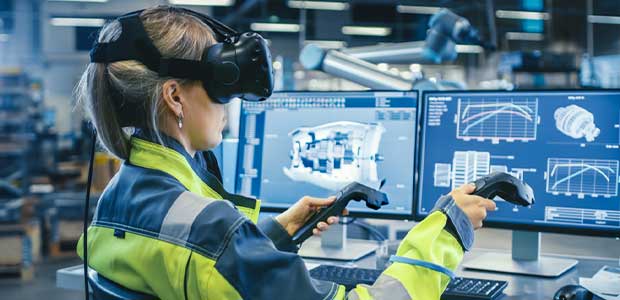
Enhancing Safety in Manufacturing with Workforce Transformation Technology
Employers can use augmented reality-enabled solutions to capture knowledge from workers.
- By Charlie Neagoy
- Sep 08, 2022
Every June for 26 years, the National Safety Council has recognized National Safety Month to increase awareness of safety hazards and accidents in the industrial workplace. However, safety can’t sleep–it’s imperative that companies maintain the focus and awareness brought by the month’s initiative year-round. According to the U.S. Bureau of Labor Statistics (BLS), there was a total of 4,764 fatal work-related injuries in 2020. Of these injuries, over a thousand occurred in the process of building and constructing infrastructure.
With the Great Resignation and an aging manufacturing workforce soon set to retire–nearly a quarter of the industry’s workforce is 55 years or older–the industry has and will continue to come face to face with the further exacerbating challenge of employee and skills gaps, which leaves remaining workers even more at risk for safety accidents and incidents. Retiring employees have amassed knowledge and honed their expertise and skills over decades of experience, enabling them to conduct their role more efficiently and safely. How can companies capture this knowledge from these subject matter experts before they leave the company? How can this knowledge be utilized to aid in onboarding, upskilling, just-in-time training and remote mentorship opportunities to existing and new workers?
Enter: Digital Transformation Technologies
Digital transformation technologies like augmented reality (AR)-enabled solutions are playing a key role in closing skills and worker gaps by creating knowledge networks that capture and preserve knowledge from senior workers, analyze that knowledge and deliver it to newer workers when and where it is needed. This approach plays and will continue to play a critical role as the manufacturing industry navigates its next frontier, one that sees employee average tenure of less than three years, as compared to the roughly ten-year average of their retiring colleagues. The coalescence of the worker shortage as employees exit the workforce and the related skills gap has created an environment where onboarding, training and access to expert knowledge have never been more critical from not only an employee health and safety standpoint, but also from an overall business outlook.
Training and Onboarding
Organizations must be prepared to continually recruit and efficiently offer on-the-job training and practical skills to ensure workforce safety and productivity regardless of employee tenure, availability and location. AR-enabled training helps retrain and upskill staff in real-time by offering critical insights required to perform any task. These technologies provide on-the-job training rapidly, safely and cost-effectively. The ability to connect less experienced workers with expert knowledge can thwart safety hazards and save thousands of hours and millions of dollars in training, travel and time.
Immediate Access to Expert Knowledge
AR-enabled technologies also provide workers the ability to get the assistance needed from the right person at the right time. It’s not always possible—or desired—to physically bring an expert employee to the site, whether this is due to availability, cost, travel restrictions or other logistic challenges.
Organizations have two options–utilize the workers available on site or physically send an expert to the site which creates cost, time, introduces increase safety risks and can propose hurdles to achieving carbon reduction goals. With the right technology, workers get the expertise they need via an expert, team member or the control center over a live video call or by following guided step-by-step work instructions. Some AR capabilities even offer data tagging and imaging, machine learning and AI computer vision to help workers quickly identify and resolve issues. Utilizing these technologies can increase efficiency and increase customer satisfaction given the opportunity cost is reduced. Organizations that are performing remote expert tasks at scale no longer have to decide to “do this job and not that one” due to expertise availability. This efficiency often increases safer outcomes as well. Many accidents occur in transit or when workers are tired or overwhelmed and overworked. Remote expert technologies can help reduce both the physical workload and the necessity of travel. Ultimately, AR aids improve operations and decrease the chances of injuries through a collaborative work atmosphere.
Conclusion: A safer, more efficient manufacturing workforce
Digital transformation technology enables companies to capture the extensive knowledge its senior industrial workers have garnered from decades on the job, and deploy that knowledge across its industrial workforce. The result? Greater safety, enhanced efficiencies and productivity, reduced carbon emissions, cost savings and more, even long after the retiring workforce punches the clock for the last time.