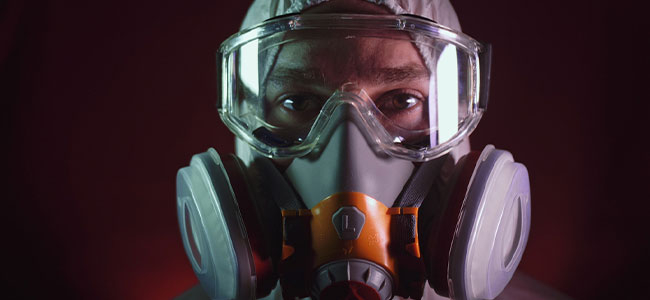
Monitoring Exposure of and Protecting Employees from Silica Dust
Understanding the challenge posed by silica dust exposure on site and in confined spaces, and the comprehensive standards and measures used to combat its peril.
- By Tim Turney
- Oct 11, 2023
Approximately 2.3 million workers in the United States are exposed to Respirable Crystalline Silica (RCS) or silica dust every year, which is now known to possess a similar magnitude of risk as the more widely understood asbestos dust. Crystalline silica is found in many commonly used construction materials, including sand, gravel, clay, stones, concrete, bricks and quartz. When these materials are broken, stirred or otherwise disturbed through cutting, drilling, grinding or crushing, minuscule dust particles are created. When inhaled, these particles travel deep into the lungs and can cause incurable and sometimes deadly respiratory diseases such as silicosis, chronic obstructive pulmonary disease and kidney disease.
The Department of Labor has recently (June 2023) proposed a new ruling to limit silica dust exposure by its Mine Safety and Health Administration (MHSA) to better protect miners’ health. This comes almost exactly ten years after The Occupational Safety and Health Administration (OSHA) proposed a rule aimed at curbing workers’ exposure to crystalline silica across all industries by updating the Permissible Exposure Limit (PEL) to be in line with modern understanding of the hazard. The newest proposal by the MHSA would see the PEL of silica dust at or below 50μg/m3 (micrograms per cubic meter of air) for a full shift of exposure, equal to an eight-hour time-weighted average. For reference, the PEL of any hazardous dust in the workplace is ten milligrams per cubic meter.
As with any known workplace health risk, the most effective means of reducing worker exposure to respirable crystalline silica is a correctly implemented scheme of controls using the hierarchy of controls. This can help reduce both the likelihood of workers developing health complications such as silicosis and the potential legal ramifications for employers. Measures include a correctly executed program of air monitoring, which can include both monitoring at the site level and on an individual employee level using personal sampling pumps. Air monitoring can quantify exposure levels, or if controls are in place, check that they are effective and measure any residual risk. These pumps are essential in places where there is a significant risk of highly concentrated hazardous pollutants in the surrounding air, for example, confined spaces and sites that emit large quantities of fumes.
Control Measures
In controlling dust, the usual risk control hierarchy applies. Where the risk cannot be eliminated entirely, a safer form of the product should be used. If this is not feasible, the process should be changed to emit less dust or enclose the process so that the dust does not escape or by extracting the dust near the source using local exhaust ventilation (LEV). Employers should make the process efficient enough to have as few workers in harm’s way as possible. In the hierarchy of control, the last thing you apply is respiratory protection. Often, because of poor understanding of toxicity and dust concentration, the wrong respiratory protection is used.
Businesses can measure worker exposure using personal sampling pumps. Employers must determine the amount of silica that workers are exposed to if it is, or may reasonably be expected to be, at or above the action level of 25μg/m3, averaged over an 8-hour day. It is important that the pumps are used with the correct sampling head and, in the case of respirable crystalline silica dust, a cyclone and filter, which collects the particulate.
Once the sample is analyzed by a laboratory, the level of exposure can be calculated. If the results of this assessment show that the exposure level is above the PEL of 50μg/m3 action is then taken to improve control measures to ensure exposure is reduced to as low as practicably possible. Many improvements have been made to personal sampling pumps over time. Battery technology, back pressure capability, accurate flow control, minimized pulsation, data download and the ability to be intrinsically safe have all been improved, ensuring measurement of an individual’s exposure to harmful substances is as accurate as possible. Understanding these factors in which the personal sampling pump needs to operate effectively will allow employers to choose the most effective device suited to their working environment.
Correct implementation of personal sampling relies on a thorough understanding of practice, procedure, how sampling pumps function and use of the correct sampling head and filters.
Correct equipment, calibrated properly
Personal sampling pumps must adhere to the standard ISO 13137:2013. The standard sets limits for required flow stability and maximum permissible pulsation levels, enabling users of personal air sampling pumps to adopt a consistent approach for flow rate assessment.
This standard provides a comprehensive framework that specifies test methods to determine the performance of air sampling pumps and ensures that environmental influences such as air pressure and temperature have a minimal impact on the accuracy of the sampled air, which in turn could affect sample results.
Correct equipment — calibrated properly — and an awareness of the limitations and impact on data collection that the equipment itself can have, should be at the forefront of correct air monitoring procedures as well as the fight against “the new asbestos.” Pumps that operate with a pulsation value of less than 10 percent and conform to all relevant ISO standards give industrial hygienists and site managers the peace of mind that the data captured is reliable and unaffected by pump pulsation. Low pulsations is particularly important when sampling for crystalline silica as the sampling head is a cyclone, and only at low pulsation levels will it get the correct ‘respirable’ sample.
While awareness of silica’s negative health effects is on the rise, correct procedure, safety-focused culture, and the right equipment will ensure that the downward trend of silicosis mortality continues.
Confined Spaces
Working environments that can be classified as confined spaces, an area or vessel large enough to enter and perform work with limited entry and exit potential, are inherently dangerous when there is a risk of hazardous gases being present or lack of oxygen, such as a tank, mine shaft and vaults. OSHA refers to these as permit-required confined spaces and advises that these confined spaces should be tested prior to entry and continually monitored and ventilated.
When it comes to dust, the atmosphere within a confined space can provide additional challenges. The risks are potentially compounded due to ventilation issues, and therefore, there is the potential for higher concentrations of airborne dust. The requirement for LEV becomes even more important; otherwise, the levels of dust will accumulate. The use of a real-time dust meter can be especially useful in this case to get an instant indication as to whether control measures are effective or additional measures are needed.
Employee Awareness
Employee health must remain a priority and a core component of any workplace health and safety management system. Likewise, monitoring must continue to evolve in accordance with changing production methods, and the industry is already moving in a positive direction.
In addition, education and training that raises workers’ awareness of the risks of dust exposure is integral in ensuring that they understand how to prioritize and protect their health.
This article originally appeared in the October 2023 issue of Occupational Health & Safety.