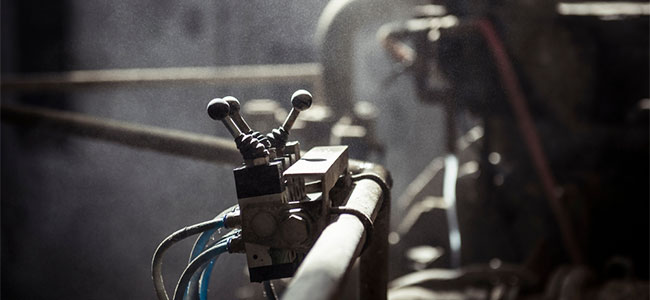
Combustible Dust in Industrial and Manufacturing Settings
Expert Mark Ramos joins OH&S to delve into the unseen challenges and solutions when it comes to managing combustible dust in industrial and manufacturing facilities.
- By David Kopf
- Sep 06, 2023
Throughout nearly every industrial or manufacturing facility lies a silent yet potent adversary: combustible dust. Often overlooked, combustible dust has the potential to wreak havoc. For safety managers, the challenges of managing and mitigating these threats can be daunting.
A seasoned expert who is no stranger to the challenges and intricacies of managing combustible dust in industrial-manufacturing settings is Mark Ramos, the Business Development Manager IVACS, Western Region, for Nilfisk, a global manufacturer of professional cleaning equipment, including systems for collecting combustible dust.
Ramos has dedicated his work at Nilfisk to understanding and addressing the complexities of dust collection and safety. Having joined the company in 2000 as a district sales manager for the Pacific Northwest, Ramos’s responsibilities grew over time, leading him to oversee territories spanning from the U.S. states of Oregon, Washington, Idaho, Montana, and Alaska to the western provinces of Canada. ,
Hi work in dust collection and safety took on even more importance in 2008, when the fatal explosion at the Imperial Sugar Mill in Port Wentworth, Ga. prompted OSHA to heighten safety regulations surrounding combustible dust. Ramos, having been on the field and in management roles, witnessed firsthand the industry's response to these regulatory shifts. His travels across diverse regions allowed him to interact with a variety of industries, broadening his understanding of the safety concerns surrounding dust.
In a conversation with Occupational Health & Safety, Ramos provides insights gleaned from his years in the field, offering a comprehensive view of combustible dust management's challenges and solutions in the industrial-manufacturing setting.
OH&S: What makes the industrial-manufacturing setting unique when it comes to combustible dust safety?
Ramos: A lot of it is about buildup. In most facilities, it comes down to basics. It's about the programs you have in place to mitigate dust buildup. Do you consistently monitor and remain true to whatever your policy is? I could share some stories from over the years and places I've visited. When you walk into a facility and say, "I'm gonna do a site assessment," you try to understand what people's challenges are.
A lot of people see everything that's going on at floor level. We can look down and see what's on the floor, and observe what's in and around equipment. But I tend to look up. If you observe dust residing in the rafters, that's the "out of sight, out of mind" dust that exists in many facilities. This indicates there's probably not a comprehensive program in place.
So, I think the challenges are to really help people realize what's going on in the facilities. It's important to know that there are processes and equipment that can address these issues. That's an ongoing challenge we face in the field.
OH&S: Are there certain types of manufacturing or industrial environments that are more prone to combustible dust than other than others?
Ramos: Under the right circumstances, I wouldn't say one industry is more prone to having issues than others. However, there is a KST chart that indicates materials that are more combustible than others.
But just because something has a lower rating doesn't mean that there's less of a risk. It really depends on the variables at hand. Metal dust, being more volatile, means people in related industries tend to understand that, and perhaps they're more proactive about addressing it.
OH&S: You mentioned rafters. Are there other areas of an industrial or manufacturing facility where dust accumulates more than others?
Ramos: Well, in and around equipment, as I mentioned earlier, is obvious. The dust that's on the floor, that's easily visible. However, there are other places like I-beams or ventilation system pipes located in the upper parts of the plant. You might also find internal office spaces within the facility with roofs, and dust can accumulate on top of those.
After working in this field for many years, I know where to look and start asking questions like, "Are you aware of this accumulation? How do you address it?" My goal is to get people thinking about areas they might not have considered before.
OH&S: Let's switch gears and discuss mitigation and prevention. What role does proper ventilation play in that?
Ramos: I view this through the lens of the old decision trees from my college days. On one hand, proper ventilation can be beneficial. In some environments where temperatures can soar to 95 degrees in the summer, workers tend to open roller doors, allowing a substantial airflow throughout the facility. This might help some of the dust generated from various processes to be dispersed outside, reducing confinement. Being in open-air areas can be beneficial.
However, on the flip side, that same ventilation can stir up unaddressed dust and redistribute it within the facility. So, the impact of ventilation can be two-fold – it can be advantageous or detrimental depending on the circumstances. Generally, adequate ventilation reduces confinement, and confinement is identified as one of the five factors in the dust explosion pentagon. If all these factors are present, they could trigger a dust explosion under the right conditions.
OH&S: Turning our attention to dust collection, what kind of dust collection systems should be employed in the industrial-manufacturing setting?
Ramos: When considering dust collection, you should ensure a few key aspects are in place. First, the system chosen should be tailored to address the specific application at hand. This requires an in-depth study to determine where the dust is generated, the composition of the dust, and the most effective way to eliminate it from the source area.
Secondly, the equipment used should adhere to the NFPA (National Fire Protection Association) standards.
Ramos: Lastly, it's crucial that the equipment is approved by an NRTL (nationally recognized testing laboratory). While various companies may claim their dust collection or industrial vacuum equipment is suitable for a particular setting, having external validation in the form of certification ensures the end-user that they're procuring equipment that aligns with the requisite standards and certifications.
OH&S: What should be the frequency of the dust collection?
Ramos: The frequency of dust collection can vary significantly based on the specific context. The key is to have a recurring schedule that effectively maintains low dust levels. For some facilities, if the established program is executed thoroughly, there might be longer intervals between dust collection processes. Conversely, if a facility generates a substantial amount of dust consistently, daily collection might be necessary.
In some cases, especially in facilities operating multiple shifts, workers might need to clean their respective areas at the end of each shift, leading to multiple cleanups within a day. The frequency essentially depends on the facility's operations. A well-structured and strictly adhered-to program can possibly allow for less frequent collection than one might initially assume.
OH&S: Do you have anything else that you recommend when it comes to cleaning up combustible dust in the industrial and manufacturing setting?
Ramos: There are definitely some additional considerations. Always keeping combustible dust top of mind is essential. Facilities frequently undergo changes: equipment is relocated, and processes might shift due to expansion or other factors. If you've been focusing on one specific area due to higher dust generation and then that process moves, it's vital to ensure that the new location can address the same issues. A common oversight is failing to trace back to the origin of the dust generation. If you can pinpoint where it's emanating from, there might be an opportunity to mitigate it right at the source, preventing its spread throughout the facility.
Many facilities have equipment that has been in use for a long time. This older equipment might have areas where dust can escape more readily, making it challenging to address the issue at its root. However, the goal shouldn't just be about consistent housekeeping. Instead, consider working upstream to determine the dust's origin and find ways to both mitigate it at the source and reduce the frequency of housekeeping tasks. Ultimately, the aim is to maintain low dust levels, which is the priority at the end of the day.
This article originally appeared in the September 2023 issue of Occupational Health & Safety.