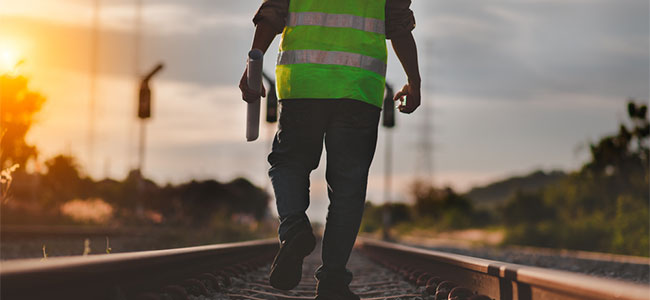
Raising the Bar: The Rise of Rigid Rail Systems in Aviation and Rail Worker Safety
How the next generation of fall protection systems will streamline safety, productivity, and cost-efficiency in transportation businesses.
- By Kevin Kelpe
- Oct 11, 2023
In the high-stakes environments of the aviation and rail industries, a single misstep can have severe consequences. Imagine a mechanic working above the ground, diligently maintaining an aircraft, or inspecting a sprawling train. It’s not only their lives that hang in the balance but also the safety of the passengers who depend on the integrity of these machines.
However, maintaining safety while maximizing productivity is often challenging in these demanding environments. Traditional fall protection systems, while necessary, can often hinder movement and decrease efficiency. But what if there was a solution that promised both uncompromised safety and streamlined productivity?
Rigid rail systems do exactly that, providing effective fall protection while enhancing operational efficiency. This article will guide you through the transformative power of these systems in maintaining robust safety standards, enhancing productivity, and significantly reducing costs in the aviation and rail industries. From understanding the intricacies of low fall clearance and worker mobility to the benefits of trolley rail systems, you’ll discover how safety and efficiency can truly go hand-in-hand.
So, whether you’re a frontline worker navigating an aircraft or train, a safety officer dedicated to upholding the highest safety standards, or an executive aiming to boost operational efficiency, it’s time to raise the bar and explore how these innovative fall protection systems are rapidly enhancing safety and productivity in the aviation and rail industries.
The Challenge
In the bustling world of aviation and rail industries, worker safety and efficiency are paramount. Employees in these sectors frequently navigate challenging environments, with two issues standing out: low fall clearance and the need for worker mobility.
Low fall clearance, a precarious situation — Low fall clearance essentially refers to the limited distance available between a worker and the ground or obstruction below. In other words, there’s very little room for error.
Picture a rail yard worker walking along the top of a train. In this scenario, the worker is high enough off the ground to be seriously injured in a fall but may not be high enough for more common fall protection methods to arrest their fall. This proximity presents a unique problem: the fall protection system must arrest a fall almost instantaneously.
Worker mobility, a must-have for efficiency — In addition to low fall clearance, these industries necessitate a high degree of worker mobility. Employees often have to move along the length of a train, airplane, or heavy equipment to carry out their duties. This mobility is integral to efficient operations, but it also introduces additional risk, as the potential for falls increases with movement.
Take, for example, a rail yard worker. Their duties may involve traversing the length of a long freight train to inspect couplings, brakes, and wheels. Similarly, aviation mechanics must frequently navigate the length and breadth of an aircraft fuselage, from nose to tail and wingtip to wingtip, performing maintenance tasks, inspections, and repairs.
Traditional fall protection systems, while sufficient for many industries, may not provide the optimal solution in these specific scenarios. Harnesses that restrict movement or anchor points that need constant repositioning can hamper a worker’s efficiency and potentially introduce additional safety hazards.
Conventional Systems
Conventional fall protection systems often struggle to balance safety and worker mobility. For example, a harness with a fixed-length lanyard might limit the distance a worker can safely travel. Every time workers move beyond this distance, they must detach and reattach their lanyards, introducing moments of vulnerability and increasing the time it takes to complete a task.
The challenge, then, is not just about meeting the stringent fall clearance requirements. It’s also about enabling transportation workers to move freely and efficiently without constantly having to re-adjust their safety equipment or compromise their safety. This underscores the need for innovative fall protection solutions tailored to the unique demands of the aviation and rail industries.
Trolley Rail and Enclosed Track Systems
Finding a solution that safeguards workers and facilitates efficient operations is a pressing priority. One of the most promising responses to this challenge is trolley rail or enclosed track fall protection systems. These innovative systems offer the flexibility and safety these industries need.
