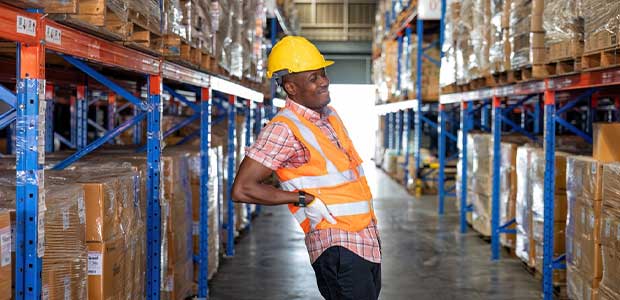
Manual Ergonomic Risk Assessments are Becoming Obsolete Due to Technology Advancements
Manually undertaking workplace ergonomic evaluations are time-consuming and hard to scale. Given the simplicity and accuracy of technology to perform the job, it’s easy to understand why paper methods are being swapped out.
- By Ashley Bauer
- Mar 08, 2023
When somebody gets injured, it impacts their entire life. They can no longer do the things they love to do outside of work. They can no longer perform their job as they used to. Sometimes, this could even lead to a victim mindset. A torn rotator cuff can become a year-long recovery process. Perhaps the person becomes addicted to pain medication. A single injury can really spiral out of control.
But what if we could proactively prevent all of that?
If we continue to follow a traditional approach to ergonomic safety, perhaps prevention on a large scale is not possible. But with recent advances in safety technology, it certainly is. Traditional ergonomic evaluations can be time-consuming and cumbersome and produce only limited insight into data trends. But technology can shoulder some of that burden.
The Problem with Traditional Ergonomic Assessments
Here is an example of a safety officer, named Rita, tasked to undertake ergonomic evaluations for a large online retailer with over 5,000 workers and multiple fulfillment warehouses spread out across the country. Rita travels a lot, trying to work through ergonomic issues across a wide range of job tasks, roles and departments. There are so many different tools and checklists that she can use, but they all take time.
She carries a heavy backpack with her to hold all the tools and equipment she needs to complete ergonomic assessments. It can take her over two hours for a single job role, observing, taking notes and measuring different tasks.
Once all data is gathered, Rita has to do something with it. She needs to analyze the information and provide recommendations, as well as collect videos and photos and compile everything into a nice, visual report.
And then even after all that, she’s only observed a single moment in time. The worker she’s observed knows they are being watched. So, it’s possible Rita doesn’t really know how they actually perform the task at all. There’s a very good chance they’re performing very well whilst they know they’re being monitored.
The time spent traveling, completing the assessment, analyzing the information and producing the report, only reflects a moment in time for one particular worker. The next day, that worker could be doing something completely different. Someone else could perform the exact same tasks in a completely different way.
Rita’s situation is a great example of understanding the challenges of traditional ergonomic evaluations. Traditional methods are time-consuming, difficult to scale and, in the end, they are very limited in their scope. The data collected only reflects a single moment in time for a particular worker. Scaling these efforts effectively in an organization with multiple sites and thousands of workers is costly, time-consuming and cumbersome.
Utilizing Technology
When Rita started using new AI-driven safety technology on the market as part of her ergonomic assessments, everything changed. Suddenly she’s able to scale her efforts across multiple jobs and sites without the need to travel so much. Technology automates the measuring and monitoring of tasks and workers, allowing Rita to access videos and data from the cloud anywhere in the world. Even data analysis is automatically generated, producing visually appealing graphs and insights easily accessible from an online dashboard.
The technology certainly helps Rita to scale her efforts, making them much more efficient, but that’s not all. It also extends the scope of her data analytics. Now she’s able to easily observe workers performing their jobs and tasks over multiple days. She’s also able to incorporate the assessment of different workers performing the same task. The technology facilitates a much wider range of data points without any additional time and cost. Rita’s ergonomic assessments are now not only much faster to complete and much less time-consuming, but they are also much more reliable, providing a breadth of data to analyze.
How Does It Work?
There are two key technologies that form the cornerstone of Rita’s proactive injury prevention safety program.
Firstly, she implemented a solution that measures and alerts workers of high-risk movements like bending, twisting, overhead reaching or open arm push and pull. It’s like having an athletic trainer at their side. Each time the worker completes a movement, a small lightweight wearable device uses built-in algorithms to calculate whether or not that movement is high risk. If it is, the worker gets alerted with real-time feedback.
Dashboard analytics enables Rita (and the organization’s management) to see data for each worker out on the warehouse floor. They can now understand their average hazards per hour, the frequency of each type of hazard, where these hazards are happening (department, job roles, etc.) and pinpoint quickly where the risk is being generated from.
Secondly, video processing provides Rita with an instant ergonomic assessment of tasks through a simple mobile application. A worker, supervisor or manager onsite simply points and shoots for immediate, in-depth data analytics. Any task is promptly analyzed, and any problem areas are clearly identified. Onsite supervisors can start coaching workers on the spot and make quick changes to tasks on the go. If a change is implemented, they can take a second video for an instant side-by-side comparison.
Rita is also able to use this to do mock-ups of changes to see how she can eliminate risks. She simply takes a video of the task as is and then tests out solutions to reduce risk by capturing a second video. Rita can compare and contrast the results side by side to demonstrate the benefit of that change before implementing it more permanently. She uses this to demonstrate that the risk reduction is significant enough to justify any associated costs with her proposed changes.
Conclusion
Ultimately, technology is just another tool in the safety arsenal of any successful operation. Technology alone is not going to solve the problem; it is not the solution. It is people who are going to solve the root cause of the problem, people like Rita, safety officers, the managers and workers on site and the executives with the power to approve spending and investment in engineering controls, but technology can certainly help us to get there.
There is not a single industry that couldn’t benefit from the technology that’s available. We all might face different hurdles depending on our industry sector, but we can all benefit from the use of it. There is only so much time in the day, and safety officers have a million things to do, especially in large organizations. The use of technology can be invaluable, making ergonomic assessments much less time-consuming and much more proactive.