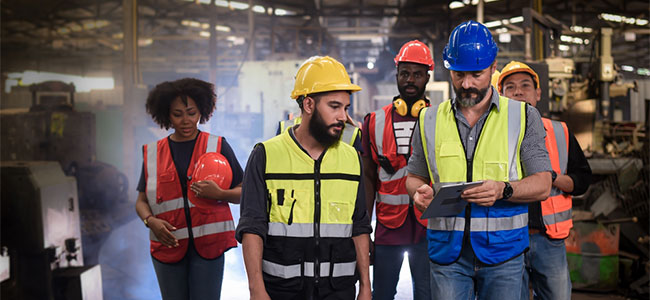
Fall Protection An Ongoing Conversation
How can employers develop a comprehensive training program and instilling a safety culture to prevent slips and falls?
- By Michael Schulte
- Sep 06, 2023
Preventing slips and falls is a high priority across industries because they are both dangerous and preventable. In 2020, according to the National Safety Council, 805 workers died from falls. In addition, more than 210,000 were injured so badly that they were forced to take time off from work. These injuries are expensive, costing the nation billions in medical expenses, workers’ compensation, and litigation.
On the other hand, safe conditions are good for productivity. When employees can plant their feet on the floor – without worrying they might start skating across it – they can move more confidently and focus on their jobs.
In a perfect world, companies could set up a single, two-hour training program that would educate their employees and new hires about safety. While these safety seminars are certainly valuable, they don’t get the job done on their own. Without daily reinforcement, training is often forgotten in the hustle of our daily work.
Safety must be part of the ongoing conversation and fully enmeshed in company culture to maximize slip and fall prevention and other protective measures. Safe environments don’t just happen – they must be engineered. That means everyone from the shop floor to the C-suite needs to take an active role and ensure the safety conversation never stops.
At our company, we manufacture specialized safety flooring products and surface technologies, covering walkways, entryways, stairs, and ladders where people live, work and play. As a result, safety is part of our DNA and every bit as important in our own facilities as it is in the places we service.
Safeopedia reports that 66 percent of falls occur on the same level due to a slip or trip, so installing the right non-slip flooring is a key step to pre-engineering a safe environment. Managers can then take a holistic approach to slip and fall prevention by considering the many elements that can cause accidents, such as workplace clutter, wet and/or greasy surfaces, and poor situational awareness, to design a safety program that works for their organization using the following practices.
Make Safety More Meaningful
Instilling a safety-focused culture is as much mentoring as it is direct training. Every team in a plant has regular meetings to discuss jobs, maintenance, and other matters, which are excellent opportunities to reinforce safety.
Our meetings generally run around 15 minutes, and it’s amazing what we can cover in that time. Regarding safety, we discuss unaddressed hazards, near misses, and how to prevent them.
Identify teachable moments. Recently, a maintenance crew at our company was blowing out some equipment, but they were called away for another, more urgent task. Unfortunately, they left the hose they were using uncoiled. I reminded them that it only takes 30 seconds to coil the hose and eliminate an obvious trip hazard.
Don’t assume that every worker knows the safest ways to do their work. For example, climbing hinges on points of contact: four is ideal, and three is the minimum. In addition, when climbing a ladder, always grasp the rungs, never the sides. Simple tips like these are perfect for teachable moments.
Footwear is another important issue. Worn boots increase the risk of slipping and falling. Our company has a boot program in which the company pays up to $175 for a new pair. To make it more convenient, we bring a boot supplier to the plant every six months. Employees can replace their worn boots without a trip to the store.
It’s a great investment in safety and goodwill. Employees appreciate that we walk the walk on slip and fall prevention. We recognize that our employees are the backbone of our operation, and we want to support their well-being.
Encourage Situational Awareness and the Strategic Pause
Plant safety requires situational awareness at all levels. People must internalize those tasks, such as carrying heavy materials up and down stairs, are intrinsically risky. This starts with training and continues with ongoing safety discussions to encourage workers to be in the moment (not on their phones or thinking about their upcoming vacation) and focused on getting the current task done.
It’s important to train people how to perform their jobs safely, but leadership must also consider how those tasks are being conducted. Are the handrails adequate? Is there a safer way to move those materials up and down?
Another ongoing issue is obstacles in walking lanes. This can be tricky because sometimes, in manufacturing, items must be set down. However, even if necessary to perform the job, people must recognize the trip hazard and remove it as quickly as possible to clear the walkway.
One of the riskier parts of manufacturing is the constant need for urgency. Customers want the product yesterday, and employees and managers naturally feel that pressure. They move faster than they should, become overly focused on the task, and lose situational awareness. People in a hurry are often less focused on safety.
We believe no deadline is worth an injury. We encourage people to slow down and assess a potentially risky task – take a strategic pause.
Workers generally know the difference between doing something safely and unsafely. Give them the space to exercise sound judgment. Saving an hour probably won’t make any difference to a client, but it could spare an employee a broken leg and weeks off the job.
Demonstrate Active Listening
Many of our best ideas – including the boot stipend – have come from employees, and I can’t overstress what an important role they play in maintaining a safe environment.
Good managers try to walk the floor as much as possible, but sometimes it’s hard to get there, and these sporadic walkthroughs can’t fully capture the minute-to-minute realities. Employees will tell us where the hazards are – we just need to hear them.
When looking at all the different aspects of creating a safe environment – initial trainings, regular meetings, mentoring, teachable moments, catching people doing great work – the throughline is empowering workers. Nobody knows their jobs better, and they should feel comfortable telling us when something is not right.
When our employees noticed that gritty materials from the shop were making nearby walkways a bit slick, we created a plan to enclose the shop. We’ve also been working with the maintenance team on safe climbing. Should we replace ladders with stairs? Is there a better way to get tools up to higher levels? Should we leave a set of tools up there? Their insights are always invaluable during these discussions.
This is really the bottom line to ensure safety: It’s an ongoing conversation. No single person or group knows everything about what’s going on in the plant or the budget or the best options to rectify a potentially hazardous situation. But when managers and employees put their heads together, the diversity of thought and varying perspectives can lead to the development of good solutions.
Using a collaborative process to develop new solutions also builds support for any new protocols that need to be implemented.
One of the best parts about initiating these conversations is that they get better over time. As employees’ ideas get implemented, they start to recognize that they are part of the innovation process, and that makes them more forthcoming. We don’t do everything they suggest, but we make sure they know they’re being heard.
It’s really just basic transparency. We want to hear what they have to say, and we’re not going to mark them down in some file. This is what we want.
Never Stay Put
Safety is a dynamic issue, and it’s important to constantly refine how we approach it. My company has conducted ad hoc discussions at daily meetings and other opportunities for years. That’s worked quite well, but we can still do better.
In April 2023, we started conducting more formal workplace walkthroughs called Gemba Walks to discuss safety, quality, and delivery with each team daily. The meaning for Gemba is “where it happens,” so it literally defines the act of seeing where the actual work happens. A Gemba Walk is a lean process method for continuous improvement, it goes far beyond checking compliance safety standards. We talk to our people out on the manufacturing floor where the work takes place, and equally important, we listen.
It’s been reinvigorating for employees because they know we are working to protect them. They also recognize that it’s okay to slow things down, when necessary, to make the plant safer for themselves and their colleagues. The more we empower each other to contribute to a safer workplace, the better we become.
This article originally appeared in the September 2023 issue of Occupational Health & Safety.