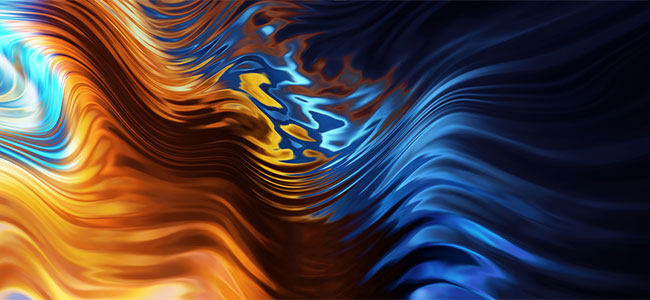
Heat Transfer Systems and Safe Chemical Processing
From proactive risk assessments to comprehensive training: A deep dive into ensuring safe and sustainable heat transfer in manufacturing facilities.
- By Tim Powell
- Oct 11, 2023
Manufacturers frequently employ heat transfer systems to sustain the high temperatures necessary for various forms of indirect heat transfer processes. Historically, facilities opted for steam-based systems because water is readily available, affordable, and commonly regarded as sustainable. However, achieving the temperatures required for industrial processes necessitated operating the system at extremely high pressures of around 1200 psi (83 Bar). This meant that, without adequate steam ventilation mechanisms in place, the pipes ran the risk of bursting and gaskets failing, allowing hot steam to escape, and putting workers at risk.
Thermal fluids, on the other hand, can safely maintain temperatures at much lower pressure and can be tailored to applications. They are suitable for both heating and cooling applications, with temperature ranges spanning from -130 to +1112 degrees Fahrenheit.
While they offer a safer alternative to steam and are designed to deliver prolonged and efficient service, facilities employing heat transfer fluids should still adopt preventative measures to extend fluid lifespan and meet safety standards.
To comply with industry regulations, manufacturers using heat transfer fluids must take proactive steps to assess potential risks and implement measures, such as predictive maintenance and remote monitoring, to eliminate them as much as possible. Thermal fluid, while classified as a dangerous substance, can offer reliable service for many years when monitored and managed proactively. This can be a safer, more sustainable, and cost-effective solution for manufacturers.
Risk Management
While heat transfer fluid has an effective life expectancy of many years, its efficacy decreases as it nears the end of its lifespan. This decline can lead to the introduction of by-products into the system. Specific regulations outline guidelines for health and safety managers to reduce the potential risks linked to this degradation, but this is often easier said than done. This is because once thermal fluid is introduced into the heat transfer system, it is no longer visible, allowing any underlying problems to remain unnoticed until they disrupt production.
To manage risks effectively, health and safety managers should closely collaborate with thermal fluid specialists to monitor fluid condition. Engineers should take a closed thermal fluid sample when the system is hot, live and circulating, so they can accurately assess the fluid’s status. Quarterly sampling and thermal fluid analysis help engineers monitor its condition. These findings enable health and safety managers, along with production and engineering managers, to track the fluid’s condition over time and adjust procedures to minimize the risk of incidents.
In addition, facilities have the option to employ remote condition monitoring, which can improve proactive maintenance efforts. Cloud-based remote monitoring systems use live, real-time analytics to diagnose potential issues. As soon as the system detects an anomaly, it warns maintenance personnel by sending an alert on their smart devices. This advanced technology empowers engineers to prolong the safe and effective use of thermal fluid.
Facility Maintenance
While the engineers will monitor fluid and system conditions to maintain uptime, health and safety managers can also implement on-site protocols to protect workers from risk.
Promoting good housekeeping practices not only enhances productivity but also fosters a safe working environment. For example, clearing pathways and relocating electrical cables are quick ways to eliminate potential trip hazards. Additionally, health and safety managers should strategically position spill kits and personal protective equipment (PPE) within close reach of the system, ensuring that workers are well-informed about their locations to enable swift action during emergencies.
Engaging thermal fluid experts to conduct site surveys and risk assessments is another valuable step health and safety managers can take to evaluate the facility comprehensively and get recommendations on any areas for improvement.
In situations involving potentially dangerous and flammable substances like thermal fluid, health and safety managers must emphasize the vigilant monitoring of any fluid outside the system, typically resulting from leaks or waste fluid spills. Swift action should be taken to address any spills — neglecting them could increase the risks of slips, trips, and fires.
Good signage detailing safety procedures is an important part of adhering to regulations. Properly labeling flammable substances, high voltage zones, and potential hazards is crucial. Simultaneously, additional signage can outline the best and safest procedures.
When controlling the temperature of the fluid and system, manufacturers must also consider how the heating process will impact the rest of the facility. If the system or other machines in the facility exceed their intended operating temperatures it can lead to equipment failure — electronic panels, for instance, can begin to fail once they exceed 104 degrees Fahrenheit. Correctly installing insulation across the system pipework enables engineers to better regulate temperature. Non-porous insulation, such as blown glass, works well in these applications because if the fluid leaks, the insulation will not absorb the fluid, helping to minimize the risk of fire.
Training Matters
Educating all staff, whether existing or new, on safety measures and their importance, as well as best practices for procedures like monitoring thermal fluid, is integral to heat transfer maintenance.
Collaborative efforts, such as engaging thermal fluid specialists for routine fluid sampling, implementing facility upkeep, and providing thorough staff training, are indispensable for maximizing the safe, working lifespan of thermal fluid. These strategies can help health and safety managers mitigate potential risks, establish a safe workspace when dealing with thermal fluids, and maintain adherence to local regulations while supporting the ongoing operations of the chemicals industry.
This article originally appeared in the October 2023 issue of Occupational Health & Safety.