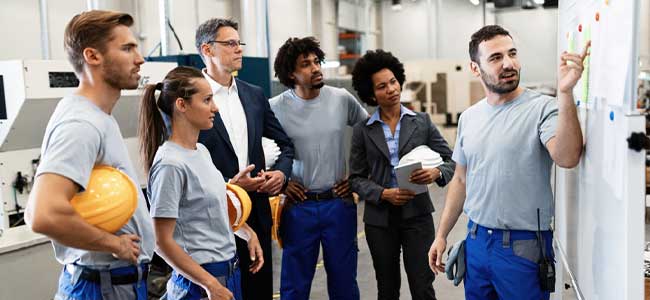
Strategies for Building a Culture of Safety
Leadership, relationships and training can all play a role in your workers’ safety, business and experience modification rate.
In the construction industry, we all come to work to support our families, but we need to go home to them, too.
This foundational idea is at the core of all successful safety programs, and it starts with leadership setting the tone and expectations. That starts with leadership taking an active, onsite role and not solely monitoring safety processes from an office somewhere. The most effective leaders are on the job sites and leading a safety department that is not structured to police policy compliance but to build relationships with field employees, customers, vendors and others so the team works together to build a trusting, safe work environment.
Engaging workers and making safety the entire team's responsibility empowers workers to make smart and safe decisions and speak up when a hazard is identified. Involve employees in safety committees and decision-making and then recognize and reward employees for their contributions to workplace safety. Any site can keep an incident-free record when all trades work together and communicate openly.
Relationship building
In creating a culture of safety, there needs to be a focus on relationship building. Team leaders need to foster a culture of trust, accountability and responsiveness when it comes to safety, demonstrating to the bigger team that the entire company is working together as a united front. It’s important to strive to be consistent in documentation and procedures so that every worker receives proper training and information regarding the present hazards. It’s also crucial to keep open lines of communication, allowing superintendents to get the support they need to safeguard their sites adequately.
Make sure you leverage opportunities to reinforce your safety commitment through special events and communication. For example, my company holds a series of safety education events during Construction Safety Week and other special observances. We use these events to plan, inspire, educate, and build relationships with all employees and field workers. When hosting events like this, consider bringing in sponsors from key manufacturing or service partners to demonstrate the newest safety features in their products and services. Hold stand-downs with industry and company leaders, but also hold stand-downs that are a little different, like a lunchtime yoga class or other wellness education. Make it a fun week that brings workers together for team-building and ongoing safety-related education. It’s a great way to bring the entire team closer and remind each other of their shared safety goals.
In addition to events, celebrate both small and large successes and milestones to reward safe practices. For example, my company's team on a complicated job site recently reached 25,000 man-hours incident-free. That milestone was a testament to the team’s diligence in keeping safety in mind and how they had worked tirelessly to ensure all proper training was obtained and best practices followed. We recognized this milestone on the job site, across the entire organization and publicly through our social media and other communication channels.
Make a Commitment to Training
In a strong, safety-focused culture, it’s recognized that a culture of safety isn’t an end goal but something to evolve and improve continually. A leadership team that recognizes this and is committed to advancing safety protocols to protect all workers at every single job site is an integral part of building a safety culture. Review and evaluate your training partners regularly to ensure your workers have the most accurate and industry-leading safety training. Is your training provider an authorized provider of continuing education credits? What about an approved course provider? These are some things to think about as you review your training resources. Implementing new technologies that proactively manage safety certifications and on-site training can help to keep safety documentation up to date and ensure that only properly certified workers are accessing a job site. A wide variety of products are available, so find the one that works for you and your team. Also, ensure your safety inspection process is constantly being updated and modified to ensure compliance with new standards and that recurring hazards are discussed and checked with each visit. Consider requiring your superintendents and project managers to complete training protocols with the broader team to educate and improve the safety conditions on site. The more eyes on safety, the more hazards you can mitigate.
Staying involved in industry association memberships offers great resources about new practices for reducing hazards and injuries; consider attending monthly committee meetings to review new and up-and-coming code changes. Designate a safety team member to stay current on service updates from local agencies and refine safety procedures to mitigate exposures and achieve compliance with local laws.
Measuring Success
Building a culture of safety can also be the foundational strategy for achieving and maintaining a lower Experience Modification Rate (EMR), a numerical rating representing how safe a business is compared to other companies. The standard EMR is 1, which is the safety rating of an average business, and for companies with safety incidents, that number will go higher than that. Conversely, if a construction business has a flawless safety record, that number goes lower than 1. A lower EMR can have several business-related benefits, including cost savings, competitive bidding advantages, and improved financial stability, and it also contributes to overall employee morale, attracting top talent, and improving worker productivity, and maintaining an EMR score below the 1.0 industry average leads to these better business results. While eliminating job site injuries is virtually impossible, many strategies can be implemented to establish a culture of safety and help lower a company’s EMR.
Obtaining a low EMR can significantly impact your company’s growth. When you can show clients, potential new hires and the insurance company that you take safety seriously, you open the door to relationships with new customers who value work being completed safely. It also brings additional work from current customers who know you as a quality partner. A low EMR can also provide access to top talent proud to work for a company dedicated to getting the job done with safety at the forefront.
How do you know progress is being made in driving down your EMR and you are establishing a culture of safety? Aside from the quantitative results like the EMR, insurance rates and overall profitability, there are qualitative measures too. For me, that moment of realization came at an elementary school choir concert. One afternoon, I left a job site for a choir concert at my daughter’s school and arrived a bit late. I tried to sneak in quietly—but the big, old creaky wooden doors drew the attention of the entire audience of parents, grandparents and others. Their attention didn’t turn back as quickly to the concert as I expected, and many attendees stared at me as I found my seat next to my wife. She immediately pointed at my outfit when I realized I had left on my safety vest. I didn’t take it off, rather proudly left it on because it’s my work uniform, just like some dads were there in business suits. At that point, I knew that our safety culture was engrained in not just my behavior but everyone who works for us.
Remember that reducing your EMR is a long-term effort requiring consistent safety and risk management dedication. It may take time to see significant improvements, but the benefits of a lower EMR can positively impact your business's bottom line and employee well-being.