How it works: A trolley rail or enclosed track fall protection system incorporates an overhead rail that allows a trolley to move along its length. The worker is connected to this trolley via a safety harness and a self-retracting lifeline (SRL), enabling linear movement along the rail.
These systems are rated for fall arrest, meaning they’re designed to stop a fall quickly and safely. Combined with the right Personal Protective Equipment (PPE), such as full-body harnesses and lanyards, these systems limit freefall and reduce arrest forces.
This is a marked improvement from traditional fall protection systems, which often require workers to disconnect and reconnect their harnesses as they move along the work area. By contrast, trolley rail systems ensure continuous, unbroken safety coverage, greatly reducing the risk of falls during transit and enhancing overall safety.
Reinforcing safety — The complex task of ensuring worker safety in the aviation and rail industries is addressed using robust, versatile rigid rail systems. Using long-span triangular truss designs, these systems offer advantages such as spanning large distances with fewer structural attachments, resulting in cost savings, strength, flexibility, and improved safety.
Cost efficiency and mobility — Rigid rail systems, especially those utilizing TD3 triangular truss, are an investment that keeps giving. They deliver substantial cost savings by allowing longer spans between support columns—up to 80 feet—reducing the need for frequent concrete foundations and column installations. This feature not only cuts down on material costs but also offers increased flexibility in system layout and placement.
Even more noteworthy is the modular nature of these systems. They can be disassembled and reassembled at different job sites, thus negating the need for new purchases with each relocation. This feature becomes particularly valuable in industries where mobility is a significant factor, such as rail yards undergoing upgrades or aviation hangars subject to reconfiguration.
Strength and Flexibility
The unique TD3 truss design isn’t just beneficial for its cost-effectiveness. It also packs considerable strength, allowing the system to bear hefty loads without buckling. This strength, significantly greater than that of other systems that can only span 60 feet, is crucial in industries where heavy equipment or machinery may be involved.
These strong spans mean that rigid rail systems can effectively serve diverse industries, from agricultural applications where machinery is substantial to chemical environments where equipment durability is paramount to rail and aviation contexts that require long, uninterrupted spans for worker mobility.
Every worksite comes with its set of challenges—fixed structures, tight spaces, and obstacles that need to be worked around. Here too, rigid rail systems, with their ability to bridge long distances, offer an innovative solution.
Consider a rail yard with various fixed structures, such as cranes, tool sheds, and power units. The longer spans allowed by the TD3 truss allow you to install the foundations and supports where they best fit, working around these existing structures.
Enhanced Safety
Rigid rail systems deliver unparalleled safety. Compliant with OSHA standards, these systems offer industry-leading safety solutions by providing lateral fall protection across the entire system length, minimizing swing fall risks.
Coupled with a harness and self-retracting lifeline, these systems enable workers to perform tasks with their hands free, enhancing productivity without compromising safety. This unbroken, continuous design eliminates the need to unhook and re-hook the system when accessing different parts of the workspace, thereby providing an added layer of protection against potential falls.
The power of rigid rail systems lies in their exceptional blend of cost-efficiency, strength, flexibility, and safety, marking a significant step forward in workplace fall protection, particularly in high-risk industries like aviation and rail.
Solutions for High-Stakes Work
In conclusion, the developments in fall protection systems raise safety and efficiency standards in high-stakes industries like aviation and rail. Systems like the trolley rail and rigid rail provide a balance of safety, worker mobility, and productivity, which are essential in these demanding environments.
However, the key to truly harnessing the benefits of these systems lies in understanding the unique challenges and requirements of your workspace and tailoring these solutions to fit your needs. The right combination of a trolley rail or enclosed track fall protection system with appropriate personal protective equipment (PPE), and leveraging the strength and flexibility of the rigid rail systems can make all the difference.
Remember, these solutions not only ensure compliance with safety regulations but also empower workers, instilling a sense of security that allows them to work more efficiently. They also offer cost-effective, durable, and adaptable solutions that provide value for money in the long run.
If you’re responsible for workplace safety or operations, explore the range of fall protection systems on the market today and transform your approach to safety and productivity.
This article originally appeared in the October 2023 issue of Occupational Health & Safety.