic.
Among the various tasks involved in warehouse management, manual material handling plays a key role in ensuring goods are properly stored, organized and transported within the facility. While automation and technology have brought significant changes to the industry, manual material handling remains essential due to its flexibility, cost-effectiveness and adaptability.
Challenges in Manual Material Handling
Manual material handling involves workers physically moving goods and materials without the aid of machinery such as forklifts. This can include order picking and loading pallets by hand, as well as using pallet jacks and carts to move products. While this process has its advantages, it also presents several challenges that warehouse managers and workers need to be aware of and address:
- Ergonomic hazards
- Worker inefficiency and inconsistent performance
- Safety concerns
- Labor costs
One of the most significant challenges of manual material handling is the risk of physical strain and other ergonomic injuries to workers. Repeatedly lifting, carrying, and moving heavy objects can lead to musculoskeletal disorders, back injuries, and other health issues.
Manual material handling can be time-consuming and less efficient than to automated processes. Workers may need to cover longer distances and expend more energy to move goods, leading to reduced productivity. It is also important to note that work capabilities from worker-to-worker can vary greatly, leading to differences in employee performance in handling, lifting, and transporting goods. This can result in errors, damaged products, and uneven workloads among workers.
Warehouse environments can be hazardous due to factors such as slippery floors, limited visibility, and the presence of powered industrial trucks. Manual material handling increases the risk of accidents, especially when workers are not adequately trained on the hazards in their work areas or when safety protocols are not followed.
While manual labor can be cost-effective in some cases, it also comes with associated labor costs. These costs include employee wages and overtime, training time, insurance, correcting errors, and potential medical expenses resulting from injuries.
Best Practices
Warehouse managers can implement several effective strategies to enhance manual material handling operations. Companies should start by providing proper training and education for workers. Effective training ensures employees are well-versed in safe lifting techniques, correct posture, and proper handling procedures. Regular training sessions help prevent injuries and maintain a skilled and knowledgeable workforce.
Considering how employees interact with their work environment is crucial when designing ergonomic workstations. Creating workstations and storage areas that minimize the need for workers to bend, twist, or lift heavy objects can significantly reduce physical strain. Incorporating ergonomically-designed equipment and tools further alleviates the physical toll on employees, promoting their well-being.
Another valuable practice is task rotation. Avoid overexertion and monotony by periodically shifting workers between different tasks. This approach helps mitigate the risk of repetitive strain injuries and keeps employees engaged and motivated.
Setting clear weight limits for lifting objects and carrying tasks is important. Providing tools like lifting aids, trolleys, and dollies for handling heavier loads can greatly facilitate the process. Implement two person lift procedures for lifting large, heavy, and awkward objects.
A well-organized and clean warehouse layout contributes to efficient material handling. Placing frequently accessed items within easy reach minimizes unnecessary movements and reduces the time and effort required. Keep the work area free and clear of debris and other hazards that could cause a slip, trip, or fall.
Safety measures play a pivotal role in manual material handling. Enforcing strict safety protocols, including the use of personal protective equipment (PPE), maintaining clear pathways, and promptly addressing any safety hazards, is vital to ensure a secure working environment.
Promoting collaboration and communication among workers, supervisors, and management is beneficial. Encouraging employee feedback regarding potential improvements in manual material handling processes can lead to more effective strategies and a safer workplace overall. This helps employees feel like they are valued and appreciated.
Future Trends
The future of manual handling in warehouses is likely to be shaped by several existing and emerging technologies. These trends include the following:
- Rise of assistive technologies
- Use of data-driven insights
- Adoption of collaborative robots (“cobots”)
- Use of augmented reality (AR) and virtual reality (VR)
- Emergence of on-demand labor platforms
Assistive technologies such as wearable devices, exoskeletons, and ergonomic tools are becoming increasingly sophisticated and affordable and are being used to reduce physical strain on warehouse workers. These technologies can help to prevent injuries, improve productivity, and reduce absenteeism.
Warehouses are increasingly using sensors and data analytics to collect information about inventory levels, traffic patterns, and worker movements. This data can be used to optimize the handling of materials and identify areas where efficiency can be improved.
Cobots are designed to work alongside human workers. They can perform tasks such as lifting, conveying, and transporting goods, which helps reduce workers’ physical workload. Cobots can also be programmed to perform repetitive tasks more accurately and consistently than human workers.
AR headsets can be used to provide warehouse workers with visual guidance and overlays. This helps them to pinpoint items, navigate precise routes, and make better decisions during manual material handling tasks.
VR and AR are being used to develop more immersive and realistic training simulations for warehouse workers. They are interactive and allow workers to make real-time decisions and see the consequences in a virtual environment. This helps them to learn new skills quickly and safely.
On-demand labor platforms make it easier for warehouses to quickly scale their workforce up or down to meet changing demands. This helps to ensure that there are always enough workers available to handle the workload without overstaffing or understaffing.
These trends are all expected to have a significant impact on the future of manual material handling in warehouses. By adopting these technologies and practices, warehouses can improve safety, efficiency, and productivity.
Key to Remember
Manual handling remains a fundamental aspect of warehouse operations, despite the advancements in automation and technology. Warehouse managers must balance the benefits of manual material handling with the associated challenges by implementing best practices, prioritizing worker safety, and embracing emerging trends in the industry. As technology continues to evolve, manual material handling will likely become more efficient, ergonomic, and integrated with smart warehouse systems, contributing to improved Overall safety of the workplace.
This article originally appeared in the October 2023 issue of Occupational Health & Safety.